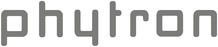
Catalog excerpts

1–STEP–DRIVE–5A–48V Stepper motor module for the SIMATIC ET 200®S In Focus In coordination with SIEMENS ® The 1-STEP-DRIVE-5A-48V is a stepper motor controller with integrated power stage. It is specially developed for application in the decentralised SIMATIC ET 200®S peripheral system. SIMATIC ET 200 S with a fully integrated, egrated, powerful and high-precision positioning conng troller for 2 phase stepper motors. This 1-STEP-DRIVE module is configured via mouse click with the STEP®7 by using the provided configuration files and then parameterised. The module is ready for use in a very short time and supplements the Application examples for the 1-STEP-DRIVE module are assembly and transfer lines, building automation, x-y-tables, paper mills, printing and textile machines. Integrated Driver Application The 1-STEP-DRIVE-5A-48V module successfully completed the system compliance test performed by SIEMENS. These Phytron power stages are eminently suitable for not only setting the basic parameters via interface bus, but also the technological parameters found in the application. certain micro step positions cannot often be reached because of a lack of fine current settings and the motor may not reach the desired position. The 1-STEP-DRIVE technology guarantees a high-precision current The power stage can be optimised for the requirements of the drive system during commissioning. Furthermore it is possible to adjust the power stage during ´CPU RUN´, particularly for the next program sequence. For example, raise the stop current when the motor is holding a load and then reduce it as soon as the system comes to a standstill without the load to minimize the power requirement and motor heating. Using these functions combined with additional parameters bring out the best in your system. Fine positioning to 1/512 step Almost all commercially available stepper motor power stages can be operated in micro step mode. When driving the motor with encoder feedback, it is apparent that adjustment and enables fine positioning up to 1/512 step. The diagram above shows that a Phytron 200 step motor with encoder is able to be at each 1/512 micro step position with an absolute and non-cumulative error of about 0.0015°, typically much less than this. • Stepper motor controller with an integrated power stage for SIMATIC ET 200®S • For 2 phase stepper motors • 5 APEAK at 24 to 48 VDC • Up to 1/512 microsteps • Online controller parameterisation and diagnostics • STEP®7 programming Online parameterisation Edition 2015 March Extreme. Precision. Positioning.
Open the catalog to page 1
Specification Mechanical Design SIMATIC ET 200®S plastic housing Mounting position Plug-in in SIMATIC ET 200®S terminal modules Features Stepper motors Suitable for bipolar control of 2 phase stepper motors with 4, (6) or 8 lead wiring Superior main station Power supply Reverse polarity protection Phase current 5 APEAK (short circuit-proof, overload protected) Motor current adjustment Step resolutions Maximum step frequency Physical resolution Approx. 102,400 positions per revolution (0.0035°/step) with a 200 step motor. An encoder with a counter should be considered for very fine...
Open the catalog to page 2
Specification Features (continued) Support of linear and modulo axes (rotary axes) Hardware error detection • Over current, short circuit >10 A spike at the controller • Over temperature at the power stage T > 85 °C Refresh rate Analogue outputs A, B, C, D - For a 2 phase stepper motor Digital inputs 2 configurable digital inputs IN0 and IN1: 0 signal: -30 to 5 V with 2 mA max. (quiescent current) 1 signal: 11 to 30 V with 9 mA typical Input delay: 4 ms IN0: • External release of momentum • External stop • Limit switch towards forward / reverse (Limit switch) IN1: • Reference switch and...
Open the catalog to page 3
Specification Communication and Programming (continued) Data set transfer to the 1-STEP-DRIVE (asynchronous while CPU RUN) Data set transfer from the 1-STEP-DRIVE (asynchronous) Parameterising the 1-STEP-DRIVE power stage • Step resolution (1/1, 1/2 up to 1/512) • Preferred direction of rotation • Run current (20 mA increments) • Stop current (20 mA increments) • Boost current (20 mA increments) • Current delay time 1 up to 1000 ms • Chopper frequency 18 to 25 kHz • Switching frequency overdrive 1 to 40 kHz • ODIS behaviour Diagnostics Feedback of the following driver parameters to the main...
Open the catalog to page 4All Phytron GmbH catalogs and technical brochures
-
phyBASIC
4 Pages
-
APS Technology
4 Pages
-
phySPACE Stepper Motors
12 Pages
-
ZSS Stepper Motors
12 Pages
-
LA Linear Actuator
4 Pages
-
SLS
4 Pages
-
MSX
4 Pages
-
phyMOTION
20 Pages
-
VSS Stepper motors in vacuum
15 Pages
-
TM StepDrive 24-48V/5A
4 Pages
-
ZSH Stepper Motor
15 Pages
-
CONTROL for all Dimensions
80 Pages
-
SP-MINI
2 Pages
-
ServiceBus-Comm
2 Pages
-
MiniLog-Comm
2 Pages
-
phyLOGIC ToolBox
2 Pages
-
Stepper Motors phyBASIC
4 Pages
-
OMC/TMC
4 Pages
-
phySPACE
12 Pages
-
VSS Stepper Motor
16 Pages
-
ZSH Stepper Motors
12 Pages
-
MCC-2
4 Pages
-
MCC-1
4 Pages
-
ZMX+
4 Pages
-
MCD+
4 Pages
-
DMP 20/29/37
2 Pages