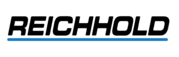
Catalog excerpts
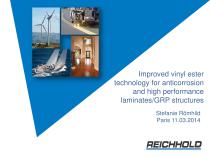
Improved vinyl ester technology for anticorrosion and high performance laminates/GRP structures Stefanie Römhild Paris 11.03.2014
Open the catalog to page 1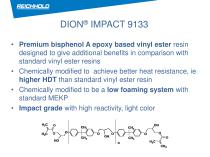
DION® IMPACT 9133 • Premium bisphenol A epoxy based vinyl ester resin designed to give additional benefits in comparison with standard vinyl ester resins • Chemically modified to achieve better heat resistance, ie higher HDT than standard vinyl ester resin • Chemically modified to be a low foaming system with standard MEKP • Impact grade with high reactivity, light color
Open the catalog to page 2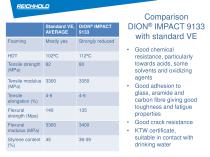
Standard VE, DION® IMPACT AVERAGE 9133 Foaming Strongly reduced Tensile elongation (%) Styrene content (%) Comparison DION® IMPACT 9133 with standard VE • Good chemical resistance, particularly towards acids, some solvents and oxidizing agents • Good adhesion to glass, aramide and carbon fibre giving good toughness and fatigue properties • Good crack resistance • KTW certificate, suitable in contact with drinking water
Open the catalog to page 3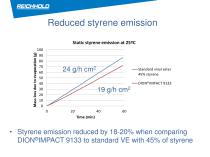
Reduced styrene emission • Styrene emission reduced by 18-20% when comparing DION®IMPACT 9133 to standard VE with 45% of styrene
Open the catalog to page 4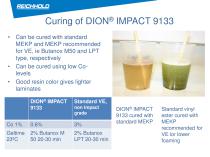
Curing of DION® IMPACT 9133 • Can be cured with standard MEKP and MEKP recommended for VE, ie Butanox M50 and LPT type, respectively • Can be cured using low Colevels • Good resin color gives lighter laminates DION® IMPACT 9133 DION® IMPACT 9133 cured with standard MEKP Standard vinyl ester cured with MEKP recommended for VE lor lower foaming
Open the catalog to page 5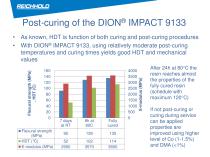
Post-curing of the DION® IMPACT 9133 Flexural strength (MPa) HDT (°C) E-modulus (MPa) Fully cured • As known, HDT is function of both curing and post-curing procedures • With DION® IMPACT 9133, using relatively moderate post-curing temperatures and curing times yields good HDT and mechanical values After 24h at 80C the resin reaches almost the properties of the fully cured resin (schedule with maximum 120C) If not post-curing or curing during service can be applied properties are improved using higher level of Co (1-1.5%) and DMA (<1%)
Open the catalog to page 6
Mechanical properties at 80C – clear casts 3000 Flexural strengh (MPa) Tensile strength (MPa) Tensile elongation (%) HDT Flexural modulus (MPa) Tensile modulus (MPa) DION® IMPACT 9133 and standard VE clear casts cured with Co and Butanox LPT, post-cured at 80C
Open the catalog to page 7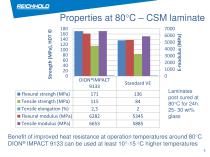
Flexural strengh (MPa) Tensile strength (MPa) Tensile elongation (%) Flexural modulus (MPa) Tensile modulus (MPa) Laminates post cured at 80C for 24h. 25- 30 wt% glass Benefit of improved heat resistance at operation temperatures around 80C DION® IMPACT 9133 can be used at least 10-15 C higher temperatures 8
Open the catalog to page 8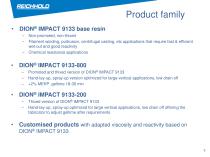
Product family • DION® IMPACT 9133 base resin – – – Non-promoted, non-thixed Filament winding, pultrusion, centrifugal casting, etc applications that require fast & efficient wet-out and good reactivity Chemical resistance applications Promoted and thixed version of DION® IMPACT 9133 Hand-lay-up, spray-up version optimized for large vertical applications, low drain off +2% MEKP geltime 18-30 min Thixed version of DION® IMPACT 9133 Hand-lay-up, spray-up optimized for large vertical applications, low drain off offering the fabricator to adjust geltime after requirements • Customised products...
