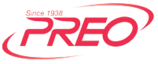

Catalog excerpts

DRUM UNLOADER APPLICATORS The Bulkmelter 20 Series melt on demand drum unloaders are intended for direct extrusion from drums of EVA based, Pressure Sensitive, Polyethylene, Polyamide, and Polyurethane adhesives and Mastics in general, for both manual and automatic applications. Designed for large-scale production, in order to meet the ever more sophisticated needs, they come in a 20 litre (5 gallon) configuration and are fitted with high pressure gear pumps with different flow rates and a safety valve, in order to guarantee absolute feed precision under all usage conditions, both continuous and intermittent. A new microprocessor controls all the operations necessary for the system to operate: thermo-regulation of the various sections, programming control of 8 glue lines for each of the 4 independent channels. Additional features include: Economy Function, Clock, Weekly Program, Maximum Absolute Temperature Alarm, sequential Heating for the various channels, and Temperature Set point Cut-out Delay. BM20 melters are innovative in terms of simplicity of use, production flexibility, maintenance operations and costs, quick installation, easy programming, safety standards, reliability, and complete integration with any existing packaging line, and guarantee maximum application versatility. LCD DISPLAY AND INNOVATIVE PROGRAMMING All the parameters involved in the correct functioning of the system are extremely simple to enter, program, edit, and set using the “Rotary Switch” selector. The new LCD Display depicts all sections of the machine and the related parameters graphically, making it extremely simple to programme the system, even for non-specialist personnel, without any problems with codes or foreign languages to be interpreted. A message area constantly and dynamically monitors the status of the system during the various operations. If any alarms or anomalies occur, appropriate error messages are displayed. ELEVATOR WITH PNEUMATIC CYLINDERS An elevator with two pneumatic cylinders for raising and lowering the heating pressure plate is used for changing the drum, which significantly reduces machine costs and down times due to refilling. The start cycle process is controlled by a two-hand activation system to ensure that the operator is totally safe and the refilling operation is then completed automatically once the flat pressure gasket is at the beginning of the drum. An automatic air discharge function simplifies drum changing operations. HIGH PRECISION GEAR PUMP The extruders are fitted with high precision gear pumps. Within the same size, pumps are available with flow rates that differ, depending on the adhesive used and the melt required. The pump is driven by alternating current motors, with variable electronic regulation and controlled by an inverter. REGULATION VALVE AND QUICK PRESSURE RELEASE This keeps the set pressure constant and guarantees maximum safety when the system is in use, by discharging the pressure in the adhesive in the system automatically and safely, even in an emergency. PRESSURE CONTROL DEVICE A sophisticated control system uses the melter’s display to show the pressure of the adhesive at the manifold outlet. This display is similar to that for a traditional digital pressure gauge and shows the adhesive pressure in bars. PRESSURE PLATE WITH “ON DEMAND” MELTING SYSTEM A pressure plate only melts the quantity of adhesive required for the application, leaving the remaining material in a solid state. This on demand melting system makes it possible to protect and preserve the adhesive, reducing the risks of deterioration and cross-linkage, due to the product coming into contact with the air. DRUM CENTRING SYSTEM AND LEVEL SENSORS A centring system guarantees precise, accurate positioning of the drum, reducing waste to a minimum and allowing almost all the adhesive it contains to be used. The extruder is also fitted with a drum detection sensor, a level sensor that indicates when the drum is finished, and an optional second sensor that can be adjusted to indicate when the drum is runni
Open the catalog to page 1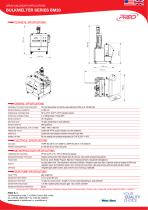
DRUM UNLOADER APPLICATORS TECHNICAL SPECIFICATIONS GENERAL SPECIFICATIONS ADHESIVE TYPOLOGY AND VISCOSITY Hot-melt polyamides and reactive polyurethanes (PUR) up to 100,000 Cps DRUM INTERNAL DIAMETER 0 280 mm OPERATING TEMPERATURE 50°Ct210°C (120°Ft410°F) standard version HOSE/GUN CONNECTIONS 2, 4 (fitting thread 1/2"x20 UNF) DRUM CAPACITY MELTING RATE 16 kg/hr (depending on used adhesive) WEIGHT (EMPTY) PRESSURE PLATE coated with PTFE scratch-resistant non-stick treatment, coated with hard oxidation treatment and built-in glue filter WARM-UP TIME 20 min starting from ambient...
Open the catalog to page 2All PREO catalogs and technical brochures
-
Easy Touch W20
2 Pages
-
Easy Touch W1
2 Pages
-
Cold Line
2 Pages
-
Bulkmelter BM200
2 Pages
-
General catalogue
8 Pages
-
HAND GUNS SERIES WEST & BEST
2 Pages
-
HOT-MELT SLOT GUNS SERIES CH
2 Pages
-
EASY SERIES U8
2 Pages
-
EASY SERIES U5
2 Pages
-
EASY SERIES W10
2 Pages
-
EASY SERIES W5
2 Pages
-
EASY SERIES P20
2 Pages
-
EASY SERIES P15
2 Pages
-
EASY SERIES P10
2 Pages
-
Applicators EASY Series P5
2 Pages