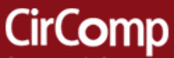

Catalog excerpts
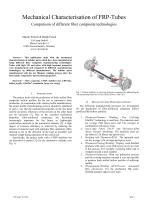
Mechanical Characterisation of FRP-Tubes Comparison of different fiber composite technologies Martin Welsch & Ralph Funck CirComp GmbH Marie-Curie-Str.11 67661 Kaiserslautern, Germany www.circomp.de Abstract— This publication deals with the mechanical characterization of tubular parts which have been manufactured using different fibre composite manufacturing technologies. Tubes with high UD and tubes with high torsional properties were manufactured and compared in different manufacturing technologies by different manufacturers. The tubular parts manufactured with the wet filament winding process show the best tensile, compressive and torsional properties. Keywords— Fibre composite, CFRP, stabiliser bar, FRP-tube, hollow profile, FilaWin®, ondulation, heavy tow roving The project dealt with the production of thick-walled fibre composite hollow profiles for the use in automotive mass production. In cooperation with various profile manufacturers, the actual profile manufacturing process should be optimized in such a way that the mechanical properties on the one hand and the economic efficiency of the process on the other hand can be increased [1]. Due to the excellent mechanical properties fibre-reinforced composites are becoming increasingly important for the future as lightweight construction materials in the automotive industry [2]. A high degree of resource efficiency is achieved by reducing the amount of material used with optimum fibre utilisation (fibre directed as far in the direction of the load as possible) and reduced weight during operation of the vehicle [2]. Specifically, the project deals with a CFRP stabiliser bar (as described in patent [3]) for the automotive industry (see Fig. 1). Fig. 1: Chassis stabiliser as a driving dynamics component for influencing the roll and steering behaviour of the vehicle (Source: Audi AG) MANUFACTURING PROCESSES APPLIED The following manufacturing processes are investigated for the production of fibre-reinforced composite hollow profiles (FRP hollow profiles): Thermoset-Filament Winding: The CirComp FilaWin® technology is used here. The materials used are rovings (50k heavy-tows and 12k rovings) in combination with epoxy resin. Non-Crimp Fabric (NCF) with Thermoset-RTM (Resin Transfer Moulding): The materials used are dry fabrics (12k fibres) and epoxy resin. Braiding with Thermoset-RTM: The materials used are dry rovings (12k rovings) and epoxy resin. Thermoset-Prepreg-Winding: Prepreg semi-finished products with epoxy resin (50k heavy-tows) are used in this process. For example, a prepreg fabric mat is wrapped around a steel mandrel. Thermoset-Pultrusion: With the pultrusion process and the existing machine concept it was not possible to produce thick-walled hollow profiles of sufficient quality. Thermoplastic-Winding (AFP-Process; Automated fibre placement): For the production 50k semifinished products (tapes) were used.
Open the catalog to page 1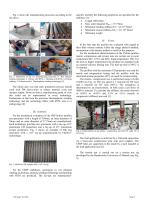
Fig. 2 shows the manufacturing processes according to the list above. specific whereby the following properties are specified for the stabiliser [1]: Length 1003,5mm Max. outer diameter Dmax = 37,75mm Minimum bending stiffness EI > 3,6∙109 Nmm² Minimum torsion stiffness GIT > 3,8 ∙109 Nmm² Minimum weight IV. Fig. 2: Illustration of the six manufacturing processes (1. Wet filament winding technology, 2. Fabrics with RTM, 3. Braiding with RTM, 4. Prepreg winding, 5. Pultrusion and 6. Thermoplastic winding technology) [4] The initial idea was that each production process should work...
Open the catalog to page 2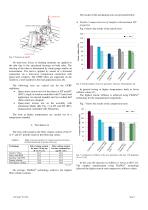
The results of the mechanical tests are presented below: Cylinder force A. Tensile-/ compression test of samples with maximum UD properties Fig. 6 shows the results of the tensile tests. Spherical roller bearing Retention force No transverse forces or bending moments are applied to the tube due to the articulated bearings on both sides. The twisting of the tubes is determined by strain gauges and/or an extensometer. The load is applied by means of a frictional connection via a transverse compression connection with glued steel couplers. The CFRP tubes are supported on the inside by a steel...
Open the catalog to page 3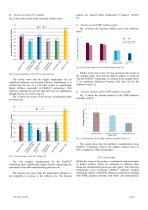
B. Torsion test of the 45° samples Fig. 8 shows the results of the torsional stiffness tests. torques are reduced under temperature by approx. 10-20% [1]. Torsional stiffness GIT 109 [Nmm²] Torsional stiffness GIT 109 [Nmm²] C. Torsion test of CFRP stabiliser tubes Fig. 10 shows the torsional stiffness test of the stabiliser tubes. max. measured value min. measured value Prepreg winding with fabric (50k) Fig. 10: Torsional stiffness of the CFRP stabiliser tubes [4] Fig. 8: Torsional stiffness of the ±45° test specimens [4] Fracture torque MT,max [kNm] The results show that the higher...
Open the catalog to page 4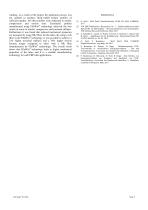
winding. As a result of the project the pultrusion process was not suitabel to produce thick-walled hollow profiles of sufficient quality. All other profiles were subjected to tensile, compression and torsion tests. Essentially profiles manufactured using FilaWin® technology achieved the best results in terms of tensile, compressive and torsional stiffness. Furthermore it was found that reduced mechanical properties are measured by using 50k fibres for the tubes. By using a 12k fibre in the FilaWin® technology it was possible to achieve a 23% higher torsional stiffness and a 50% higher...
Open the catalog to page 5