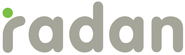
Catalog excerpts
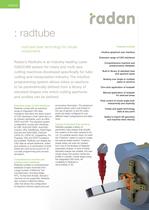
: radtube multi-axis laser technology for tubular components Features include Intuitive graphical user interface Extensive range of CAD interfaces Radan’s Radtube is an industry leading Laser CAD/CAM system for rotary and multi axis cutting machines developed specifically for tube cutting and manipulation industry. The intuitive programming system allows tubes or sections to be parametrically defined from a library of standard shapes into which cutting apertures and profiles can be defined. Extensive range of CAD interfaces Radtube comes with an extensive range of integrated CAD data translators that allow the direct import of CAD drawings in their native form or as industry standards, such as IGES, STEP and DXF. The standard system configuration comes with interfaces for DXF, AutoCAD DWG, AutoCADInventor, VISI, SolidWorks, Solid Edge, IronCad and Solid IGES. Optional CATIA V4, CATIA V5, Unigraphics, Pro Engineer, VDA and STEP translators are available. Radtube can display the CAD data as simple wireframe, solids and surfaces or a combination of both. Solids are used as the source for all cut-path programming and process simulation. Comprehensive machine and postprocessor database Radtube contains a comprehensive database of laser machines from a large number of Machine Tool manufacturers; including Adige, NTC, Trumpf and Amada. Should a machine not be supported, Radtube also contains a Machine Setup utility that allows the configuration of bespoke machine types and post processing information. The advanced postprocessors aren’t just limited to the use of generic G and M codes; posts are easily configured to suit different head configurations and table sizes. Library of standard tube sections Radtube supplies a library of parametric tube shapes that simplify the creation of the tube material to be cut. If a suitable section does not exist, the ‘Freeform’ option is used to create the special shape section. Freeform shape tubes can even be created from one of the libraries of Radtube parametric shapes. If none of these standard shapes are suitable, the user simply draws the section centre line profile or outside / inside shape using the integrated CAD tools. All modelling in Radtube is done entirely in 3D. Comprehensive machine and postprocessor database Built-in library of standard tube and aperture types Nesting over single or multiple pipes or sections One-click application of toolpath Manual application of toolpath for selected areas Total control of nozzle angle both interactively and explicitly Create and apply technology data at any point Ability to import 3D geometry and machine them directly
Open the catalog to page 1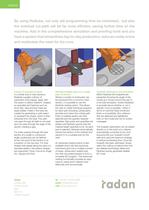
By using Radtube, not only will programming time be minimised, but also the eventual cut-path will be far more efficient, saving further time on the machine. Add in the comprehensive simulation and proofing tools and you have a system that streamlines day-to-day production, reduces costly errors and eradicates the need for dry-runs. Library of standard shapes In a similar way to tube sections, Radtube supplies a library of parametric hole shapes, again with the option to define ‘freeform’ shapes; so specialist joint features such as duck tails, clips and key holes are easily added. Holes in...
Open the catalog to page 2All RADAN catalogs and technical brochures
-
RADAN Radquote
1 Pages
-
RADAN e2i
1 Pages
-
RADAN eQuote
1 Pages
-
RADAN Radview DNC
1 Pages
-
RADAN Radbend for Inventor
2 Pages
-
RADAN Radbend
2 Pages
-
RADAN3D
2 Pages
-
RADAN Radraft
2 Pages
-
RADAN Radm-ax
2 Pages
-
RADAN Radnest
2 Pages
-
RADAN Radprofile
2 Pages
-
RADAN Essential Profile
1 Pages
-
RADAN Radcombi
2 Pages
-
RADAN Essential Combi
2 Pages
-
RADAN Radpunch
2 Pages
-
RADAN Essential Punch
1 Pages
-
RADAN Sheet Metal Solutions
24 Pages
-
RADAN Overview
4 Pages