Catalog excerpts
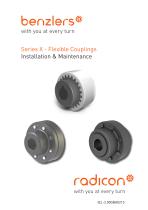
with you at every turn Series X - Flexible Couplings Installation & Maintenance with you at every turn
Open the catalog to page 1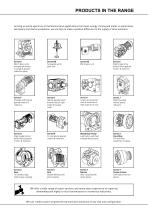
Serving an entire spectrum of mechanical drive applications from food, energy, mining and metal; to automotive, aerospace and marine propulsion, we are here to make a positive difference to the supply of drive solutions. Series A Worm Gear units and geared motors in single & double reduction types Series BD Screwjack worm gear unit Series BS Worm gear unit Series C Right angle drive helical worm geared motors & reducers Series F Parallel shaft helical geared motors & reducers Series G Helical parallel shaft & bevel helical right angle drive gear units Series H Large helical parallel shaft &...
Open the catalog to page 2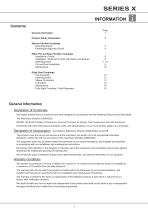
INFORMATIONContents: Page Product Safety Information 2 Nylicon Flexible Couplings Assembly Details 4 Permissible Alignment Errors 4 Elflex Pin and Bush Flexible Couplings Installation of Hubs 6 Installation / Removal of Hubs with Taper Lock Bushes 6 Elign Gear Couplings Hub Assembly 12 Fully Rigid Couplings - Shaft Alignment 16 General Information Declaration of Conformity We hereby declare that our products have been designed in accordance with the following Directives and Standards: The Machinery Directive 2006/42/EC EN ISO 12100:2010 Safety of Machinery. General...
Open the catalog to page 3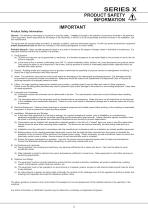
PRODUCT SAFETY INFORMATION Product Safety Information General - The following information is important in ensuring safety. It must be brought to the attention of personnel involved in the selection of the equipment, those responsible for the design of the machinery in which it is to be incorporated and those involved in its installation, use and maintenance. The equipment will operate safely provided it is selected, installed, used and maintained properly. As with any power transmission equipment proper precautions must be taken as indicated in the following paragraphs, to ensure safety....
Open the catalog to page 4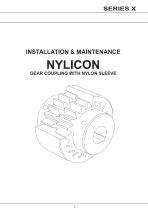
INSTALLATION & MAINTENANCE GEAR COUPLING WITH NYLON SLEEVE
Open the catalog to page 5
NYLICON COUPLING INSTALLATION OF NYLICON GEAR TYPE FLEXIBLE COUPLINGS Errors of alignment fall into categories of angularity and eccentricity, or a combination of both. While the NYLICON gear type flexible coupling compensates for a certain amount of misalignment, its life is greatly Increased if any errors present are reduced as much as possible. It is important, therefore to check the coupling for alignment with the setting gauge supplied before tightening the grub screws in the two hubs on their respective shafts. The gauge should be placed on the coupling as shown above. Check for...
Open the catalog to page 6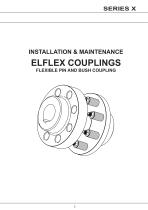
INSTALLATION & MAINTENANCE ELFLEX COUPLINGS FLEXIBLE PIN AND BUSH COUPLING
Open the catalog to page 7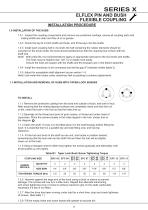
1.0.1 Inspect the coupling components and remove any protective coatings, ensure all coupling parts and mating shafts are clean and free of oil or grease. 1.0.2 Check the key fit in both shafts and hubs, and fit the keys into the shafts 1.0.3 Install each coupling half on its shaft, the half containing the rubber elements should be mounted on the driven shaft, the hubs should positioned so that the coupling face is flush with the shaft end Note! With press fits it is recommended to apply an appropriate lubricant to the hub bores and shafts, The hubs may be heated (max 120° C) to install...
Open the catalog to page 8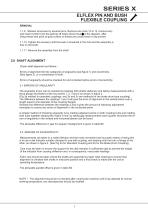
ELFLEX PIN AND BUSH FLEXIBLE COUPLING REMOVAL 1.1.9 Slacken all screws by several turns. Remove one (size 12 to 13, remove two) and insert it (them) into the jacking off holes shown thus in the diagram, after oiling thread and point of grub screws or thread and under head of cap screws. 1.1.10 Tighten the screw(s) until the bush is loosened in the hub and the assembly is free on the shaft. 1.1.11 Remove the assembly from the shaft. Check shaft alignment as follows:- Errors of alignment fall into categories of angularity (see figure 1) and eccentricity (See figure 2), or a combination of...
