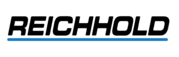
Catalog excerpts
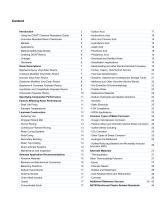
- Using the DION® Chemical Resistance Guide 4 - Hydrochloric Acid 18 - Corrosion-Resistant Resin Chemistries 5 - Nitric and Chromic Acid 18 -Markets 5 - Hydrofluoric Acid 18 -Applications 5 -Acetic Acid 18 - Material Safety Data Sheets 5 - Perchloric Acid 18 -Ordering DION® Resins 6 - Phosphoric Acid 18 -Changes 6 - Deionized and Distilled Water 19 -Disclaimer 6 - Desalination Applications 19 7 - Electroplating and other Electrochemical Processes 19 7 - Fumes, Vapors, Hood & Duct Service 20 8 - Gasoline, Gasohol and Underground Storage Tanks 21 11 - Sodium Hydroxide and Alkaline Solutions...
Open the catalog to page 2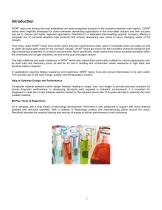
Introduction DION® resins are among the most established and best-recognized products in the corrosion-resistant resin market. DION® resins were originally developed for some extremely demanding applications in the chlor-alkali industry and their success has led to diverse and highly regarded applications. Reichhold is a dedicated thermosetting polymer company offering a complete line of corrosion-resistant resin products and actively developing new resins to serve changing needs of the industry. Over many years DION® resins have shown good long term performance when used in composite tanks...
Open the catalog to page 3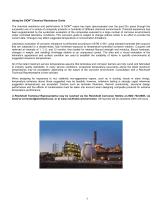
Using the DION® Chemical Resistance Guide The chemical resistance and performance of DION® resins has been demonstrated over the past 50+ years through the successful use of a variety of composite products in hundreds of different chemical environments. Practical experience has been supplemented by the systematic evaluation of the composites exposed to a large number of corrosive environments under controlled laboratory conditions. This corrosion guide is subject to change without notice in an effort to provide the current data. Changes may affect suggested temperature or concentration...
Open the catalog to page 4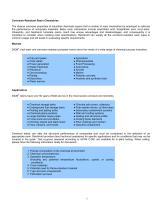
Corrosion-Resistant Resin Chemistries The diverse corrosive properties of industrial chemicals require that a number of resin chemistries be employed to optimize the performance of composite materials. Basic resin chemistries include isophthalic acid, terephthalic acid, vinyl ester, chlorendic, and bisphenol fumarate resins. Each has unique advantages and disadvantages, and consequently it is important to consider when creating resin specifications. Reichhold can supply all the corrosion-resistant resin types in common usage and will assist in evaluating specific requirements. Markets DION®...
Open the catalog to page 5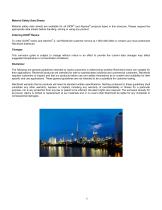
Material Safety Data Sheets Material safety data sheets are available for all DION® and Atprime® products listed in this brochure. Please request the appropriate data sheets before handling, storing or using any product. Ordering DION® Resins To order DION® resins and Atprime® 2, call Reichhold customer service at 1-800-448-3482 or contact your local authorized Reichhold distributor. Changes This corrosion guide is subject to change without notice in an effort to provide the current data changes may affect suggested temperature or concentration limitations. Disclaimer The following are...
Open the catalog to page 6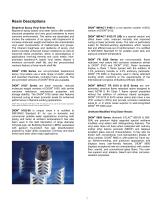
Resin Descriptions DION® IMPACT 9160 is a low styrene content (<35%) version of DION® 9100. Bisphenol Epoxy Vinyl Ester Resins Bisphenol epoxy based vinyl ester resins offer excellent structural properties and very good resistance to many corrosive environments. The resins are styrenated and involve the extension of an epoxy with bisphenol-A to increase molecular weight and feature the characteristic vinyl ester incorporation of methacrylate end groups. The inherent toughness and resilience of epoxy vinyl esters provides enhanced impact resistance as well as improved stress properties,...