Open the catalog to page 9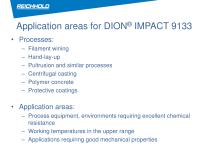
Application areas for DION® IMPACT 9133 • Processes: – – – – – – Filament wining Hand-lay-up Pultrusion and similar processes Centrifugal casting Polymer concrete Protective coatings • Application areas: – Process equipment, environments requiring excellent chemical resistance – Working temperatures in the upper range – Applications requiring good mechanical properties
Open the catalog to page 10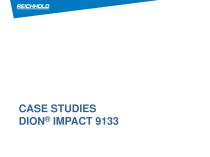
CASE STUDIES DION® IMPACT 9133
Open the catalog to page 11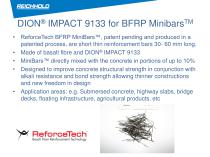
DION® IMPACT 9133 for BFRP MinibarsTM • ReforceTech BFRP MiniBars™, patent pending and produced in a patented process, are short thin reinforcement bars 30- 60 mm long. • Made of basalt fibre and DION® IMPACT 9133 • MiniBars™ directly mixed with the concrete in portions of up to 10% • Designed to improve concrete structural strength in conjunction with alkali resistance and bond strength allowing thinner constructions and new freedom in design • Application areas: e.g. Submersed concrete, highway slabs, bridge decks, floating infrastructure, agricultural products, etc
Open the catalog to page 12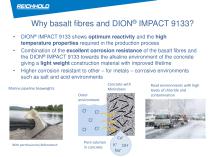
Why basalt fibres and DION® IMPACT 9133? • • DION® IMPACT 9133 shows optimum reactivity and the high temperature properties required in the production process Combination of the excellent corrosion resistance of the basalt fibres and the DION® IMPACT 9133 towards the alkaline environment of the concrete giving a light weight construction material with improved lifetime Higher corrosion resistant to other – for metals – corrosive environments such as salt and acid environments Concrete with Minirebars Marine pipeline Seaweights Outer environment With permission by Reforcetech Pore solution...
Open the catalog to page 13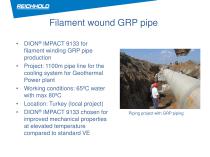
Filament wound GRP pipe • DION® IMPACT 9133 for filament winding GRP pipe production • Project: 1100m pipe line for the cooling system for Geothermal Power plant • Working conditions: 65ºC water with max 80ºC • Location: Turkey (local project) • DION® IMPACT 9133 chosen for improved mechanical properties at elevated temperature compared to standard VE Piping project with GRP piping
Open the catalog to page 14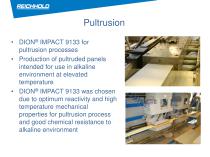
Pultrusion • DION® IMPACT 9133 for pultrusion processes • Production of pultruded panels intended for use in alkaline environment at elevated temperature • DION® IMPACT 9133 was chosen due to optimum reactivity and high temperature mechanical properties for pultrusion process and good chemical resistance to alkaline environment
Open the catalog to page 15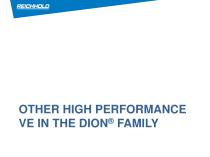
OTHER HIGH PERFORMANCE VE IN THE DION® FAMILY
Open the catalog to page 16
DION® 9400/ DION® IMPACT 9400 – Novolac bisphenol A epoxybased vinyl ester resin – HDT 135C – Improved high temperature performance – Retains mechanical properties at elevated temperatures – Low color and high reactivity for Impact grade – Resists organic solvents – Good resistance to many oxidising environments – An economical alternative to exotic metal alloys Case study Transport tanks for chemical industry Selcotec Norway Various corrosive environments Dion 9400 offers good corrosion resistance to different environments and good mechanical properties
Open the catalog to page 17All Reichhold catalogs and technical brochures
-
UROTUF® F275-M-75
2 Pages
-
EPOTUF® 38-698
2 Pages
-
F600-W-40
2 Pages
-
UROTUF®
7 Pages
-
DION® IMPACT 9133
2 Pages
-
UROTUF® Water-borne Urethane
4 Pages
-
BioiPreferred® Guideline
2 Pages
-
NORPOL® ULTIMATE GELCOAT
2 Pages
-
NORPOL® SVX Gelcoat
2 Pages
-
NORPOL® SVG Gelcoats
3 Pages
-
NEW NORPOL® SRG GELCOAT
2 Pages
-
DION® Corrosion Guide
45 Pages
-
POLYLITE ® 3354225
3 Pages
-
EPOTUF® 38-698
2 Pages
-
UROTUF® F600-W-40
2 Pages
-
UROTUF® E300-W-40
2 Pages
-
Corrosion Guide
45 Pages
-
Coating Resins Catalog
35 Pages
-
BECKOSOL AQ®
12 Pages
-
AROFLINT® Flyer
2 Pages
-
Material Selection Guide
77 Pages
-
FRP Inspection Guide
36 Pages
-
Vacuum Foil Infusion
19 Pages
-
RTM Light
15 Pages
-
Pultrusion (Europe)
3 Pages
-
A Reichhold Company Overview
11 Pages
-
NORPOL® VBC Barriercoat
3 Pages
-
NORPOL® GI
3 Pages
-
NORPOL® CPG
4 Pages
-
Pultrusion (EMEA)
3 Pages
-
NORPOL® SVG Gelcoats
4 Pages
-
Fire Retardant (EMEA)
15 Pages
-
Bonding Paste (EMEA)
15 Pages
Archived catalogs
-
Vacuum Foil/ RTM Process (EMEA)
11 Pages
-
Tooling System (EMEA)
11 Pages
-
SMC/ BMC (EMEA)
3 Pages