
Catalog excerpts
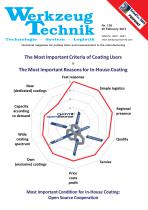
Technical magazine for cutting tools and measurement in the manufacturing
Open the catalog to page 1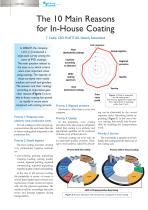
. Wmlizeiig ^echnik In 2006/07, the company L.E.K. [1] conducted a large-scale survey among the users of PVD coatings. The main question related to the issue as to which criteria were most important when using coatings. The majority of those surveyed were mainly medium and small tool grinders. The answers and their rankings according to importance gave clear reasons (Figure 1) as to why in-house coating has spread so rapidly in recent years compared with coating services. Priority 1: Response time (delivery time, production time) No tool coating provider can pick up, coat and return the...
Open the catalog to page 2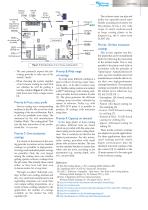
- The user primarily expects the jobcoating provider to take care of his weekly "needs". - When choosing the system supplier of an in-house coating, he must first see whether he will be getting a turnkey solution (Figure 3) with complete know-how from a single source [2]. Priority 6: Price, costs, profit Service coating was a moneymaking machine in the 80s, 90s as well as at the beginning of the new millennium. But it is still very profitable even today. The statement by the tool manufacturer Gunther Wirth: "The coating plant? That was the best innovation of my professional life." is very...
Open the catalog to page 3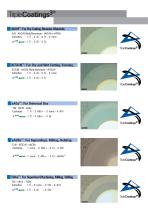
| AlCrN3®: For Dry Cutting Abrasive Materials CrN - AI/CrN Multi/Nanolayer - (AlCrN or AITiN) Cathodes: 1:Ti — 2:AI — 3:Cr — 4: none AITiCrN3®: For Dry and Wet Cutting, Forming Cr(Ti)N - AI/CrN Multi/Nanolayer - AITiCrN Cathodes: 1:Ti — 2:AI — 3:Cr — 4: none |nACo3®: For Universal Use TiN - AITiN - nACo Cathodes: 1:Ti-2: AISi+ - 3: none - 4: AITi InACRo3®: For Superalloys, Milling, Hobbing CrN - AITiCrN - nACRo Cathodes: 1:none -2:AISi + -3:Cr-4:AITi |TiXCo3®: For Superhard Machining, Milling, Drilling TiN-nACo-TiSiN Cathodes: 1:Ti-2: none - 3: TiSi - 4: AITi
Open the catalog to page 4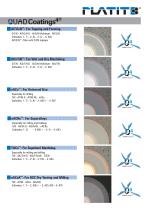
Q Coatings4® |AITiCrN4®: For Tapping and Forming CrTiN - AITiCrN-G - AI/CrN Multilayer - AITiCrN Cathodes: 1:Ti — 2:AI — 3:Cr — 4: AlCr AITiCrN4® -Tribo with CrCN toplayer AlCrTiN4®: For Wet and Dry Machining CrTiN - AICrTiN-G - AI/CrN Multilayer - AlCrTiN Cathodes: 1:Ti — 2:AI — 3:Cr — 4: AlCr Especially for drilling TiN-AITiN-G-AITiN-NL-nACo Cathodes: 1:Ti — 2:AI — 3: AISi+ - 4: AITi |nACRo4®: For Superalloys Especially for milling and hobbing CrN - AICrN-G - AICrN-NL - nACRo Cathodes: 1: Cr -2:AISi+ -3: Cr-4: AlCr ■TiXCo4®: For Superhard Machining Especially for milling and drilling TiN...
Open the catalog to page 5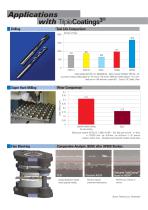
Tool Life Comparison Number of holes Solid carbide drill; 0 8 mm; DIN6539-D8 - Work material 42CrMoV, HRC 30~32; successive cutting; drilling depth ap=24 mm Vc 150 m/min; 5968 rpm; feed/rotation f=0.15 mm; feed rate vf=895 mm/min; coolant 8%-Source: TDC Dalian, China Work piece material: X210Cr13,1.2080, 64 HRC— Tool: Ball nose end mill - d=6mm n= 16'820 1/min-ap=0.09 mm-ae=0.06 mm-f=0.1 mm/rev Coolant: cold air 5 bar - Developed and tested for HyoShin, South Korea Comparative Analysis (SEM) after 30'000 Strokes Coating detached, maintenance urgently needed. Element requires preventive...
Open the catalog to page 6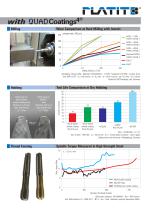
PLATi"with lJ Coatings4®| Milling§t;5§§§l2t;tt§5f2 Wear Comparison at Hard Milling with Inserts AITiN + TiSiN market coating 1 AITiN + AlCrN market coating 2 TiAIN + AlCrN market coating 3 Improved AITiN-L market coating 4 TiXCo4 nACo4 milling distance: Lf [m] Workpiece: Wave profile - Material: X155CrVMo12 - 1.2379 - hardened to 55HRC- coolant: IC-air Tool: WPR 16-SF - vc=240 m/min - fz=0.2 mm - vf=1910 mm/min - ap=0.2 mm - ae=0.3mm Tested by LMT-Kieninger, Lahr, Germany Tool Life Comparison at Dry Hobbing Flankwear on AlCrSi-based market coating with thickness of 3.9 pm after tool life...
Open the catalog to page 7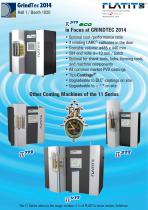
Advanced Coating Systems SWISSjETQUALITY www.platit.com 7 in Focus at GRINDTEC 2014 • Optimal cost-/performance ratio • 3 rotating LARC®-cathodes in the door • Coatable volume: 0485 x 440 mm • 504 end mills d=10 mm / batch • Optimal for shank tools, hobs, forming tools, and machine components • All common market PVD coatings • Triple Coatings3® • Upgradeable to DLC2-coatings on site • Upgradeable to n3Tt on site Other Coating Machines of the 11 Series
Open the catalog to page 8All PLATIT AG catalogs and technical brochures
-
Short Catalog
52 Pages
-
Compendium
140 Pages
-
CCS Custom Coating Solutions
12 Pages
-
Hybrid Coating
4 Pages
-
PLATIT’s new DLC coatings
2 Pages
-
Complete Solutions in Demand
6 Pages
-
Productive Decoating
4 Pages
-
Coatings with Boron
4 Pages
-
Dedicated Coating Systems
5 Pages
-
My Tool, My Coating
6 Pages
-
New Quad Coatings
8 Pages
-
Coating of Large Chunks
4 Pages