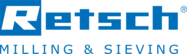
Group: VERDER Scientific

Catalog excerpts
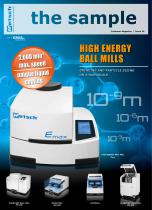
Customer Magazine | Issue 39 HIGH ENERGY BALL MILLS -1 2,000 min max . speed unique liquid cooling GRINDING AND PARTICLE SIZING ON A NANOSCALE HIGH ENERGY BALL MILL Emax PLANETARY BALL MILL PM 100 PLANETARY BALL MILL PM 400
Open the catalog to page 1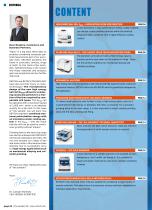
CONTENT HIGH ENERGY BALL MILL Emax – A REVOLUTION IN FINE SIZE REDUCTION A new dimension in high performance milling: 2,000 rotations per minute create ultrafine particles within the shortest amount of time, combined with a highly effective cooling system. Dear Readers, Customers and Business Partners, “Nano” is a big issue these days as products containing nanoscale particles have become part of our everyday lives. Ultrafine particles are found in sunscreen, textiles, drugs or paint, to only name a few examples. Nanotechnology is the reason why these materials and products gain new...
Open the catalog to page 2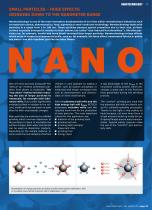
SMALL PARTICLES – HUGE EFFECTS: GRINDING DOWN TO THE NANOMETER RANGE Nanotechnology is one of the most innovative developments of our time which revolutionizes industries such as materials science, pharmaceutics, food, pigments or semi-conductor technology. Nanotechnology deals with particles in a range from 1 to 100 nm. These particles possess special properties due to their size, as their surface is greatly enlarged in relation to their volume (so-called “size-induced functionalities”). Ultrafine particles are, for example, harder and more break-resistant than larger particles....
Open the catalog to page 3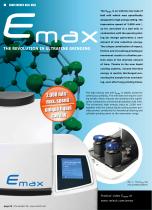
HIGH ENERGY BALL MILL The Emax is an entirely new type of ball mill which was specifically designed for high energy milling. The impressive speed of 2,000 min-1, so far unrivaled in a ball mill, in combination with the special grinding jar design generates a vast amount of size reduction energy. THE REVOLUTION IN ULTRAFINE GRINDING The unique combination of impact, friction and circulating grinding jar movement results in ultrafine particle sizes in the shortest amount of time. Thanks to the new liquid cooling system, excess thermal energy is quickly discharged preventing the sample from...
Open the catalog to page 4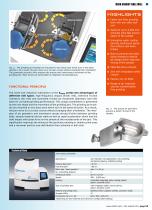
HIGH ENERGY BALL MILL Faster and finer grinding than with any other ball mill Retaining bracket Speed of up to 2,000 min-1 provides ultra-fast pulverization of the sample Innovative water cooling permits continuous operation without cool down breaks Safety screw Narrow particle size distribution thanks to special jar design which improves mixing of the sample Fig. 2: The grinding jar brackets are mounted on two discs each which turn in the same direction. As a result, the jars move on a circular course without changing their orientation. The quadruple eccentric drive ensures the precise...
Open the catalog to page 5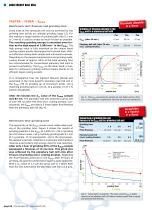
HIGH ENERGY BALL MILL FASTER – FINER – Emax In a comparative trial, the pigment titanium dioxide was pulverized in the most powerful planetary ball mill and in the Emax (50 ml grinding jar of zircomium oxide, 110 g matching grinding balls 0.1 mm Ø, 10 g sample, 15 ml 1 % sodium phosphate). After 30 minutes the d90 value of the Emax sample was 87 nm. The planetary ball mill achieved a grind size of only 476 nm after this time (excl. cooling breaks). Consequently, the Emax provided a 5 times higher final fineness than the planetary ball mill (fig. 4). Benchmark test: grinding time The...
