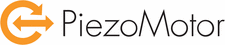

Catalog excerpts
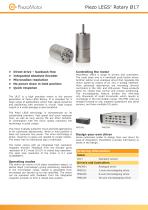
Piezo LEGS Rotary Ø17 ® Direct drive – backlash free Integrated Absolute Encoder Microradian resolution No power draw in hold position Quick response The LR17 is a high precision motor in the second generation of Piezo LEGS Rotary. It is intended for a large range of applications where high speed dynamics and positioning with precision is crucial. High torque output in a small package is also beneficial. PiezoMotor offers a range of drivers and controllers. The most basic one is a handheld push button driver. Another option is an analogue driver that regulates the motor speed by means of an ±10 V analog interface. More advanced alternatives are microstep drivers/ controllers in the 100- and 200-series. These products allow for closed loop control and precise positioning. The microstepping feature divides the wfm-step into thousands of small increments which results in microsteps in the microradian range. The PMD units are straight forward to use, supports quadrature and serial sensors, and have multiple I/O ports. The Piezo LEGS technology is characterized by its outstanding precision. Fast speed and quick response time, as well as long service life are other benefits. In combination with the micro radian resolution the technology is quite unique. The motor is ideally suited for move and hold applications or for automatic adjustments. When in hold position it does not consume any power. The drive technology is direct, meaning no gears are needed to create motion. The motor has no mechanical play or backlash. The motor comes with an integrated high resolution magnetic encoder. Feedback from the encoder gives resolution of 0.2 mrad (0.01º) in closed loop operation. The open loop resolution of the motor is 0.1 µrad (0.000006º). Operating modes The motor can move in full steps (waveform-steps), or partial steps (microsteps) giving positioning resolution in the microradian range. Speed is adjustable from microsteps per second up to max specified. The motor can be operated with feedback from the integrated magnetic encoder to form a closed loop system. Design your own driver Some customers prefer to design their own driver for ease of integration. PiezoMotor provides information to assist in the design. Ordering information Motor LR17 Standard version Analogue driver
Open the catalog to page 1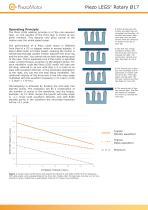
Piezo LEGS Rotary Ø17 ® Operating Principle 1 When all legs are electrically activated they are elongated and bending. As we shall see below, alternate legs move as pairs. Arrows show the direction of motion of the tip of each leg. The Piezo LEGS walking principle is of the non-resonant type, i.e. the position of the drive legs is known at any given moment. This assures very good control of the motion over the whole speed range. The performance of a Piezo LEGS motor is different from that of a DC or stepper motor in several aspects. A Piezo LEGS motor is friction based, meaning the motion...
Open the catalog to page 2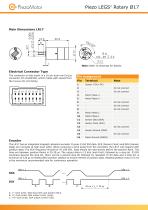
Piezo LEGS Rotary Ø17 ® Electrical Connector Type The connector on the motor is a 16 pin dual row CviLux connector CI1116M2VD0, which mates with socket from 1 the CviLux CI1116 family. Note: Refer to drawings for details. Motor Phase 2 Motor Phase 1 Sensor Data (SDA) Sensor Clock (SCK) Motor Ground (GNDM) The LR17 has an integrated magnetic absolute encoder. It gives 15 bit SSI data. SCK (Sensor Clock) and SDA (Sensor Data) are normally at high level (idle). When receiving a clock pulse from the controller, the LR17 will respond with position data. The SCK frequency should be 70-180 kHz....
Open the catalog to page 3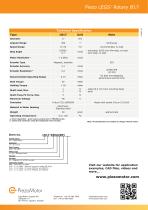
Piezo LEGS Rotary Ø17 Technical Specification Type Angular Range Speed Range Encoder Type Step Angle Motor Resolution - microstep, 8192a per wfm-step, no load - wfm-step, no load Magnetic, absolute Encoder Accuracy for best microstepping performance and life time Shaft Press Fit Force, Max. Encoder Resolution Recommended Operating Range Stall Torque Holding Torque Maximum Voltage Connector Mates with socket CviLux CI1116S Aluminium, Stainless Steel Material in Motor Housing Weight Operating Temperature a. Driver dependent - given values using driver in PMD200-series. b. Closed loop...
Open the catalog to page 4All PiezoMotor AB catalogs and technical brochures
-
LR23-50
2 Pages
-
LR23-80
2 Pages
-
PMD101 Technical Manual
42 Pages
-
Analogue Driver PMCM31
4 Pages
-
Microstepping Driver 206
2 Pages
-
PiezoMotor Brochure
8 Pages
-
PMD101 - Microstep Driver
2 Pages
-
Piezo LEGS Caliper 20N
4 Pages
-
Piezo LEGS Rotary 50mNm
4 Pages
-
Piezo LEGS Rotary 80Nmm
4 Pages
-
Piezo LEGS Linear 6N
4 Pages
-
Piezo LEGS Linear Twin-C 20N
4 Pages
-
Piezo LEGS Linear Twin 20N
4 Pages
-
Piezo LEGS WavePlate
4 Pages
-
Piezo LEGS Linear Twin-C 40N
4 Pages
-
Piezo LEGS® Rotary Ø17
4 Pages