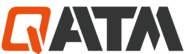
Group: VERDER

Catalog excerpts
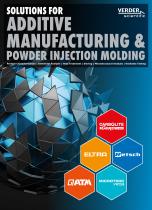
Particle Characterization | Elemental Analysis | Heat Treatment | Sieving | Microstructural Analysis | Hardness Testing
Open the catalog to page 1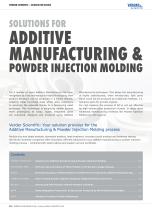
VERDER SCIENTIFIC – SCIENCE FOR SOLIDS ADDITIVE MANUFACTURING & POWDER INJECTION MOLDING For a number of years Additive Manufacturing has been recognized as a key technology for Rapid Prototyping. New product iterations can be produced in a timely fashion, enabling initial functional tests which allow customers to ascertain the potential thanks to a functioning rapid prototype. This technology is advancing rapidly beyond mere prototyping as today, highly integrated parts are conceived, designed and produced using Additive Manufacturing techniques. This allows the manufacturing of highly...
Open the catalog to page 2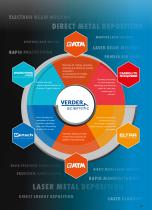
ELECTRON BEAM MELTING DIRECT METAL DEPOSITION SELECTIVE LASER SINTERING SELECTIVE LASER MELTING LASER BEAM MELTING RAPID PROTOTYPING POWDER BED FUSION Machines for cutting, mounting, polishing and etching for surface preparation as prerequisite for reliable microstructural analysis. Furnaces and ovens Dynamic Image Analysis. under air, inert gas, reactive gas or vacuum. Elemental analyzers powders remaining metal powders used for AM processes. Hardness testing of metal components produced by additive manufacturing. SOLID FREEFORM FABRICATION FREEFORM FABRICATION DIRECT METAL LASER SINTERING...
Open the catalog to page 3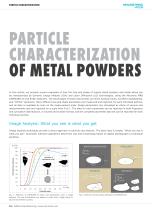
PARTICLE CHARACTERIZATION PARTICLE CHARACTERIZATION OF METAL POWDERS In this article, we present several examples of how the size and shape of typical metal powders and metal alloys can be characterized by Dynamic Image Analysis (DIA) and Laser Diffraction (LD) technologies, using the Microtrac MRB CAMSIZER X2 and SYNC analyzers. The advantages of these instruments are short analysis times, excellent repeatability, and “infinite” resolution. Many different size and shape parameters are measured and reported, for each individual particle, and all data is available as soon as the measurement...
Open the catalog to page 4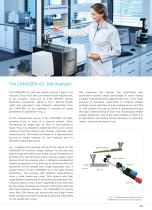
The CAMSIZER X2: DIA Analyzer The CAMSIZER X2, with the widest dynamic range in the industry, 0.8 µm to 8 mm, can measure both suspensions, or dry samples, using one of three different sample dispersion accessories. Below in Fig 1. particle length, width and equivalent area diameter information from the CAMSIZER X2 are reported. A selection of shape parameters is explained in Fig. 2. In the measurement set-up of the CAMSIZER X2 (DIA), particles move in front of a camera system, either transported by single pass air flow or recirculating in liquid. Thus, it is possible to obtain data from up...
Open the catalog to page 5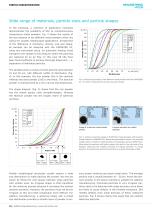
PARTICLE CHARACTERIZATION Wide range of materials, particle sizes and particle shapes The samples show a variety of mean particle sizes between 10 and 50 µm, with different widths of distribution (Fig. 4). In this example, the iron powder (Fe) is the coarsest whereas the steel powder (316) is the finest. The titanium powder is characterized by a very narrow size distribution. In the following, a selection of application examples demonstrates the suitability of DIA to comprehensively characterize metal powders. Fig. 4 shows the results of the size analysis of ten different metal powders...
Open the catalog to page 6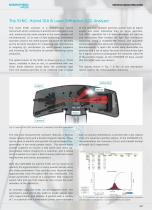
PARTICLE CHARACTERIZATION The SYNC: Hybrid DIA & Laser Diffraction (LD) Analyzer The novel SYNC analyzer is a revolutionary hybrid instrument which combines LD and DIA technologies in one unit, measuring the same sample in the same sample cell simultaneously. LD (a type of light scattering) technology has been used by the metal powder industries for decades as the de facto standard for measuring size distributions in outgoing QC certification by metal powder suppliers and incoming QC verification by powder metallurgy parts producers. The optical bench of the SYNC is shown in Fig. 6. Three...
