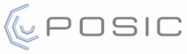
Catalog excerpts
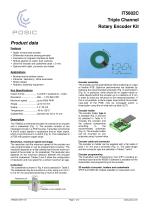
IT5602C Triple Channel Rotary Encoder Kit Product data Features • • • • • • Highly miniaturized encoder Differential inductive sensing principle Insensitive to magnetic interference fields Robust against oil, water, dust, particles Ultra-thin encoder and codewheel (total < 2 mm) Optional with cable, connector and holder Brushed and brushless motors Industrial / laboratory / office automation Rotary stages Robotics, assembly equipment Encoder assembly The encoder can be assembled by reflow soldering on a rigid or flexible PCB. Optimum performances are obtained by following the recommended schematic (Fig. 5) and footprint (Fig. 6). In particular, there should be no copper traces or metal objects behind the encoder up to a distance of 3 mm in order to avoid any influence on the measured position. If this is not possible, a blank copper layer behind the encoder (rear-side of the PCB) may be envisaged and/or a linearization using the on-chip look-up table (LUT). Description The IT5602C incremental encoder kit consists of an encoder and a codewheel (Fig. 1). The encoder consists of two integrated circuits in a PCB housing. It provides incremental A and B output signals in quadrature and an Index signal, which is synchronous to A and B (Fig. 2). The codewheel is a PCB with passive copper strips. Resolution, maximum speed and airgap The resolution and the maximum speed of the encoder are user-programmable or can be programmed ex-factory. The resolution depends on a filter setting that limits the maximum speed of the encoder vs. the codewheel. The resolution also depends on the maximum distance between the encoder and the codewheel. Tables 2 and 3 allow the configuration of resolution and max speed for a certain maximum air-gap. Codewheel The codewheel is shown in Fig. 4 and is selected in Table 5. The codewheel may be mounted on a hub, using a rim of 0.1 to 0.2 mm for accurate positioning in front of the encoder. Encoder holder The encoder holder type A is available (Fig. 7) and can be selected in Table 6. It includes the encoder and the external components according to the recommended schematic (Fig. 5). The encoder holder can be mounted on any substrate using 4 screw holes. Encoder cable and connector The encoder on holder can be supplied with a flat cable of pitch 1.27 mm and a connector (Fig. 7). The cable length and the connector type are selected in Tables 7 and 8. Encoder programming The Evaluation and Programming Tool (EPT) including an interface board and the ASSIST software is available for the linearization and programming of the encoder. 3D models of encoder, holders and codewheels STEP and IGES 3D models available on www.posic.com.
Open the catalog to page 1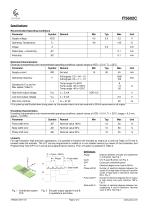
IT5602C Specifications Recommended Operating Conditions Parameter Operating Temperature Supply voltage Radial play + eccentricity Axial play Electrical Characteristics Electrical characteristics over recommended operating conditions, typical values at VDD = 5.0 V, TA = 25°C. Parameter Temp range 0 to 65°C Temp range -20 to 100°C Temp range -40 to 125°C Supply current Operating frequency Derating for FA/B and for Max speed (Table 2) High level output voltage Low level output voltage Rise time, fall time If A is pulled up and B pulled down during power-up, the encoder enters into a test mode...
Open the catalog to page 2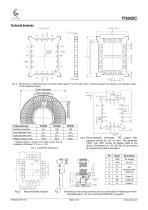
Dimensions of IT3402 encoder on encoder-holder type B. The “Encoder center” must be centered with respect to the “Readout radius” of the Codewheel (Fig 4) Codewheel type * Readout Radius = position of Encoder Center (Fig. 3) Codewheel thickness 0.73 mm +/- 10% Fig. 4 Codewheel dimensions. schematic. The supply filter capacitor should be 1µF or more. The capacitors 100nF and 10nF should be placed close to the device. Connections A1, B1, A2, B2, I2 are required for programming and linearization. Recommended footprint. Dimensions (mm) and connector pin-out of encoder on holder type A with flat...
Open the catalog to page 3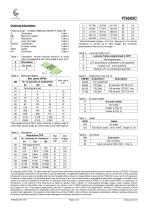
Ordering code: IT3402C-ABBCCD-EEEEE-F-GGG-HH A Orientation Table 1 BB Maximum speed Table 2 CC Resolution Table 3 D Look-Up Table Table 4 EEEEE Codewheel Table 5 F Encoder holder Table 6 GGG Cable Table 7 HH Connector Table 8 Table 1: A 0 3 Orientation. Arrows indicate direction of movement of codewheel with rising edge A prior to B. Orientation Not progr. 0° Look-Up Table (LUT) Look-Up Table programmed in OTP Not programmed LUT according to codewheel, to be specified Custom LUT, to be specified Default LUT, no codewheel specified Table 5: Codewheel (see Fig. 4) EEEEE Codewheel Description...
Open the catalog to page 4All POSIC catalogs and technical brochures
-
RSB001 RS422 Interface Board
4 Pages
-
RSB001 - RS-4022 Driver
4 Pages