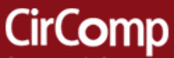

Catalog excerpts
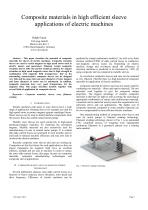
Composite materials in high efficient sleeve applications of electric machines Ralph Funck CirComp GmbH Marie-Curie-Str.11 67661 Kaiserslautern, Germany www.circomp.de Abstract— This paper describes the potential of composite materials for sleeves of electric machines. Composite retention sleeves are used to retain magnets on high speed rotors used in electric motors and generators. Filament wound composite retention sleeves offer the perfect technical solution for magnet retention on high speed magnetic rotors due to high strength in combination with magnetic field transparency. Due to the outstanding characteristics composite sleeves can be designed very thin and the space between outer diameter of rotor magnets and inner diameter of stator can be minimized. In addition, composite materials have very good transparency for the magnetic field. This paper describes benefits together with several fields of application for composite sleeves. Keywords— Composite materials, sleeves, cans, filamentwinding I. INTRODUCTION Electric machines with stator or rotor sleeves have a wide range of application. Rotating sleeves for example are used for high speed rotors to protect magnets against centrifugal forces. Stator sleeves can be used to shield machine components from the process fluid, also called canned motor pumps. Metallic rotor sleeves are used extensively in high-speed permanent-magnet machines for fastening the permanent magnets. Metallic materials are also extensively used for manufacturing of cans in canned motor pumps. It is evident that eddy-current losses are generated in such metallic sleeves and leads to reduced machine efficiency and may also lead to overheat the electric machines. predicted by simple mathematic models [1] as well as by finite element method (FEM) of eddy current losses in conductive non-magnetic sleeves (cans) [2]. Depending on electric machine design and revolution speed the efficiency of electrical machines is predicted to be increased by >30% [3] using composite sleeves compared to metallic sleeves. As conclusion composite sleeves and cans can be assumed as very efficient. Therefor there is a high potential of composite materials for application of electric machines. Composite material for sleeves and cans are manly made by combining two materials – fibres and matrix materials. The two materials work together to give the composite unique properties. The biggest advantage of modern composite materials is that they are light as well as strong. By choosing an appropriate combination of matrix and reinforcement material, a material can be made that exactly meets the requirements of a particular sleeve and can applications. The higher cost of composite materials compared to some metallic materials can be over compensated by more efficient electric machines. One manufacturing method of composite rotor sleeves and cans for motor pumps is filament winding technology. Filament winding technology shown in Fig. 1 is an automated CNC controlled process of wrapping resin impregnated continuous filaments in a geometric pattern over a rotating male mandrel. Recently composite rotor sleeves and cans are coming up. Composites are the first choice for such applications as they are almost transparent for magnetic field, have an excellent stiffness, strength and are easy to machine. In order to reduce the rotor eddy-current losses, this paper focuses on composite materials, composite manufacturing technologies and composite sleeve applications. II. COMPOSITE SLEEVE AND CAN MANUFACTURING Fig. 1: Filament winding technology. Several publication analyses rotor eddy-current losses as a function of sleeve material, sleeve thickness, rotor speed and drive frequency. Efficiency of electric machines can be
Open the catalog to page 1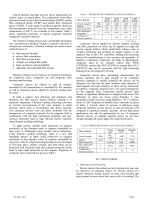
Typical filament materials used for sleeve applications are carbon-, glass- or aramid-fibres. The combination of the fibres and matrix leads to glass fibre reinforced platic (GFRP), carbon fibre reinforced plastic (CFRP) and aramid fibre reinforced plastic (AFRP). A wide range of certified composite thermoset and thermoplastic materials from low temperatures up to high temperatures of 400 °C are available on the market. Table 1 shows significant properties of typical composite materials compared to metallic materials. The filament winding process has considerable advantages over...
Open the catalog to page 2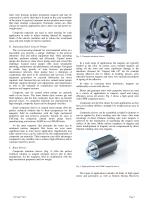
outer rotor housing includes permanent magnets and may be connected to a drive shaft that is located on the axial centerline of the motor. In general, outrunner motors produce more torque than their inrunner counterparts. Outrunner motors are often chosen for specific applications due to their size and power-toweight ratios. Composite materials are used as rotor housing for such application in order to reduce heating induced by magnetic fields of the electric machines and to reduce the accelerated mass and total weight of electric machines. B. Separating Stator Cans for Pumps The...
Open the catalog to page 3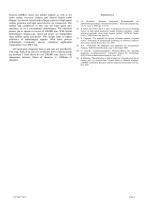
Systems (KERS), micro gas turbine engines as well as for turbo energy recovery systems and electric hybrid turbo charger. An electric hybrid turbo charger consists of high speed turbine generator and high speed electric air compressor. The turbine and compressor in this case are high speed aero machines, as in a conventional turbocharger. The electrical motors run at speeds in excess of 100,000 rpm. With hybrid turbocharger compressors, speed and power are independent from turbine speed and power. This design leads to higher efficiency of turbocharged engines. With latest process...
Open the catalog to page 4