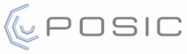
Catalog excerpts
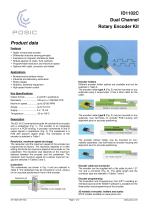
ID1102C Dual Channel Rotary Encoder Kit Product data Features • Highly miniaturized encoder • Differential inductive sensing principle • Insensitive to magnetic interference fields • Robust against oil, water, dust, particles • Programmable resolution and maximum speed • Optional with cable, connector and holder Applications • Brushed and brushless motors • Industrial and laboratory automation • Rotary stages • Robotics, assembly equipment • High-speed motion control Key Specifications Description The ID1101C incremental encoder kit consists of an encoder and a codewheel (Fig. 1). The encoder is an integrated circuit in a PCB housing. It provides incremental A and B output signals in quadrature (Fig. 2). The codewheel is a PCB with passive copper strips. The orientation of the encoder is selected in Table 1. Resolution, maximum speed and airgap The resolution and the maximum speed of the encoder are programmed ex-factory. The resolution depends on a filter setting that limits the maximum speed of the encoder vs. the codewheel. The resolution also depends on the maximum distance between the encoder and the codewheel. The resolution and maximum speed for a certain maximum air-gap are selected in Tables 2 and 3. Codewheel The codewheels are shown in Fig. 4 and are selected in Table 5. The codewheel may be mounted on a hub, using a rim for accurate positioning in front of the encoder. Encoder holders Different encoder holder options are available and can be selected in Table 6. The encoder holder type A (Fig. 5) may be mounted on any substrate using 4 screw-holes. It has a strain relief for the cable. The encoder without holder may be mounted on non-metallic substrates. Use half-holes on encoder housing and alignment pins for accurate positioning. Encoder cable and connector The encoder can be supplied with a flat cable of pitch 1.27 mm and a connector (Fig. 6). The cable length and the connector type are selected in Tables 7 and 8. Encoder programming The Evaluation and Programming Tool (EPT) including an interface board and the ASSIST software is available for the linearization and programming of the encoder. 3D models of encoder, holders and scales STEP models available on www.posic.com.
Open the catalog to page 1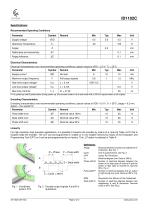
Recommended Operating Conditions Linearity For high-resolution high-precision applications, it is possible to linearize the encoder by means of a Look-Up Table (LUT) that is located inside the encoder. The LUT can be programmed in volatile or in non-volatile memory by means of the Evaluation and Programming Tool (EPT) or it can be pre-programmed by ex-factory. The LUT option is selected in Table 4. 0 = Phase P = Pulse width <-> Definitions Airgap Cycle CPR °e Phase shift O Fig. 2 Encoder output signals A and B in quadrature. Distance between encoder and codewheel in Z-direction. See Fig. 1....
Open the catalog to page 2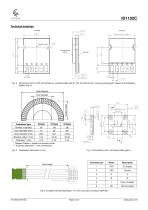
Outer diameter Inner diameter Codewheel type * Readout Radius = position of encoder center ** Thickness tolerance +/- 10% of thickness
Open the catalog to page 3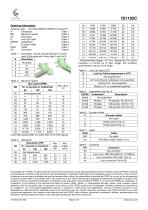
BB Maximum speed Table 2 D Look-Up Table Table 4 EEEEE Codewheel Table 5 F Encoder holder Table 6 Table 1: Orientation. Arrows indicate direction of move Table 2: Maximum speed Lower Max speed leads to a lower jitter of the A/B outputs. * Recommended airgap = 0.2 mm. Sequence of A and B transitions is correct up to Max Airgap, but encoding specifications may be out of range. Table 4: . Look-Up Table (LUT) © Copyright 2017 POSIC. All rights reserved. No part of this document may be reproduced without the prior written consent of POSIC. Products and companies mentioned in this document may be...
Open the catalog to page 4All POSIC catalogs and technical brochures
-
RSB001 RS422 Interface Board
4 Pages
-
RSB001 - RS-4022 Driver
4 Pages