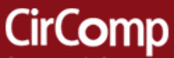

Catalog excerpts
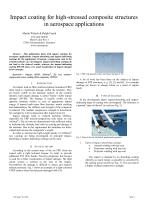
Impact coating for high-stressed composite structures in aerospace applications Martin Welsch & Ralph Funck CirComp GmbH Marie-Curie-Str.11 67661 Kaiserslautern, Germany www.circomp.de Abstract— This publication deals with impact coatings for aerospace applications. Impact-absorbing and impact-indicating coatings for the application of tension-/ compression rods in the aviation industry are investigated. Impact-absorbing coatings do not lead to the desired results, whereas the impact-indicating coating DW330 shows very good visualization of impact damage at low energies. Keywords— Impact, BVID, AirStrut®, Tie rod, tension-/ compression strut, coating, fibre composite, DW330 An impact load on fibre reinforced plastic laminates (FRP) often leads to significant damage within the laminate. They are barely visible on the laminate surface. In the aviation industry such impact damage is called "barely visible impact damage" (BVID). The damage is usually visible on the opposite laminate surface in case of appropriate impact energy. If impact loads cause fibre fractures, matrix cracking and delamination, the stiffness and strength of the composite is reduced. The residual compressive strength is determined, for example by CAI (compression after impact) tests [1]. Impact damage leads to reduced buckling stiffness, especially for FRP tension/compression rods (strut, tie rod, AirStrut®). The tie-rods are dimensioned with sufficient safety to withstand the ultimate load with an existing pre-damage of the laminate. Due to this requirement the laminates are thickwalled and increase the component’s weight. In order to increase the light-weight quality of AirStruts® new coatings are being investigated. In principle impactabsorbing or impact-indicating coatings can be used. Fig. 1: FRP with painted surface and impact damage (8.5J) A lot of work has been done on the subject of impact damage on FRP structures, e. g. [2], [3] and [4]. For example coatings are known to change colour as a result of impact loads. III. TYPES OF COATINGS In the development phase impact-absorbing and impactindicating types of coating were investigated. The reference is a painted "state-of-the-art" tie rod (see Fig. 2). Fig. 2: State-of-the-art AirStruts® painted and unpainted 1. II. STATE OF THE ART According to the current state of the art FRP struts are coated with a light textured lacquer. In order to provide additional FST (Fire Smoke Toxicity) properties, this lacquer is used for a better visualization of impact damage. The light colour creates a contrast in the area of the impact. Nevertheless the damage is difficult to detect and requires trained personnel. Fig. 1 shows an example of a light-coloured CFRP surface which has been pre-damaged with 8.5J. Types of impact-absorbing coatings: a. Aramid winding with top coat b. Elastomer coating with top coat c. Polyester winding with top coat The impact is damped by an absorbing coating whereby as much energy as possible is converted by the coating (cross-section see Fig. 3). This can lead to a higher residual compressive strength.
Open the catalog to page 1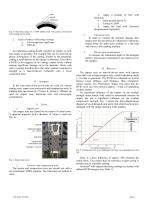
a. Apply a preload of 1kN with 8mm/min b. Hold the preload for 3s c. Unload to 200N d. Apply the load with 2mm/min (displacement controlled) Fig. 3: Schematic image of a CFRP tubular body with partial cross-section with coating and top paint Types of impact-indicating coatings : a. Two-component rigid foam b. DW330 An indicating-coating should visualize an impact as early and clearly as possible. For example this can be achieved by plastic deformation of the coating. Similar to the absorbingcoating a small portion of the energy is absorbed. This allows a BVID to be triggered at low energy...
Open the catalog to page 2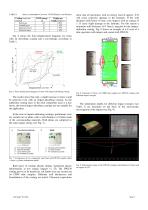
IMPACT ABSORBING-COATING - BVID ENERGY AND WEIGHT Coating (top layer, painted) Reference Aramid layer Elastomer layer Polyester layer Weight per length (relative) 100% + 12% + 19% + 19% show that all specimens with an energy load of approx. 8.5J will cause extensive damage to the laminate. If the wall thickness falls below 0.7mm, even impacts with an energy of ≤ 1J cause slight damage to the laminate. For this reason a minimum wall thickness of 0.7mm is targeted for the impactindication coating. Fig. 8 shows an example of a C-scan of a tube specimen with impact and coated with DW330. Fig. 6...
Open the catalog to page 3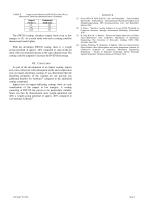
INDENTATION DEPTHS OF DW330-COATING (WALL THICKNESS 0,7MM) FOR DIFFEREND IMPACT ENERGIES The DW330 coating visualizes impact loads even at low energies (< 1J). As a result struts with such a coating could be dimensioned much lighter. With the developed DW330 coating, there is a weight saving potential of approx. 40% compared to state-of-the-art struts with conventional topcoat at the same ultimate load. The coating could be adapted to increase the BVID limit energy. Norm DIN EN 6038:2016-02: Luft- und Raumfahrt – Faserverstärkte Kunststoffe – Prüfverfahren – Bestimmung der...
Open the catalog to page 4