Open the catalog to page 7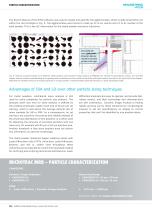
PARTICLE CHARACTERIZATION The Search feature of the SYNC software was used to isolate and quantify the agglomerates, which include all particles not within the red rectangle in Fig. 9. The agglomerates were found to make up 23 % by volume and 12 % by number of the total sample. This is key QC information for the metal powder and parts industries. Fig. 8: Analysis of particle shape of 10 different metal powders with Dynamic Image Analysis (CAMSIZER X2). Beside the quantitative results, the recorded images allow an intuitive understanding of morphology and size differences. More spherical...
Open the catalog to page 8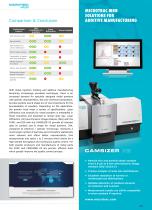
MICROTRAC MRB SOLUTIONS FOR ADDITIVE MANUFACTURING Comparison & Conclusion Performance Feature Laser Diffraction Sieve Analysis Wide dynamic range Reproducibility High resolution for narrow distributions Particle shape analysis Compatibility of results with other techniques Reliable detection of oversize Robust, easy operation Measurement speed, sample throughput Analysis of individual particles With metal injection molding and additive manufacturing becoming increasingly prevalent techniques, there is an increased demand for specially designed metal powders with specific characteristics....
Open the catalog to page 9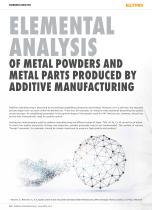
ELEMENTAL ANALYSIS ELEMENTAL ANALYSIS AND OF METAL POWDERS METAL PARTS PRODUCED BY ADDITIVE MANUFACTURING Additive manufacturing is becoming an increasingly established production technology. However, as it is still new, the required process steps have not been uniformly defined yet. There are, for example, no industry-wide standards describing the quality control process. An established parameter is the particle shape of the powder used for AM. Particle size, however, should not be the only characteristic used for quality control. Among the metal powders used for additive manufacturing are...
Open the catalog to page 10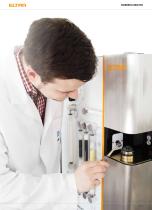
ELEMENTAL ANALYSIS
Open the catalog to page 11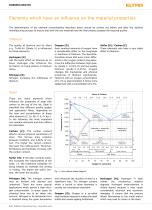
ELEMENTAL ANALYSIS Elements which have an influence on the material properties The determination of the element concentrations described below should be carried out before and after the additive manufacturing process to ensure that both the raw materials and the final product possess the required quality. Titanium The quality of titanium and its alloys e. Ti-6Al-4V (Grade 5) is influenced g. by these elements: Hydrogen [H] Has the same effect on titanium as on steel. Hydrogen may influence the formation of mixed phases in titanium alloys. Nitrogen [N] Nitrogen increases the brittleness of...
Open the catalog to page 12All QATM catalogs and technical brochures
-
QNESS 60 EVO
20 Pages
-
QNESS 200 CS / QNESS 200 CSA+
16 Pages
-
Qeye 800 - Optical Analyzer
8 Pages
-
Qcut - Cutting Accessories
20 Pages
-
Qcut 250 A - Cut-Off Machine
4 Pages
-
Qcut 400 A - Cut-Off Machine
4 Pages
-
Qcut 500 A - Cut-Off Machine
4 Pages
-
Qcut 350 A - Cut-Off Machine
4 Pages
-
Qcut 250 M - Cut-Off Machine
3 Pages
-
Qmount - UV Mounting Device
3 Pages
-
Qpol Accessories
6 Pages
-
Qgrind 100 - Belt Grinder
2 Pages
-
Qmount - UV mounting device
4 Pages
-
Qcut 250 A - Cut-off Machine
4 Pages
-
CONSUMABLES 2022
96 Pages
-
General Catalogue
204 Pages
-
Product Overview
20 Pages
-
Rockwell Hardness Tester
8 Pages
-
Verder Scientific
16 Pages
Archived catalogs
-
Solutions for Materialography
16 Pages
-
Brillant 240
4 Pages