Open the catalog to page 7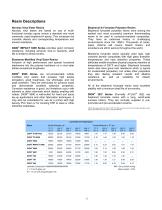
Resin Descriptions Novolac Vinyl Ester Resins Novolac vinyl esters are based on use of multifunctional novolac epoxy versus a standard and more commonly used bisphenol-A epoxy. This increases the crosslink density and corresponding temperature and solvent resistance. Bisphenol-A Fumarate Polyester Resins Bisphenol fumarate polyester resins were among the earliest and most successful premium thermosetting resins to be used in corrosion-resistant composites. They have an extensive history in challenging environments since the 1950’s. Thousands of tanks, pipes, chlorine cell covers, bleach...
Open the catalog to page 8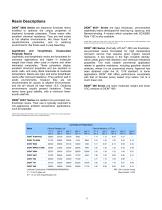
Resin Descriptions DION® 6694 Series are bisphenol fumarate resins modified to optimize the unique properties of bisphenol fumarate polyesters. These resins offer excellent chemical resistance. They are well suited to hot alkaline environments, like those found in caustic/chlorine production, and to oxidizing environments, like those used in pulp bleaching. DION® 6631* Series are rigid, thixotropic, pre-promoted isophthalic resins developed for hand lay-up, spray-up, and filament-winding. A version which complies with SCAQMD Rule 1162 is also available. ® *DION 6631 comply with FDA Title 21...
Open the catalog to page 9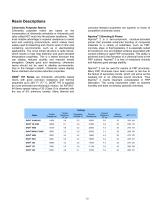
Resin Descriptions corrosion-resistant properties are superior to those of competitive chlorendic resins. Chlorendic Polyester Resins Chlorendic polyester resins are based on the incorporation of chlorendic anhydride or chlorendic acid (also called HET acid) into the polymer backbone. Their most notable advantage is superior resistance to mixed acid and oxidizing environments, which makes them widely used for bleaching and chromic acid or nitric acid containing environments, such as in electroplating applications. The cross linked structure is quite dense, which results in high heat...
Open the catalog to page 10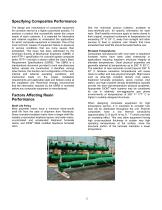
Specifying Composites Performance The design and manufacture of composite equipment for corrosion service is a highly customized process. To produce a product that successfully meets the unique needs of each customer, it is essential for fabricators and material suppliers to understand the applications for which composite equipment is intended. One of the most common causes of equipment failure is exposure to service conditions that are more severe than anticipated. This issue has been addressed by the American Society of Mechanical Engineers (ASME) in their RTP-1 specification for...
Open the catalog to page 11All Reichhold catalogs and technical brochures
-
UROTUF® F275-M-75
2 Pages
-
EPOTUF® 38-698
2 Pages
-
F600-W-40
2 Pages
-
UROTUF®
7 Pages
-
DION® IMPACT 9133
2 Pages
-
UROTUF® Water-borne Urethane
4 Pages
-
BioiPreferred® Guideline
2 Pages
-
NORPOL® ULTIMATE GELCOAT
2 Pages
-
NORPOL® SVX Gelcoat
2 Pages
-
NORPOL® SVG Gelcoats
3 Pages
-
NEW NORPOL® SRG GELCOAT
2 Pages
-
POLYLITE ® 3354225
3 Pages
-
EPOTUF® 38-698
2 Pages
-
Improved vinyl ester technology
21 Pages
-
UROTUF® F600-W-40
2 Pages
-
UROTUF® E300-W-40
2 Pages
-
Corrosion Guide
45 Pages
-
Coating Resins Catalog
35 Pages
-
BECKOSOL AQ®
12 Pages
-
AROFLINT® Flyer
2 Pages
-
Material Selection Guide
77 Pages
-
FRP Inspection Guide
36 Pages
-
Vacuum Foil Infusion
19 Pages
-
RTM Light
15 Pages
-
Pultrusion (Europe)
3 Pages
-
A Reichhold Company Overview
11 Pages
-
NORPOL® VBC Barriercoat
3 Pages
-
NORPOL® GI
3 Pages
-
NORPOL® CPG
4 Pages
-
Pultrusion (EMEA)
3 Pages
-
NORPOL® SVG Gelcoats
4 Pages
-
Fire Retardant (EMEA)
15 Pages
-
Bonding Paste (EMEA)
15 Pages
Archived catalogs
-
Vacuum Foil/ RTM Process (EMEA)
11 Pages
-
Tooling System (EMEA)
11 Pages
-
SMC/ BMC (EMEA)
3 Pages