Open the catalog to page 6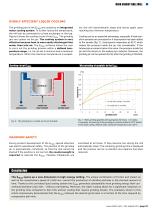
HIGH ENERGY BALL MILL HIGHLY EFFICIENT LIQUID COOLING The grinding jars of the Emax are cooled by an integrated water cooling system. To further reduce the temperature, the mill can be connected to a heat exchanger or the tap. Figure 6 shows the cooling circuit of the Emax. The grinding jars are cooled via the jar. The cooling system is very effective because heat is more easily discharged into water than into air. The Emax software allows the user to carry out the grinding process within a defined temperature range, i. e. he can set a minimum and a maximum temperature. When the maximum...
Open the catalog to page 7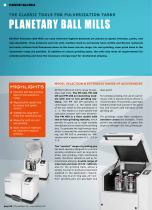
PLANETARY BALL MILLS THE CLASSIC TOOLS FOR PULVERIZATION TASKS PLANETARY BALL MILLS RETSCH Planetary Ball Mills are used wherever highest demands are placed on speed, fineness, purity, and reproducibility. They pulverize and mix soft, medium-hard to extremely hard, brittle and fibrous materials and easily achieve final finenesses down to the lower micron range. For wet grinding, even grind sizes in the nanometer range are possible. In addition to classic grinding tasks, the mills also meet all requirements for colloidal grinding and have the necessary energy input for mechanical alloying....
Open the catalog to page 8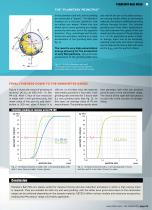
PLANETARY BALL MILLS THE “PLANETARY PRINCIPLE” In the planetary ball mill, every grinding jar represents a “planet”. This planet is located on a circular platform, the so-called sun wheel. When the sun wheel turns, every grinding jar rotates around its own axis, but in the opposite direction. Thus, centrifugal and Coriolis forces are activated, leading to a rapid acceleration of the grinding balls (see fig. 1). The result is very high pulverization energy allowing for the production of very fine particles. The enormous acceleration of the grinding balls from one wall of the jar to the other...
Open the catalog to page 9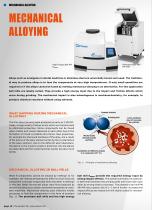
MECHANICAL ALLOYING MECHANICAL ALLOYING High Energy Ball Mill E max Planetary Ball Mill PM 400 Alloys such as amalgama in dental medicine or stainless steel are universally known and used. The traditional way to produce alloys is to fuse the components at very high temperatures. If only small quantities are required or if the alloys cannot be fused by melting mechanical alloying is an alternative. For this application ball mills are ideally suited. They provide a high energy input due to the impact and friction effects which occur during grinding. The mechanical impact is also advantageous...
Open the catalog to page 10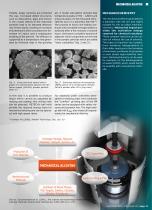
MECHANICAL ALLOYING Initially, larger particles are produced this way. Increased defect structures such as dislocations, gaps and tension in the crystal lattices of the individual particles lead to an elevated diffusion rate of their atoms, resulting in increased embrittlement which promotes the formation of cracks and a subsequent breaking of the particle. The diffusion is supported by a temperature rise generated by frictional heat in the grinding jar. A model calculation showed that temperature peaks of 700 – 1,800 K and pressure peaks of a few thousand atmospheres occur in a planetary...
Open the catalog to page 11All Retsch GmbH catalogs and technical brochures
-
General Product Overview
16 Pages
-
New Mixer Mill MM 500 vario
2 Pages
-
General Catalogue
132 Pages
-
New Mixer Mill MM 500
2 Pages
-
Emax
20 Pages
-
Ball Mills
4 Pages
Archived catalogs
-
Verder Scientific
20 Pages
-
Knife Mills GRINDOMIX
12 Pages
-
Cutting Mills
12 Pages
-
Rotor Mills
20 Pages
-
RS 200
4 Pages
-
Jaw Crushers
12 Pages
-
Biotech
4 Pages
-
Mixer Mills / CryoMill
12 Pages