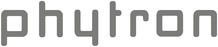
Catalog excerpts

www.phytron.eu www.phytron.us CATALOGUE STEPPER MOTORS Precision for challenging applications INDUSTRIAL VACUUM | CRYO | RADIATION VIBRATION | VACUUM | RADIATION Edition 2018 November Extreme. Precision. Positioning
Open the catalog to page 1
Phytron GmbH Stepper motor technology for special requirements: Stepper motor technology is particularly suitable for precision applications under extreme environmental conditions. Whether vacuum, cryo environment, high temperature or under the influence of radioactivity - the Phytron motor series are tough and do precision work, because stepper motors can position very accurately without a fragile feedback encoder. Our control units perform, especially in applications that rely on very precise and smooth running behaviour. We control motors in electron microscopes, accelerator experiments...
Open the catalog to page 2
INDUSTRIAL Environments Precise. Reliable. Dynamic. Phytron‘s STANDARD industrial motors are eminently suitable for applications in engineering and industry. Whether it‘s for the positioning of slides, the adjustment of pressure rollers or sensitive optics, the synchronised delivery and application of labels or for handling in mail sorting - fast and reliable running performances are constantly demanded. Precision, high torque and solid craftsmanship make our standard industrial motors an excellent choice for environments up to IP 50. Precision stepper motor with smooth running, IP 40, 19...
Open the catalog to page 3
For Applications with Extended Temperature Range The proven 2-phase hybrid stepper motors series ZSS combine highest precision with smooth running characteristics. With up to 102.400 approachable positions (200-step motor, driven in micro stepping mode with 1/512 step resolution and encoder) the ZSS motor provides your application with highest precision positioning capabilities. Perfect-fit for your application: The ZSS serie differs from standard market motors by the extended ambient temperature range from -30 to +80 °C. • with encoder • with gear - GPL low-backlash planetary gears PLG...
Open the catalog to page 4
Industrial Stepper Motor ZSS 19 to ZSS 57 ZSS 19 to 33 with free wire ends ZSS 41 to 57 with protective cover Standard motor flange Dimensions / Electrical and Mechanical Characteristics Inductivity/ Phase Loads axial Detent torque Resistance/ Phase Mechanical Characteristics Rotor inertia Electrical Characteristics Standard 8-lead, motor connection see page 3 Holding torque in bipolar mode with parallel windings, two phases on rated current 3) The inductivity values apply for each single winding as well as for parallel connected windings. 4) ZSS 52, 56 and 57 with earthing screw on the...
Open the catalog to page 5
Electrical Connection / Connection Types / Phase Current Phase currents The Phytron stepper motors type ZSS are built in 8-lead windings (standard). For ZSS Phytron stepper motors, the rated current [A] per motor phase is printed on the rating plate. The last digits of the motor‘s type number define the rated current. Example: ZSS 32.200.1,2 The rated current is defined for full step operation, at bipolar control mode, with parallel connected motor windings. According to the connection mode, the motor windings receive different currents. Therefore, for identical power dissipation in the...
Open the catalog to page 6
Industrial Option: Stepper Motor with Encoder The stepper motors ZSS 25 to ZSS 57 with mounted encoder are particularly suitable for use in control actuators or for system monitoring. • Motor connection by free wire ends • Encoder connection with flat cable with 10-pin connector • Protection class IP20 side view front view rear view Technical characteristics of the encoder Resolution: Output current: Output voltage: Supply current: Count frequency: Supply voltage:
Open the catalog to page 7
Option: Stepper Motor with Motor Brake For the stepper motors ZSS 32 to ZSS 57 a mounted 24 VDC permanent magnet motor brake is optionally available. ZSS 32 to 43: KEB 01: Power 8 W / nominal torque 0.4 Nm; electrical connection: free wire ends Power 10 W / nominal torque1 Nm; electrical connection: circular connector K Side view Motor brake Front view Stepper motor Option: Stepper Motor with Heat Sink The ZSS stepper motors are also available with a mounted heat sink.Depending on the motor‘s mounting position, a heat sink with radial fins (K1) or axial fins (K2) can be selected. The use of...
Open the catalog to page 8
Industrial Option: Stepper Motor with GPL Low-Backlash Planetary Gear z1 Mass (motor and gear) in kg Dimensions in mm Stepper motor Mass /Permissible Loads / Protection Class Gear Mass without motor 1-stage Permissible axial load Perm. radial load (center of shaft) Protection Protection class class gear + motor
Open the catalog to page 9
GPL Gear Mechanical Characteristics Stepper Motor with GPL Gear • Stepper motor mounted gear • 1- to 3-stage planetary gear • Low gear backlash Mechanical gear characteristics Average mass inertia at output Torsional stiffness Emergency stop torque No-load backlash Low-backlash Emergency stop torque No-load backlash Reduction ratios Stepper motor - Standard: 20 to 50 arcmin - Low-backlash: 6 to 15 arcmin • Maximum permanent torque 0.1 to 38 Nm • 100% permissible short-term overload • Adapted for permanent, alternate or intermittent operation • Ideal for combinations with toothed belt...
Open the catalog to page 10
Industrial ZSS Stepper Motor with HD Gear The Harmonic Drive® gears are based on a totally new operating principle. The transmission force is exerted by a resilient deformable toothed steel cylinder flexspline which transmits the motor rotation to the drive shaft. Drive shaft and output shaft direction is are opposed. Backlash and torsional stiffness Harmonic Drive® gears have particularly low backlash. In practice, the tooth-contour backlash can be neglected (see page 9). The total gear torsion is equal to the sum of ½ backlash + torque/resillient constant. with mounted stepper motor ZSS...
Open the catalog to page 11
Spring constant Permissible bearing load axial Permissible bearing load radial Rotor mass inertia 1) Max. permissible off drive torque Reduction ratio Mass motor with gear Stepper motor Dimensions and Mechanical Characteristics Note: Motor dimensions and technical data: see page 2. Mass inertia of the motor: see page 2.
Open the catalog to page 12All Phytron GmbH catalogs and technical brochures
-
phyBASIC
4 Pages
-
APS Technology
4 Pages
-
phySPACE Stepper Motors
12 Pages
-
ZSS Stepper Motors
12 Pages
-
LA Linear Actuator
4 Pages
-
SLS
4 Pages
-
MSX
4 Pages
-
phyMOTION
20 Pages
-
VSS Stepper motors in vacuum
15 Pages
-
TM StepDrive 24-48V/5A
4 Pages
-
ZSH Stepper Motor
15 Pages
-
CONTROL for all Dimensions
80 Pages
-
SP-MINI
2 Pages
-
ServiceBus-Comm
2 Pages
-
MiniLog-Comm
2 Pages
-
phyLOGIC ToolBox
2 Pages
-
Stepper Motors phyBASIC
4 Pages
-
OMC/TMC
4 Pages
-
phySPACE
12 Pages
-
VSS Stepper Motor
16 Pages
-
ZSH Stepper Motors
12 Pages
-
1-STEP-DRIVE
4 Pages
-
MCC-2
4 Pages
-
MCC-1
4 Pages
-
ZMX+
4 Pages
-
MCD+
4 Pages
-
DMP 20/29/37
2 Pages