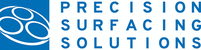
Catalog excerpts
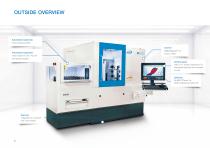
OUTSIDE OVERVIEW Automation (optional) robot loading system Control Automation (optional) chain loader KL155 / KL310 and pickup system Control panel with 21.5" screen (standard 15"), industrial keyboard and trackball mouse Software NUMROTOplus® or MTS Professional TOOL-KIT Drip pan integrated for machine and chain loader
Open the catalog to page 2
INSIDE OVERVIEW Coolant nozzle ring firmly installed on the grinding head with 14 adjustable nozzles Wheel changer 8-fold with maximum wheel diameter 150 mm or optionally 10-fold with maximum wheel diameter 100 mm Grinding spindle peak power 27 kW up to 8,000 rpm interface HSK E50 or F50 Tool gripper with automatic bushing change Interface for workpiece holder for all common clamping systems with ISO 50 interface Electronic measuring probe records all essential tool data A-axis direct drive with 9.5 kW and infinitely variable rotation speed up to 850 rpm
Open the catalog to page 3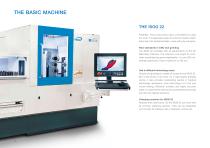
THE BASIC MACHINE THE ISOG 22 Flexibility: This is what many users of the ISOG 22 value the most. It is especially useful for small to medium batch sizes due to its vertical principle – even with only one piece. New standards in CNC tool grinding The ISOG 22 complies with all requirements of the EU Machinery Directive. The maximum tool length for automatic machining has grown significantly – to over 300 mm, whereas previously it was a maximum of 180 mm. Use in different technology areas Classic tool grinding is a matter of course for the ISOG 22. But it still knows a lot more: As a...
Open the catalog to page 4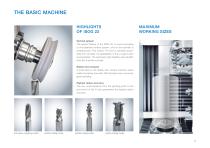
THE BASIC MACHINE HIGHLIGHTS OF ISOG 22 MAXIMUM WORKING SIZES Vertical system The special feature of the ISOG 22: It works according to the patented vertical system, and its tool spindle is perpendicular. This means: The tool is optimally accessible from all sides. Its repeatability in the μ range is also incomparable. The extremely high flexibility also benefits from this machine concept. Stable and compact A solid base is the stable cast mineral machine stand made of polymer concrete. With its large mass, it ensures good damping. Highest radius accuracy The very small distance from the...
Open the catalog to page 5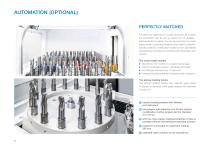
PERFECTLY MATCHED The ISOG 22 series has a modular structure. As a result, the automation can be set up exactly as it is needed -individually and in detail. You can choose from the chain loader system, the pickup loader, a robotic cell or customer-specific solutions. Automation systems from specialised manufacturers can also be combined with the single cabin solution. The chain loader system ■ attached to the machine in a space-saving way ■ 155/310 workpiece places, individually encoded ■ tool change time less than 12 seconds ■ loading/unloading possible during automatic operation The...
Open the catalog to page 6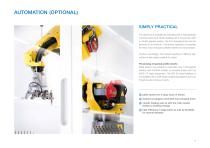
AUTOMATION (OPTIONAL) SIMPLY PRACTICAL The ISOG 22 is available as standard with a standardised machine cabin and robotic loading cell. In conjunction with a double gripper system, the tool changing times can be reduced to a minimum. Unmanned operation is possible for many hours because sufficient blanks can be provided. Another advantage: The chaotic loading of different diameters is also easily possible by robot. Processing of special profile inserts What used to be possible to automate only in the special solution with FLEXUS Invader, is possible today with the ISOG 22 basic equipment:...
Open the catalog to page 7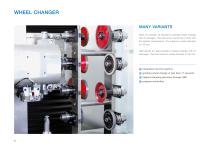
WHEEL CHANGER MANY VARIANTS ISOG 22 includes as standard a grinding wheel changer with 8 packages. This allows the machining of tools with the highest requirements. The maximum wheel diameter is 150 mm. Alternatively, it is also possible to install a changer with 10 packages. Then the maximum wheel diameter is 100 mm. integrated into the machine grinding wheel change in less than 17 seconds highest clamping precision through HSK program-controlled
Open the catalog to page 8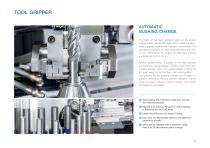
TOOL GRIPPER AUTOMATIC BUSHING CHANGE The ISOG 22 has been relying for years on the proven loading system via the CNC axes, which enables an absolutely µ-precise loading with the best concentricity. The standard tool gripper can load shank diameters from 6 to 32 mm continuously. For smaller tool diameters, there is a gripper pair of 3 to 16 mm. Another positive effect, in addition to the high precision (concentricity) during loading, is the low wear of the intermediate sleeves. Due to the vertical design of ISOG 22, the dead-weight of the tool has a self-centring effect. The grippers for...