Open the catalog to page 9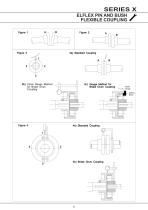
ELFLEX PIN AND BUSH FLEXIBLE COUPLING A 3b) Clock Gauge Method for Brake Drum Coupling 3c) Gauge Method for Brake Drum Coupling 4b) Brake Drum Coupling Setting Block
Open the catalog to page 10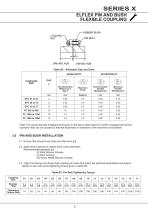
ELFLEX PIN AND BUSH FLEXIBLE COUPLING Table B2 Allowable Gap and Error
Open the catalog to page 11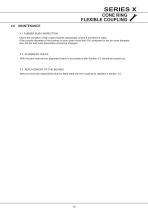
CONE RING FLEXIBLE COUPLING 4.0 4.1 RUBBER BUSH INSPECTION Check the condition of the rubber bushes periodically (every 6 months) for wear. If the outside diameter of the bushes is worn down more than 5% compared to the pin bore diameter, then the pin and bush assembles should be changed. With the pins removed an alignment check in accordance with Section 2.0 should be carried out. New pin and bush assemblies shall be fitted back into the coupling as detailed in section 3.0
Open the catalog to page 12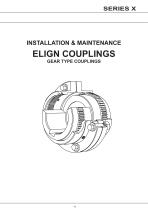
INSTALLATION & MAINTENANCE ELIGN COUPLINGS GEAR TYPE COUPLINGS
Open the catalog to page 13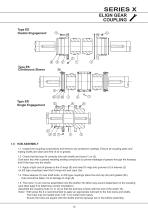
Type ER Single Engagement 1.1 Inspect the coupling components and remove any protective coatings. Ensure all coupling parts and mating shafts are clean and free of oil or grease. 1.2 Check that the keys fit correctly into both shafts and hubs (1) or (3) Coat each key with a grease resisting sealing compound (to prevent leakage of grease through the keyway) and fit the keys into the shafts 1.3 Apply a light coat of grease to the O-rings (8) and insert O-rings into grooves (X) in sleeves (2) on ES type couplings insert the O-rings into end caps (2a) 1.4 Place sleeves (2) over shaft ends, on...
Open the catalog to page 14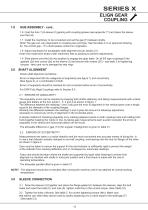
ELIGN GEAR COUPLING 1.0 HUB ASSEMBLY - cont.. 1.6 Coat the hub (1) & sleeve (2) gearing with coupling grease (see appendix ??) and place the sleeve over the hub 1.7 Install the machinery to be connected and set the gap (F) between shafts. Note! The gap can vary dependant on coupling size and type. See the table 3 or an approved drawing for the correct gap, - if in doubt pease contact our engineers. 1.8 Adjust machinery for acceptable shaft alignment as per section 2.0. Note! Use metal shim strips under machinery feet as packing to achieve adjustments. 1.9 Slide sleeve over the hub into...
Open the catalog to page 15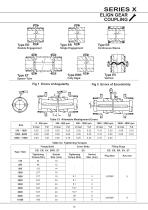
Double Engagement Single Engagement Type ES Continuous Sleeve Fig 1 Errors of AngularityFig 2 Errors of Eccentricity x. Table C1 Allowable Misalignment Errors Table C2 Tightening Torques Type / Size
Open the catalog to page 16All Radicon catalogs and technical brochures
-
Series M Helical In-Line
116 Pages
-
BR-Series-AM.
72 Pages
-
adicon-SeriesX
32 Pages
-
BR Series F
117 Pages
-
Radicon Series X Couplings
32 Pages
-
BR Series X Couplings
36 Pages
-
BR Cone Ring Couplings
16 Pages
-
Series J
73 Pages
-
Motor
4 Pages
-
Series E Flyer
4 Pages
-
G series
4 Pages
-
BD
4 Pages
-
Product Brochure radicon
8 Pages
-
Benzlers Screw Jacks
69 Pages
-
Series J - Shaft Mounted Gearbox
15 Pages
-
Radicon Series ET
42 Pages
-
BR Series G
71 Pages
-
Metric
8 Pages
-
Geared Pump
15 Pages
-
Series P Planetary
4 Pages
-
M series
120 Pages
-
Sala Gears
74 Pages
-
Roloid Pump
17 Pages
-
Heavy Duty Worm Gear Series ER
15 Pages
-
Screw Jacks
58 Pages
-
Series AM Worm Gear
73 Pages
-
Worm Gear Series AJ
89 Pages
-
Series BS Worm Gear
60 Pages
-
Elflex Flexible Couplings
8 Pages
-
Series H industrial gearboxes
123 Pages
-
SERIE G
71 Pages
-
C series
120 Pages
-
Geared Motor Series K
90 Pages
-
F series
119 Pages
-
Elign Gear Couplings
17 Pages
Archived catalogs
-
Worm Gears Series AH
13 Pages