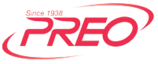

Catalog excerpts
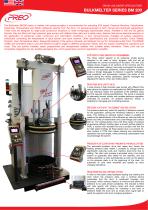
DRUM UNLOADER APPLICATORS The Bulkmeter BM200 series of melters with pressure plates is recommended for extruding EVA based, Pressure Sensitive, Polyethylene, Polyamide, Polyurethane and Mastic adhesives directly from the drum, for general purposes in both manual and automatic applications. These units are designed for large-scale production situations to meet increasingly sophisticated needs. Available in 200 litre (55 gallon) formats, they are fitted with high precision gear pumps with different flow rates and a safety valve, features that ensure absolute precision in the application of adhesives under continuous and intermittent conditions. A new microprocessor manages all system operations, individually controlling the temperature of each section and each channel. Other specifications are: Economy function, Clock, Weekly Program, Over-Temperature Alarm, Sequential Heating of the various channels, and Delayed Cut-out for Temperature Set Point. The BM200 melters are innovative: easy to use and flexible enough to adapt to different production needs, with low impact maintenance operations and costs. They are quickly installed, easily programmed and exceptionally reliable, with suitable safety standards. These units can be completely integrated into any existing packaging line, which guarantees maximum application versatility. LCD DISPLAY AND INNOVATIVE PROGRAMMING The rotary switch selector is an extremely simple device designed to be used to enter, program, edit and set all parameters for correct functioning of the plant. The new LCD Display shows images of all sections of the machine and the relative parameters, making it very easy to program the system, even for non-specialist personnel, without problems involving codes or foreign languages to interpret. A specific notification area constantly and dynamically monitors the status of the system during the various operations. Specific messages are displayed for alarms, errors and malfunctions. GEAR PUMP WITH SAFETY VALVE A wide choice of high precision gear pumps with different flow rates allows the operator to personalise the BM200 applicators to suit individual needs, the properties of the adhesive used, and the required melting specifications. The pump is powered by alternating current motors with variable electronic regulation controlled by inverters. An optional electronic sensor is available for managing and controlling pressure. PRESSURE PLATE WITH “ON DEMAND” MELTING SYSTEM The pressure plate only melts the quantity of adhesive required for the application, leaving the remaining material in the solid state. This melting on demand system makes it possible to preserve the specifications of the adhesive by reducing thermal stress and risks of deterioration and cross-linkage due contact with air. The melting plates come with three types of surfaces to guarantee different melting rates: a smooth surface (ideal for PUR), a surface with standard fins and a surface with fine fins for high speed melting. All these plates have a no-scratch nostick surface in PTFE that makes cleaning and maintenance operations fast and simple, while preventing carbonisation that would damage the system. PRESSURE PLATE ELEVATOR WITH PNEUMATIC-HYDRAULIC SYSTEM The pneumatic-hydraulic drive that raises and lowers the heating pressure plate makes it possible to change drums, significantly reducing costs and machine down-time due to refilling. The start cycle process is activated using a two-hand system to guarantee total safety for the operator, and the refilling operation is done automatically as soon as the gasket on the pressure plate is at the beginning of the drum. An automatic air vent valve simplifies and speeds up drum changing operations. DRUM INSERTING AND CENTRING SYSTEM A roller on the plant’s base facilitates loading and inserting the drum below the pressure plate, and a centring device guarantees that the drum is positioned precisely and accurately, which reduces waste to a minimum and allows the adhesive to be used almost completely. The extruder is fitted with side guards with closing hooks and drum detection sensors, adjustable contacts for indicating a low level of adhesive inside the drum and an empty drum signal light to assist the operator with drum changing operatio
Open the catalog to page 1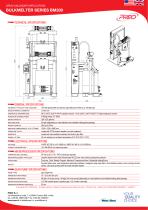
DRUM UNLOADER APPLICATORS BULKMELTER SERIES BM200 TECHNICAL SPECIFICATIONS GENERAL SPECIFICATIONS ADHESIVE TYPOLOGY AND VISCOSITY Hot-melt polyamides and reactive polyurethanes (PUR) up to 100,000 Cps DRUM INTERNAL DIAMETER 570 mm 50°C÷210°C (120°F÷410°F) standard version - 50°C÷230°C (120°F÷450°F) HT high temperature version 3 (fitting thread 1/2” GAS) 200 lt (55 gallons) 40 kg/h (depending on used adhesive and installed melting plate typology) 950 kg (2100 lb) 1200 x 1200 x 2600 mm coated with PTFE scratch-resistant non-stick treatment, coated with hard oxidation treatment and built-in...
Open the catalog to page 2All PREO catalogs and technical brochures
-
Easy Touch W20
2 Pages
-
Easy Touch W1
2 Pages
-
Cold Line
2 Pages
-
Bulkmelter BM20
2 Pages
-
General catalogue
8 Pages
-
HAND GUNS SERIES WEST & BEST
2 Pages
-
HOT-MELT SLOT GUNS SERIES CH
2 Pages
-
EASY SERIES U8
2 Pages
-
EASY SERIES U5
2 Pages
-
EASY SERIES W10
2 Pages
-
EASY SERIES W5
2 Pages
-
EASY SERIES P20
2 Pages
-
EASY SERIES P15
2 Pages
-
EASY SERIES P10
2 Pages
-
Applicators EASY Series P5
2 Pages