Open the catalog to page 9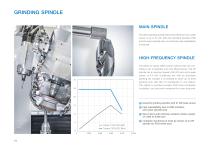
MAIN SPINDLE The direct grinding spindle drive of the ISOG 22 has a peak power of up to 27 kW. With the standard interface HSK and the exact spindle stop, an extremely high repeatability is ensured. HIGH-FREQUENCY SPINDLE The ISOG 22 series offers further options that can contribute a lot to flexibility and cost effectiveness: The HF spindle has a maximum speed of 60,000 rpm and a peak power of 4.4 kW. Combining this with an automatic grinding pin change, it is possible to stock up to three grinding pins with ISO-10 receptacles in one station. This allows to process complex PCD tools...
Open the catalog to page 10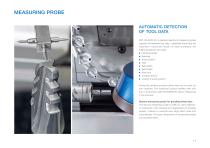
AUTOMATIC DETECTION OF TOOL DATA With the ISOG 22, a standard electronic measuring probe captures all essential tool data - especially those that are important in automatic mode. For each workpiece, the following data are recorded: ■ clamping length ■ diameter ■ tooth position ■ helix ■ flute depth ■ flute length ■ flute form ■ unequal division ■ cooling channel position During the grinding process further data can be read out and checked. Two additional vertical needles help with this, in conjunction with the NUMROTO option "Measuring in the process". Second measuring probe for grinding...
Open the catalog to page 11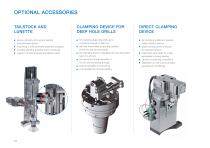
TAILSTOCK AND LUNETTE ■ secure clamping of long and slender tools between spikes ■ machining in fully automatic operation possible ■ end face grinding possible due to halved tip ■ support via automatically adjustable lunette ■ for clamping deep hole drills up to a maximum length of 650 mm ■ with the micrometer screw, the position of the tool can be set exactly ■ the clamping device is designed for tool diameters from 2 to 20 mm ■ the maximum shank diameter of 25 mm can be loaded through ■ best accessibility to the tool tip ■ only possible for manual loading DIRECT CLAMPING DEVICE ■ for...
Open the catalog to page 12All Precision Surfacing Solutions GmbH & Co. KG catalogs and technical brochures
-
Kehren RP 8
2 Pages
-
Elb-gantryLine
2 Pages
-
aba ecoLine
2 Pages
-
Micron Macro-SK
2 Pages
-
Micron Macro-S
2 Pages
-
aba powerLine
2 Pages
-
Elb-microCut
2 Pages
-
Elb-broachLine BGS
2 Pages
-
REFORM Trirex
2 Pages
-
aba multiLine
2 Pages
-
Elb-broachLine BG
2 Pages
-
Image_Brochure_PSS
11 Pages
-
Lapmaster Model 20
2 Pages
-
Lapmaster Model 15
2 Pages
-
Lapmaster Model 48
2 Pages
-
Lapmaster Model 24
2 Pages
-
Lapmaster DL 370
2 Pages
-
Lapmaster Model 36
2 Pages
-
Kehren NEO 5
2 Pages
-
Peter Wolters AC 400
2 Pages
-
Peter Wolters AC 2000
2 Pages
-
Peter Wolters AC 1000
2 Pages
-
Peter Wolters AC 700
2 Pages
-
Peter Wolters AC 535
2 Pages
-
Peter Wolters AC 1250
2 Pages
-
Peter Wolters DW 292
2 Pages
-
ELB smartLine
2 Pages
-
ELB millGrind
2 Pages
-
Elb-rotary
2 Pages
-
Peter Wolters AC 1500
2 Pages
-
Micron Macro-I
2 Pages
-
Micron Macro-SI
2 Pages
-
Kehren Ri
2 Pages
-
ISOG11
8 Pages
-
ISOG24
16 Pages
-
REFORM HSG
2 Pages
-
ISOG20
12 Pages
Archived catalogs
-
AC microLine 880 eco
2 Pages
-
AC microLine 1200 eco
2 Pages