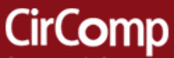

Catalog excerpts
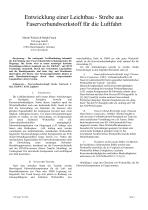
Entwicklung einer Leichtbau - Strebe aus Faserverbundwerkstoff für die Luftfahrt Martin Welsch & Ralph Funck CirComp GmbH Marie-Curie-Str.11 67661 Kaiserslautern, Germany www.circomp.de Kurzfassung— Die vorliegende Veröffentlichung behandelt die Entwicklung einer Faserverbund-Fahrwerkskomponente für Flugzeuge. Die Strebe wird in einem neuartigen hybriden Herstellungsverfahren bestehend aus der FilaWin®- und RTM Technologie, hergestellt. Durch den verwendeten Lagenaufbau und die Bauteilgeometrie sind hohe Zug- und Drucklasten übertragbar. Die Druck- und Torsionseigenschaften können je nach Bauteilanforderungen durch einen entsprechenden Lagenaufbau variiert werden. Schlagworte— Faserverbundwerkstoff, Strebe, Fahrwerk, IRod, FilaWin®, RTM, Luftfahrt Die Luftfahrtindustrie stellt immer höhere Anforderungen an Steifigkeit, Festigkeit, Gewicht und Korrosionsbeständigkeit. Neben diesen Aspekten spielt die Wirtschaftlichkeit auch eine bedeutende Rolle. Somit ist das Ziel die Entwicklung von Bauteilen mit besseren oder gleichen Eigenschaften bei niedrigerem Gewicht und, wenn möglich, niedrigeren Kosten. Um diesen Herausforderungen gerecht zu werden, ist eine Entwicklung von Komponenten aus neuen leichteren Werkstoffen wie z.B. Faserverbundwerkstoffen unumgänglich. Fahrwerkskomponenten von Flugzeugen (z.B. linkage oder brace) oder Helikoptern (z.B. trailing arm) werden vornehmlich aus herkömmlichen, metallischen Werkstoffen hergestellt. Neuentwicklungen solcher Komponenten aus FVK (Faserverbundkunststoffen) liegen bereits vor. Neben den mechanischen Eigenschaften der Fahrwerkskomponenten steht die Entwicklung eines neuartigen HybridenHerstellungsprozesses, bestehend aus der Faserwickeltechnik und des RTM-Prozesseses (Resin Transfer Moulding), im Vordergrund. Die entwickelte Komponente wird nachfolgend als I-Rod bezeichnet. II. STAND DER TECHNIK Nach dem aktuellen Stand der Technik werden überwiegend Fahrwerkskomponenten für die Luft- und Raumfahrtindustrie aus Titan oder 300M Legierung o.ä. hergestellt. Der Trend bewegt sich jedoch in Richtung von leistungsfähigeren und leichteren Werkstoffen. Aus wirtschaftlicher Sicht ist 300M ein sehr guter Werkstoff, jedoch ist die Korrosionsbeständigkeit nicht optimal für die Anwendung [1]. Um den Anforderungen gerecht zu werden, finden Entwicklungen in den folgenden Bereichen statt [2]: A. Kunststoffverbundwerkfstoffe (engl. Polymer Matrix Composites, PMC): Verbundwerkstoffe (z.B. Faservervundwerkstoffe) bieten gegenüber herkömmlichen Werkstoffen die Vorteile – Gewicht, Dauerschwingfestigkeit und Korrosionsbeständigkeit (unter Verwendung der korrekten Werkstoffpaarung). I.d.R. werden Komponenten für Fahrwerke mittels einer Faser-Preform und dem Post-Prozess RTM hergestellt. In [3], [4] [5] und [6] werden mehrere Faserverbund Prototypen dargelegt. Darunter beispielsweise ein „drag brace“ für den F16 Kampfjet oder ein „trailing arm“ für den NH-90 Helicopter. B. Titan-Verbund-Werkstoffe (engl. Titanium Metal Matrix Composites, TiMMC): Hierbei handelt es sich um einen Verbundwerkstoff bestehend aus Titan mit einer zusätzlichen Verstärkung wie z.B. Fasern. Dabei kann beispielsweise eine SiC (Siliciumcarbid) Faser eingesetzt werden. Diese Werkstoffkombination ist besonders für Anwendungen geeignet, bei denen eine extrem hohe Steifigkeit gefordert wird [5]. Ein wesentlicher Nachteil dieses Werkstoffes sind die hohen Herstellungskosten. C. Hochfeste nichtrostende Stähle: Im Bereich der hochfesten, nichtrostenden Stähle werden neue Werkstoffe entwickelt, die im Vergleich zu bekannten Werkstoffen höhere Festigkeiten, excelente Korrosionsbeständigkeiten und höhere Bruchzähigkeiten aufweisen (z.B. X1CrNiMoAlTi12-11-2) [2]. Abbildung 1 zeigt eine Übersicht von Werkstoffen, die für
Open the catalog to page 1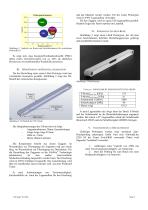
und das Material variiert werden. Für die ersten Prototypen wird ein 0/90° Lagenaufbau verwendet. Für den Zuggurt wird ein quasi UD-Lagenaufbau gewählt. Dadurch liegen die Fasern optimal im Lastpfad. IV. EIGENSCHAFTEN DES I-RODS Abbildung 3 zeigt einen I-Rod Prototypen, der mit dem zuvor beschriebenen hybriden Herstellungsprozess gefertigt und anschließend lackiert wurde. Abbildung 1: Vergleich von Kosten und Gewichtsersparnis für verschiedene Werkstoffe [5] Es zeigt sich, dass Kunststoffverbundwerkstoffe (PMC) neben einem Gewichtsvorteile von ca. 40% ein ähnliches Preisniveau wie...
Open the catalog to page 2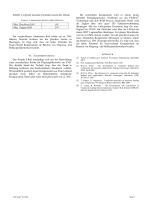
Tabelle 2 zeigt die maximal erreichten Lasten des I-Rods. TABELLE 2: ERGEBNISSE DER ZUG-/ DRUCKPRÜFUNG Ein vergleichbarer Aluminium Rod würde ein ca. 50% höheres Gewicht besitzen um die gleichen Lasten zu übertragen. Es zeigt sich, dass ein hohes Potential für Faserverbund Komponenten im Bereich von Flugzeug- und Helikopterfahrwerken besteht. Die entwickelte Komponente wird in einem neuen hybriden Fertigungsprozess, bestehend aus der FilaWin® Technologie und dem RTM Prozess, hergestellt. Dabei wird die Zuglast über eine quasi UD Schlaufenverbindung übertragen. Mit der vorliegenden Geometrie...
Open the catalog to page 3