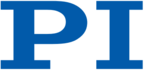

Catalog excerpts
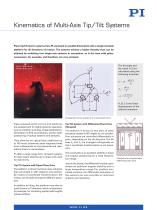
Kinematics of Multi-Axis Tip/Tilt Systems Piezo tip/tilt mirror systems from PI are based on parallel kinematics with a single movable platform for all directions of motion. The systems achieve a higher linearity than can be attained by switching two single-axis systems in succession, as is the case with galvanoscanners, for example, and therefore, are very compact. Horse head nebula (Photo: Brian Lula) The tilt angle and the travel in Z are calculated using the following formulas: A, B, C is the linear displacement of the relevant actuators. Arrangement of the actuators of a tripod piezo drive They allow for an optical beam deflection up to 100 mrad, extremely short response times from milliseconds to microseconds and resolutions down to nanoradians. The platform is driven by two pairs of piezo actuators located in 90° angles to one another. Four actuators are controlled differentially in pairs, depending on the tilt direction. The tilt axes θX and θY are arranged orthogonally so that a coordinate transformation is not necessary. PI offers a large range from compact systems for laser beam steering up to large units used for astronomy. This concludes in an excellent stability in linear and angular positioning for a wide temperature range. Tip/Tilt System with Tripod Piezo Drive The platform is driven by three piezo actuators that are located in 120° angles to one another. By means of coordinate transformation, the motion can be split among the different actuators. Just as the tripod, the differential version guarantees an optimum angular stability over a large temperature range. For position controlled versions, the differential evaluation of two sensors per axis provides an improved linearity and resolution. In addition to tilting, the platform may also be used linearly in Z direction, which is important, for example, for correcting optical path lengths (phase shifters). Tip/Tilt System with Differential Piezo Drive (Tetrapod) Piezo-actuated tip/tilt mirrors and platforms are suitable both for highly dynamic operation, such as tracking, scanning, image stabilization, elimination of drift and vibration, and for static positioning of optical systems and samples. Principle of a tilt system with differential piez
Open the catalog to page 1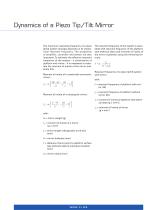
The maximum operating frequency of a piezo tip/tilt system strongly depends on its mechanical resonant frequency. The properties of amplifier, controller and sensor are also important. To estimate the effective resonant frequency of the system - a combination of platform and mirror - it is necessary to calculate the moment of inertia of the mirror substrate first. Moment of inertia of a rotationally symmetric mirror: The resonant frequency of the system is calculated with resonant frequency of the platform (see technical data) and moment of inertia of the mirror substrate using the...
Open the catalog to page 2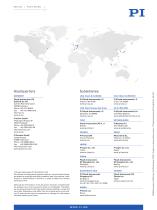
Headquarters GERMANY_ © Physik Instrumente (PI) GmbH & Co. KG All contents, including texts, graphics, data etc., as well as their layout, are subject to copyright and other protective laws. Any copying, modification or redistribution in whole or in parts is subject to a written permission of PI. Although the information in this document has been compiled with the greatest care, errors cannot be ruled out completely. Therefore, we cannot guarantee for the information being complete, correct and up to date. Illustrations may differ from the original and are not binding. PI reserves the right...
Open the catalog to page 3All Physik Instrumente catalogs and technical brochures
-
A-143
5 Pages
-
A-811.CE
3 Pages
-
G-902.RxI
5 Pages
-
P-405
4 Pages
-
PRYY
7 Pages
-
A-523
5 Pages
-
M-110 • M-111 • M-112 V6
4 Pages
-
L-812
18 Pages
-
RS-40 V7
4 Pages
-
A-68x
4 Pages
-
G-901
9 Pages
-
G-910.RC02
6 Pages
-
F-712.IRP
6 Pages
-
G-910.RC01 • RC03
4 Pages
-
C-663.12
3 Pages
-
C-887.53x
5 Pages
-
Piezoelectric Discs
7 Pages
-
L-402
5 Pages
-
P-840
4 Pages
-
M-238
5 Pages
-
L-220
5 Pages
-
P-725
9 Pages
-
C-413
3 Pages
-
P-518 • P-528 • P-558
6 Pages
-
PL112 – PL140
4 Pages
-
U-628
3 Pages
-
P-545.3D8S
5 Pages
-
P-611.XZ • P-611.2
4 Pages
-
P-541.2 • P-542.2
5 Pages
-
Leading in Precision Positioning
12 Pages
-
Engineered Systems
8 Pages
-
Precision Motion Control
4 Pages
-
Drivetrain Elements
4 Pages
-
Motors and Drives
3 Pages
-
Positioning with Piezo Systems
248 Pages
-
Hexapod Positioning Systems
133 Pages
-
PIRest Actuators - P-131
4 Pages
-
High-Load Linear Stage - L-417
12 Pages
-
PICA piezo amplifier module
3 Pages
-
V-412 • V-418 • V-423
2 Pages
-
S-335 Fast Tip/Tilt Platform
3 Pages
-
Q-Motion® SpaceFAB
4 Pages
-
A-131
5 Pages
-
d-891
1 Pages
-
PI Datasheet V-275
5 Pages
-
PI Datasheet V-273
5 Pages
-
PI Datasheet VT-80
3 Pages
-
A-65x
4 Pages
-
A-60x.MTT
1 Pages
-
A-80x
3 Pages
-
A-322
3 Pages
-
A-110
3 Pages
-
A-141
3 Pages
-
A-123
5 Pages
-
A-121
5 Pages
-
DT-34
4 Pages
-
D-015 • D-050 • D-100
5 Pages
-
A-10x
3 Pages
-
New Products 2015
48 Pages
-
PI Products for Microscopy
36 Pages
-
PI Electron Microscopy
16 Pages
-
Piezo Motors and Stages
48 Pages
-
Piezo Mike Linear Actuators
16 Pages
-
PI Product Overview
34 Pages
-
PILine® Ultrasonic Piezomotors
20 Pages
-
Piezoelectric Actuators
74 Pages
-
Hexapods 6-Axis Stages
56 Pages
-
Piezo Amplifiers & Controllers
44 Pages