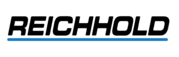
Catalog excerpts
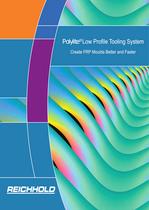
Polylite® Low Profile Tooling System Create FRP Moulds Better and Faster
Open the catalog to page 1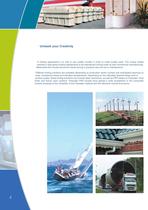
Unleash your Creativity 2 In tooling applications it is vital to use quality moulds in order to make quality parts. The unique shape requires a high gloss surface appearance to be reproduced during scale up and commercial manufacturing. Meanwhile the moulds should be robust during in practical use and low in maintenance. Different tooling solutions are available depending on production series number and anticipated exposure to wear, mechanical stress and elevated temperatures. Depending on the ultimately desired shape and/ or surface quality, these tooling solutions can include steel,...
Open the catalog to page 2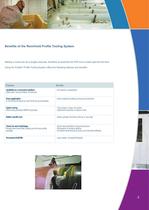
Benefits of the Reichhold Profile Tooling System Making a mould can be a lengthy exercise, therefore its essential the FRP tool is made right the first time. Using the Polylite® Profile Tooling System offers the following features and benefits: Features Benefits Available as a one-pack solution (filled resin, pre-promoted, thixotropic) - No hassle in preparation Easy application in conventional spray-up and hand lay-up processes - Easy material handling during tool production Quick curing whilst using standard MEKP peroxides - Tools ready in days not weeks - Significant reduction in labour...
Open the catalog to page 3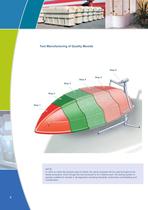
Tool Manufacturing of Quality Moulds NOTE: In order to make the process easy to follow, the same example will be used throughout the whole procedure. Even though the tool produced is for a Marine part, the tooling system is equally suitable for moulds in all segments including Industrial, Automotive and Building and Construction. 4 Step 1 Step 2 Step 3 Step 4 Step 5 Step 6
Open the catalog to page 4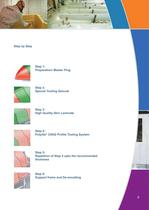
Step by Step Step 1: Prparation/ Master Plug Step 2: Spcial Tooling Gelcoat Step 3: High Quality Skin Laminate Step 4: Polylite® 33542 Profile Tooling System Step 5: Repetition of Step 4 upto the recommended thickness Step 6: Support frame and De-moulding
Open the catalog to page 5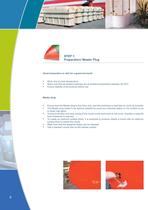
Good preparation is vital for a good end result • Work only at room temperature • Make sure that all needed materials are at ambient temperature between 20-23ºC • Ensure stability of all products before use Master plug: • Ensure that the Master plug is free from dust, and the workshop is dust-free as much as possible • The Master plug needs to be styrene resistant to avoid any chemical attack on the surface so as to retain high gloss • During production and post curing of the mould some heat build-up will occur, therefore a specific heat resistance is required • To create an optimum surface...
Open the catalog to page 6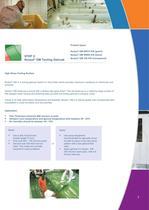
STEP 2: Norpol® GM Tooling Gelcoat Product types: Norpol® GM 60014 H/S (green) Norpol® GM 90000 H/S (black) Norpol® GM 100 H/S (transparent) High Gloss Tooling Surface Norpol® GM is a tooling gelcoat based on Vinyl Ester which provides maximum rsistance to chemicals and solvents. Norpol® GM produces a mould with a lasting high gloss finish. This will stand up to a relatively large number of lifts between each waxing and polishing step provided the tooling gelcoat is properly cured. Owing to its high deformation temperature and flexibility, Norpol® GM is a robust quality and consequently...
Open the catalog to page 7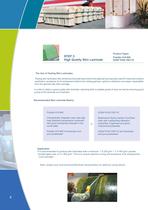
Product Types: Polylite® 410-900 DION® 9100-700/710 STEP 3: High Quality Skin Laminate DION® 9100-700/710 Bisphenol-A Epoxy based Vinyl Ester resin with outstanding adhesion properties, toughness and good mechanical properties DION® 9100-700/710 are thixotropic and pre-accelerated or 8 Polylite® 410-900 Orthophthalic Polyester resin with high heat distortion temperature combined with good mechanical strength in the cured state Polylite® 410-900 is thixotropic and pre-accellerated The Use of Tooling Skin Laminates Tooling skin laminates (the reinforced laminate layer behind the gelcoat) are...
