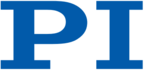

Catalog excerpts
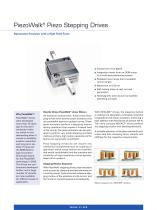
■ Forces from 10 to 800 N ■ Integration levels from an OEM motor to a multi-axis positioning system ■ Scalable travel range due to scalable runner length ■ Resolution to 0.03 nm ■ Self-locking when at rest, no heat generation ■ Nonmagnetic and vacuum-compatible operating principle Why PiezoWalk®? PiezoWalk® drives were developed more than 10 years ago for the semiconductor industry, which is very demanding when it comes to reliability, position resolution and long-term stability. PI received the SEMI Technology Innovation Showcase Award for the PiezoWalk® technology in 2005. The drives are continuously developed further, and a large number of variants are now available for different areas of application. Directly Driven PiezoWalk® Linear Motors As essential components, these piezo stepping drives have several piezo actuators that are preloaded against a guided runner. These piezo actuators perform a stepping motion during operation that causes a forward feed of the runner.The piezo actuators can be operated to perform very small stepping and feed motions so that a high motion resolution of far below one nanometer is achieved. Piezo stepping drives do not require any mechanical components such as coupling or gearhead, which cause friction and backlash and would considerably limit the precision and reliability of high-resolution motor-spindle-based drive systems. Stepping Motion Sequence With PiezoWalk® stepping drives, piezo actuators work in pairs as clamping and feed elements on a moving runner. Cyclical control induces a stepping motion of the actuators on the runner, and the runner is moved forwards and backwards. With NEXLINE® drives, the stepping motion is realized via separately controlled, powerful longitudinal and shear actuators, achieving a high stiffness with feed forces of several 100 N. The more compact NEXACT® drives perform the stepping motion with bending elements. A suitable selection of the piezo elements optimizes step size, clamping force, velocity and stiffness for the respective requirements.
Open the catalog to page 1
Piezomotors are Self-Locking Preloading the piezoceramic actuators against the runner ensures self-locking of the drive when at rest and switched off. As a result, it does not consume any power, does not heat up, and keeps the position mechanically stable. Applications with a low duty cycle that require a high time and temperature stability profit from these characteristics. Lifetime and Reliability The motion of the piezoceramic actuator is based on crystalline effects and is not subject to any wear. Unlike other piezomotor principles, the coupling of the piezo actuators to the runner is...
Open the catalog to page 2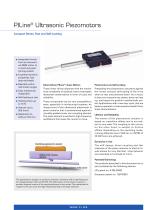
PILine® Ultrasonic Piezomotors Compact Drives, Fast and Self-Locking Integration levels from an economical OEM motor to a multi-axis positioning system Excellent dynamic properties, fast step-and-settle Basically unlimited travel ranges Easy mechanical integration Direct-Driven PILine® Linear Motors These linear drives dispense with the mechanical complexity of classical rotary motor/gear/ leadscrew combinations in favor of costs and reliability. Preloading the piezoceramic actuators against the runner ensures self-locking of the drive when at rest and powered down. As a result, it does not...
Open the catalog to page 3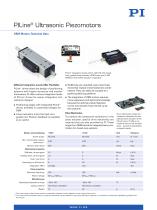
PILine® integration levels (left to right): M-272 closed-loop, guided linear actuator, OEM motor and U-264 RodDrive low-profile actuator (unguided) Different Integration Levels Offer Flexibility PILine® drives allow the design of positioning systems with higher dynamics and smaller dimensions. PI offers various integration levels of PILine® drives for easier integration into customer designs: ■ Positioning stages with integrated PILine® drives, available in customized designs for OEM ■ Linear actuators move the load via a guided rod. Position feedback is available as an option ■ RodDrives...
Open the catalog to page 4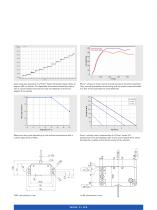
Open-loop step sequence of a PILine® based translation stage. Steps of approx. 300 nm shown. For repeatable increments closed-loop operation is recommended, because the step size depends on the force applied from outside PILine® ultrasonic linear motors provide excellent dynamic properties. They provide acceleration to several g and can achieve step-and-settle of a few 10 microseconds for small distances Maximum duty cycle depending on the ambient temperature with a control signal level of 100% Force / velocity motor characteristic of a PILine® motor 6 N holding force. The percentages refer...
