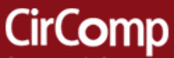

Catalog excerpts
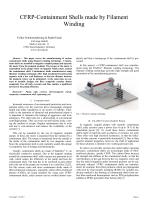
CFRP-Containment Shells made by Filament Winding Volker Schimmelpfennig & Ralph Funck CirComp GmbH Marie-Curie-Str. 11 67661 Kaiserslautern, Germany www.circomp.de Abstract— This paper covers the manufacturing of carbon containment shells using filament winding technology. Containment shells are installed in magnetic coupled pumps and separate the motor from the pumped medium. The torque of the motor is transmitted to the pump wheel via magnets which rotate around the containment shell. Containment shells manufactured using filament winding technology offer high mechanical load-bearing capacity with a low wall thickness, so that the distance between the magnetic rotors can be minimized. At the same time, in contrast to metallic designs, the fibre composite remains almost completely free off eddy currents and thus enables a significant increase in the pump efficiency. pletely and thus a heating-up of the containment shell is prevented. In this project, a CFRP-containment shell was manufactured using the FilaWin® filament winding technology. The filament winding technology provides high strength and good automation of the manufacturing process. Keywords— Pump, eddy current, electromagnetic clutch, composite, containment shell, separating can I. INTRODUCTION Increased awareness of environmental protection and occupational safety over the years has led to increasingly stringent health and safety regulations in all sectors of industry. Especially in the operation of chemical and petrochemical plants it is important to minimize the leakage of aggressive and toxic substances. The shaft seals are a shortcoming of conventional centrifugal pumps. They can wear out and become leaky, causing the medium to escape. Regular maintenance due to wear and tear is cost-intensive and reduces the availability of the system [1]. This can be remedied by the use of magnetic coupled pumps. In these, the motor is separated from the medium by a containment shell. The torque is transferred from the outside to the inside of the containment shell by two magnetic rotors. Since the containment shell is only statically sealed, this design is completely free of leakage and maintenance. Usually, containment shells are made of Hastelloy® C, an electrically conductive material. Due to the magnets rotating around the containment shell, eddy currents are generated in its wall, which reduce the efficiency of the pump and heat the containment shell. The heat has to be extracted at great effort and a dry run of the pump can overheat it to a total loss [2] [3]. For this reason, more and more containment shells made of fibre-reinforced composites, especially carbon fibre-reinforced plastics (CFRP), are being installed. By using such CFRPcontainment shells, eddy currents can be avoided almost com- Fig. 1: Filament winding technology. II. FILAWIN®-CONTAINMENT SHELL In magnetic coupled pumps with metallic containment shells, eddy currents cause a power loss of up to 10 % of the transmitted power [2]. To avoid these losses, containment shells made of materials such as plastics or ceramics are used. These offer very high electrical resistances, so that the induction of eddy currents is practically eliminated [2]. Due to their specific material properties, however, the field of application for these solutions is limited to low working pressures [4]. In order to avoid eddy currents also under higher operating pressures, containment shells are increasingly made of fibrereinforced plastics, usually CFRP. The carbon fibres increase the strength and stiffness of the containment shells, so that the wall thickness in the gap between the two magnetic rotors and also the radial elongation under increased pressure can be significantly reduced. CFRP- containment shells are manufactured, for example, from fibre preforms which are impregnated with resin by resin transfer moulding (RTM) [5]. Another production method is the forming of containment shells from carbon fibre-reinforced thermoplastic such as PPS (polyphenylene sulfide) or PEEK (polyether ether ketone) [6] [7].
Open the catalog to page 1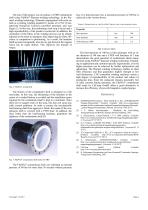
The aim of this project was to produce a CFRP containment shell using FilaWin® filament winding technology. In the filament winding technology, filaments impregnated with resin are laid on a rotating winding mandrel by means of a CNC (Computerized Numerical Control) controlled automatic unit (see Figure 1). In this way, the preforming work step is saved and a high reproducibility of the product is achieved. In addition, the orientation of the fibres in the winding process can be ideally adjusted to the loads in operation, thus improving the fibre efficiency in comparison to preforming. As a...
Open the catalog to page 2