Open the catalog to page 8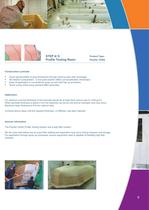
STEP 4/ 5: Profile Tooling Resin Product Type: Polylite* 33542 Construction Laminate Good reproducibility of plug dimensions through close-to-zero resin shrinkage Օ No hassle in preparation - a one-pack solution (filled, pre-accelerated, thixotropic) Ease of application in conventional spray up and hand lay up processes Օ Quick curing whilst using standard MEK peroxides Application For optimum cure the thickness of the laminate should be at least 4mm wet-on-wet (3 x 450 g/m2). When laminate thickness is below 4 mm the reactivity can be too low and an improper cure may occur. Maximum layer...
Open the catalog to page 9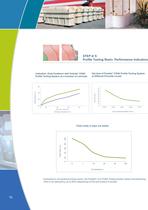
Peak Exotherm (*C) 20 40 60 80 Workshop Temperature (*C) 6 mm 4 mm 0 15 20 25 30 Gel Time (min.) Cured with Standard MEKP at 23*C 0 10 20 30 40 50 60 70 0,75% 1,00% 1,25% 1,50% 1,75% Total Time in % Tool Surface m2 0 20 40 60 80 100 0 1 10 20 50 100 Compared to conventional tooling resins, the Polylite® Low Profile Tooling System allows manufacturing time to be reduced by up to 80% (depending on the tool surface involved). STEP 4/ 5: Profile Tooling Resin: Performance Indicators Gel time of Polylite® 33542 Profile Tooling System at Different Peroxide Levels Indication: Peak Exotherm with...
Open the catalog to page 10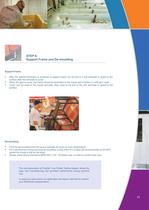
Support Frame After the desired thickness is achieved, a support frame can be laid in a wet laminate or glued to the surface after the laminate is cured. Օ When the glue is cured, the frame should be laminated to the mould with a further 3 x 450 g/m2 layer. Cores can be used in the mould laminate, they need to be laid in the wet laminate or glued to the surface. De-moulding Օ Time for de-moulding from the plug is typically 24 hours at room temperature. For improved tool curing and plug de-moulding, curing times of 2-3 days are recommended at 35-40°C (whilst the mould is still on the...
Open the catalog to page 11All Reichhold catalogs and technical brochures
-
UROTUF® F275-M-75
2 Pages
-
EPOTUF® 38-698
2 Pages
-
F600-W-40
2 Pages
-
UROTUF®
7 Pages
-
DION® IMPACT 9133
2 Pages
-
UROTUF® Water-borne Urethane
4 Pages
-
BioiPreferred® Guideline
2 Pages
-
NORPOL® ULTIMATE GELCOAT
2 Pages
-
NORPOL® SVX Gelcoat
2 Pages
-
NORPOL® SVG Gelcoats
3 Pages
-
NEW NORPOL® SRG GELCOAT
2 Pages
-
DION® Corrosion Guide
45 Pages
-
POLYLITE ® 3354225
3 Pages
-
EPOTUF® 38-698
2 Pages
-
Improved vinyl ester technology
21 Pages
-
UROTUF® F600-W-40
2 Pages
-
UROTUF® E300-W-40
2 Pages
-
Corrosion Guide
45 Pages
-
Coating Resins Catalog
35 Pages
-
BECKOSOL AQ®
12 Pages
-
AROFLINT® Flyer
2 Pages
-
Material Selection Guide
77 Pages
-
FRP Inspection Guide
36 Pages
-
Vacuum Foil Infusion
19 Pages
-
RTM Light
15 Pages
-
Pultrusion (Europe)
3 Pages
-
A Reichhold Company Overview
11 Pages
-
NORPOL® VBC Barriercoat
3 Pages
-
NORPOL® GI
3 Pages
-
NORPOL® CPG
4 Pages
-
Pultrusion (EMEA)
3 Pages
-
NORPOL® SVG Gelcoats
4 Pages
-
Fire Retardant (EMEA)
15 Pages
-
Bonding Paste (EMEA)
15 Pages
Archived catalogs
-
Vacuum Foil/ RTM Process (EMEA)
11 Pages
-
SMC/ BMC (EMEA)
3 Pages