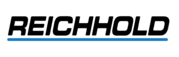
Catalog excerpts
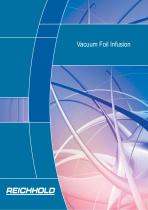
Vacuum Foil Infusion
Open the catalog to page 1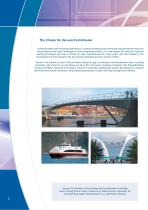
The Choice for Vacuum Foil Infusion Achieving better part functional performance, a cleaner working environment and reduced styrene exposure and emissions are major challenges for the composites industry. For that reason the need for improved working processes has been a priority for resin manufacturers for many years, and has resulted in the development of resin systems with low styrene emissions and low styrene content. Vacuum Foil Infusion is one of the processes filling the gap in production volume between open moulding processes, like Hand lay up and Spray up (HLU/ SU) and press...
Open the catalog to page 2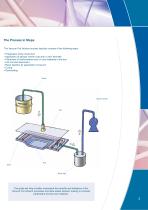
The Vacuum Foil Infusion process typically consists of the following steps: • Preparation of the mould tool • Application of gelcoat, barrier coat and/ or skin laminate • Placement of reinforcement and/ or core materials in the tool • Foil and seal placement • Resin injection by application of vacuum Resin trap This guide will help to better understand the benefits and limitations of the Vacuum Foil Infusion processes and allow easier decision making on process
Open the catalog to page 3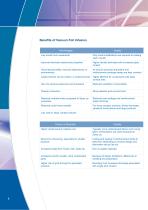
Low mould/ tool investments open moulds Improved laminate mechanical properties Higher density laminates with increased glass content Good reproducibility: reduced dependence on workmanship As long as process parameters and reinforcement package design are kept constant Large products can be made in a closed process Highly effective for components with large surface area Very low styrene exposures and emissions Reduced ventilation cost possible Cleaner production More pleasant work environment Reduced material waste compared to Spray up processes Reduced resin spillage and reinforcement...
Open the catalog to page 4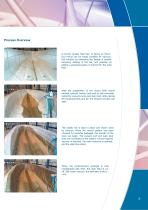
Process Overview A normal, female Hand lay- or Spray up (HLU/ SU) mould can be easily modified for Vacuum Foil Infusion by extending the flange to enable clamping/ sealing of the foil, and possibly by adding a peripheral gate or channel for the resin After the preparation of the mould (with mould release, gelcoat, barrier coat and/ or skin laminate), install the vacuum pump and resin trap; after placing the reinforcements and foil, the infusion process can The plastic foil is kept in place and drawn down by vacuum. When the 'mould system' has been checked for possible leakages, the transfer...
Open the catalog to page 5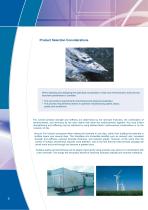
Product Selection Considerations When selecting and designing the optimised combination of resin and reinforcement, there are two important parameters to consider: • The end product requirements (mechanical and physical properties) • The process requirements (desire to optimise manufacturing speed, labour, The overall laminate strength and stiffness are determined by the laminate thickness, the combination of reinforcements, and obviously by the resin matrix that holds the reinforcements together. Any local further strengthening and stiffening may be obtained by using tailored fabric/...
Open the catalog to page 6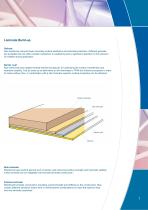
Laminate Build-up Non-reinforced coloured layer providing surface aesthetics and laminate protection. Different gelcoats are available that can offer excellent protection to weathering and a significant reduction in the emission of volatiles during application. Barrier coat Non-reinforced layer applied directly behind the gelcoat, for optimising the surface smoothness and hydrolytic stability. Can be used as an alternative to skin laminates in RTM and infusion processes in order to reduce labour time. In combination with a skin laminate superior surface properties can be obtained. nfusion...
Open the catalog to page 7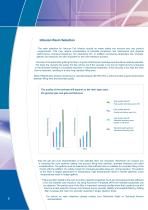
Infusion Resin Selection The resin selection for Vacuum Foil Infusion should be made taking into account end use product requirements. This may require consideration of laminate properties, like mechanical and physical performance, chemical resistance, fire retardancy etc. In addition processing parameters like viscosity, geltime and reactivity are also important for the resin selection process. Viscosity is the parameter guiding the flow in a given reinforcement package and should be carefully selected. The lower the viscosity the easier the flow will be, but if the viscosity is too low...