Open the catalog to page 5
Cost-Efficient, Compact Linear Motors PIShift drives are space-saving and cost-efficient piezo-based drives with relatively high holding forces of up to 10 N and a basically unlimited travel range. They make use of the stick-slip effect (inertia effect) - a cyclical alternation of static and sliding friction between a moving runner and the drive element generated by the piezo element - for a continuous feed of the runner. With an operating frequency above 20 kHz, PIShift drives reach velocities of more than 5 mm/s. Silent and Energy-Saving The drive works silently at this frequency. When at...
Open the catalog to page 6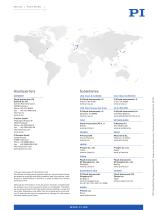
Headquarters GERMANY_ © Physik Instrumente (PI) GmbH & Co. KG All contents, including texts, graphics, data etc., as well as their layout, are subject to copyright and other protective laws. Any copying, modification or redistribution in whole or in parts is subject to a written permission of PI. Although the information in this document has been compiled with the greatest care, errors cannot be ruled out completely. Therefore, we cannot guarantee for the information being complete, correct and up to date. Illustrations may differ from the original and are not binding. PI reserves the right...
Open the catalog to page 7All Physik Instrumente catalogs and technical brochures
-
A-143
5 Pages
-
A-811.CE
3 Pages
-
G-902.RxI
5 Pages
-
P-405
4 Pages
-
PRYY
7 Pages
-
A-523
5 Pages
-
M-110 • M-111 • M-112 V6
4 Pages
-
L-812
18 Pages
-
RS-40 V7
4 Pages
-
A-68x
4 Pages
-
G-901
9 Pages
-
G-910.RC02
6 Pages
-
F-712.IRP
6 Pages
-
G-910.RC01 • RC03
4 Pages
-
C-663.12
3 Pages
-
C-887.53x
5 Pages
-
Piezoelectric Discs
7 Pages
-
L-402
5 Pages
-
P-840
4 Pages
-
M-238
5 Pages
-
L-220
5 Pages
-
P-725
9 Pages
-
C-413
3 Pages
-
P-518 • P-528 • P-558
6 Pages
-
PL112 – PL140
4 Pages
-
U-628
3 Pages
-
P-545.3D8S
5 Pages
-
P-611.XZ • P-611.2
4 Pages
-
P-541.2 • P-542.2
5 Pages
-
Leading in Precision Positioning
12 Pages
-
Engineered Systems
8 Pages
-
Precision Motion Control
4 Pages
-
Drivetrain Elements
4 Pages
-
Motors and Drives
3 Pages
-
Positioning with Piezo Systems
248 Pages
-
Hexapod Positioning Systems
133 Pages
-
PIRest Actuators - P-131
4 Pages
-
High-Load Linear Stage - L-417
12 Pages
-
PICA piezo amplifier module
3 Pages
-
V-412 • V-418 • V-423
2 Pages
-
S-335 Fast Tip/Tilt Platform
3 Pages
-
Q-Motion® SpaceFAB
4 Pages
-
A-131
5 Pages
-
d-891
1 Pages
-
PI Datasheet V-275
5 Pages
-
PI Datasheet V-273
5 Pages
-
PI Datasheet VT-80
3 Pages
-
A-65x
4 Pages
-
A-60x.MTT
1 Pages
-
A-80x
3 Pages
-
A-322
3 Pages
-
A-110
3 Pages
-
A-141
3 Pages
-
A-123
5 Pages
-
A-121
5 Pages
-
DT-34
4 Pages
-
D-015 • D-050 • D-100
5 Pages
-
A-10x
3 Pages
-
New Products 2015
48 Pages
-
PI Products for Microscopy
36 Pages
-
PI Electron Microscopy
16 Pages
-
Piezo Motors and Stages
48 Pages
-
Piezo Mike Linear Actuators
16 Pages
-
PI Product Overview
34 Pages
-
PILine® Ultrasonic Piezomotors
20 Pages
-
Piezoelectric Actuators
74 Pages
-
Hexapods 6-Axis Stages
56 Pages
-
Piezo Amplifiers & Controllers
44 Pages