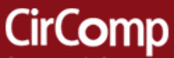

Catalog excerpts
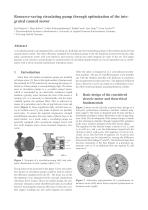
Resource-saving circulating pump through optimization of the integrated canned motor Juri Dolgirev*, Marc Kalter*, Volker Schimmelpfennig*, Ralph Funck, Jens Jung**, Sven Urschel** * Electrotechnical Systems in Mechatronics, University of Applied Sciences Kaiserslautern, Germany * CirComp GmbH, Germany Abstract A circulation pump is an integrated unit, consisting of a hydraulic part for transmitting energy to the medium and a driving canned electric motor. The strict efficiency standards for circulation pumps set by the European Union led to the fact, that today synchronous motor with cost-intensive and resource critical rare earth magnets are state of the art. This paper presents a new resource saving design for canned motors of circulation pumps based on a novel separation can in combination with a ferrite assisted synchronous reluctance motor. More than 140 million circulation pumps are installed in Europe alone [1]. Due to this high number of pumps used, the potential for CO2 reduction by increasing the energy efficiency of these pumps is correspondingly high. The motor used in circulation pumps is a so-called canned motor, which is surrounded by an electrically conductive liquid medium, typically water. Because the rotor of the motor is running wet, it is necessary to hermetically seal the stator winding against the pumped fluid. This is achieved by means of a separation can in the air gap between rotor and stator (Figure 1). Since significant eddy current losses occur in metallic cans [2], cans made of plastic are partially used today. To ensure the required compressive strength and diffusion resistance the cans made of plastic have to be much thicker. As a result, today´s circulating pumps are generally equipped with a permanent magnet motor with rare earth magnets and a motor-mounted frequency converter. while the stator is designed as in a conventional synchronous machine. The use of a SynRM requires a non-metallic can with the thinnest possible wall thickness to minimize the air gap between stator and rotor. The approach followed here is based on a novel can made of a combination of carbon fiber reinforced plastic and polyphenylene sulfide. Basic design of the considered electric motor and theoretical fundamentals Figure 2 shows on the left side a typical basic design of a four-pole synchronous reluctance machine without magnetic support. The stator is designed with 24 slots and has a distributed winding to reduce harmonics in the air gap magnetic field. The development of the internal torque is based on the reluctance principle through targeted flux guidance in the rotor, which is designed in the flux barrier shape. The equation for the internal torque is given in (1). Ld and Lq as well as id and iq are the inductances respectively the currents in the d- and q-axis. The equation (1) can be converted via (2) into the form of equation (3). It can be seen that the torque can be increased by varying the difference between the flux linkage Ψd and Ψq. The internal torque thus becomes maximum if the flux linkage in q-direction approaches zero or if an additional flux acts against Ψq and removes it. Figure 1 Example of a circulation pump (left) and schematic illustration of such a pump (right) [3, 4] The question to be answered in this paper is how rare-earthfree motors in circulation pumps could be used to achieve the efficiency standard set by the EU. The focus was on the development of an integrated ferrite assisted synchronous reluctance drive system. Due to its simple design, the synchronous reluctance motor (SynRM) provides an excellent basis for increasing the resource efficiency: In the rotor, neither copper windings nor rare earth magnets are needed, Figure 2 Schematic representation of a synchronous reluctance motor (left) and a ferrite assisted synchronous reluctance motor (right
Open the catalog to page 1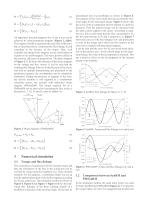
(1) (2) (3) An oppositely directed magnetic flux in the q-axis can be achieved by using permanent magnets (Figure 2, right). The magnets should not generate the main flux in the rotor, but, as described above, counteract the flux linkage Ψq and contribute to the increase of the torque. Here, well available and cheap ferrite magnets can be used instead of expansive rare earth magnets. This has a positive effect on the resource efficiency in pump drives. The phase diagram in Figure 3 [5, 6] shows the influence of the ferrite magnets on the voltage and flux vectors. It can be seen that the...
Open the catalog to page 2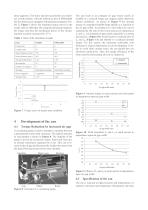
three segments. The stator and rotor geometries are identical in both models, with the difference that in PMSynRM the flux barriers are equipped with permanent magnets (Table 1). Figure 7 shows the simulated torque curves in the steady state at 3200 rpm. By using the permanent magnets, the torque and thus the mechanical power of the electric machine could be increased by 33 %. Table 1 Data of the simulation models Data The can leads to an enlarged air gap which results in SynRM in a reduced torque per ampere under otherwise similar conditions. As shown in Figure 9 the internal torque of a...
Open the catalog to page 3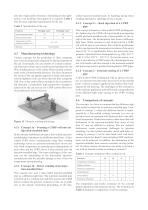
also have high media resistance. Depending on the application, even drinking water approval is required. Table 2 lists the most important requirements for the can. Table 2 Specification of the can Features Heating water Drinking water Temperature of the pumping medium (°C) Material Manufacturing technology Various concepts for the production of fibre composite cans were developed and compared for the development of the can. In principle, the can consists of a media-conducting inner layer (liner) and a reinforcement produced by the fibre winding process with carbon fibres running...
Open the catalog to page 4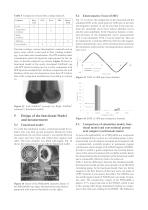
Epoxy resin Temperature resistance Media resistance Parylene coatings, various thermoplastic materials and an epoxy resin, which is also used in fibre winding technology, were taken into consideration. The PPS material under consideration meets all important requirements for the can liner, so that this material was chosen. Figure 13 shows a functional model of the newly developed FilaWin® can with PPS internal coating next to a series component with PPS injection-moulded liner. In direct comparison, the wall thickness of the new development is more than 50 % below that of the component...
Open the catalog to page 5