Open the catalog to page 8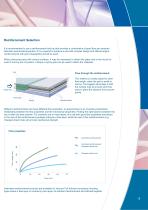
Reinforcement Selection It is recommended to use a reinforcement build-up that provides a combination of good flow and required laminate mechanical properties. If it is required to produce a part with complex design and difficult angles, reinforcements with good drapeability should be used. When producing parts with vertical surfaces, it may be necessary to attach the glass mat to the mould to avoid it moving out of position. Clamps or spray glue can be used to attach the materials. Resin flow Flow through the reinforcement This method is mostly suited for short flow length, when the part...
Open the catalog to page 9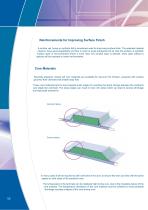
Reinforcements for Improving Surface Finish A surface veil, tissue or synthetic felt is sometimes used for improving surface finish. The selected material needs to have good drapeability and flow in order to avoid entrapment of air near the surface. A synthetic surface layer is recommended where a more resin rich surface layer is desired, when parts without a gelcoat will be exposed to harsh environments. Core Materials Specially prepared, closed cell core materials are available for Vacuum Foil Infusion, prepared with surface grooves/ flow channels that enable easy flow. These core...
Open the catalog to page 10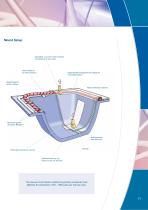
Mould Setup Adjustable vacuum for resin transport (connected to a resin trap) Helical tubes for air/ resin transport one single infusion Sealant tape for vacuum closure Resin distribution channel (so-called ‘Bleeders’) Resin feed channel by vacuum Standard Hand lay up/ Spray up tool can be used The Vacuum Foil Infusion method is typically considered cost effective for production of 50 - 1000 parts per tool per year.
Open the catalog to page 11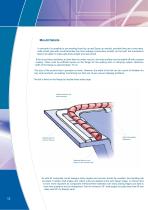
Mould Details In principle it is possible to use existing Hand lay up and Spray up moulds, provided they are a one piece, solid mould type with mould laminate free from leakage (multi-piece moulds can be built, but precautions need to be taken to make split-lines airtight and leak proof). If the mould has a tendency to draw false air under vacuum, the outer surface can be sealed off with a proper coating. There must be sufficient space on the flange for the sealing and/ or clamping system. Minimum width of the flange is approximately 15 cm. The size of the product has in principle no...
Open the catalog to page 12All Reichhold catalogs and technical brochures
-
UROTUF® F275-M-75
2 Pages
-
EPOTUF® 38-698
2 Pages
-
F600-W-40
2 Pages
-
UROTUF®
7 Pages
-
DION® IMPACT 9133
2 Pages
-
UROTUF® Water-borne Urethane
4 Pages
-
BioiPreferred® Guideline
2 Pages
-
NORPOL® ULTIMATE GELCOAT
2 Pages
-
NORPOL® SVX Gelcoat
2 Pages
-
NORPOL® SVG Gelcoats
3 Pages
-
NEW NORPOL® SRG GELCOAT
2 Pages
-
DION® Corrosion Guide
45 Pages
-
POLYLITE ® 3354225
3 Pages
-
EPOTUF® 38-698
2 Pages
-
Improved vinyl ester technology
21 Pages
-
UROTUF® F600-W-40
2 Pages
-
UROTUF® E300-W-40
2 Pages
-
Corrosion Guide
45 Pages
-
Coating Resins Catalog
35 Pages
-
BECKOSOL AQ®
12 Pages
-
AROFLINT® Flyer
2 Pages
-
Material Selection Guide
77 Pages
-
FRP Inspection Guide
36 Pages
-
RTM Light
15 Pages
-
Pultrusion (Europe)
3 Pages
-
A Reichhold Company Overview
11 Pages
-
NORPOL® VBC Barriercoat
3 Pages
-
NORPOL® GI
3 Pages
-
NORPOL® CPG
4 Pages
-
Pultrusion (EMEA)
3 Pages
-
NORPOL® SVG Gelcoats
4 Pages
-
Fire Retardant (EMEA)
15 Pages
-
Bonding Paste (EMEA)
15 Pages
Archived catalogs
-
Vacuum Foil/ RTM Process (EMEA)
11 Pages
-
Tooling System (EMEA)
11 Pages
-
SMC/ BMC (EMEA)
3 Pages