
Catalog excerpts
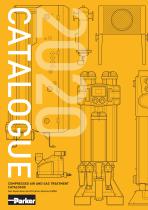
Gas Separation and Filtration Division EMEA - COMPRESSED AIR AND GAS TREATMENT CATALOGUE 2020 COMPRESSED AIR AND GAS TREATMENT CATALOGUE Gas Separation and Filtration Division EMEA ©2020 Parker Hannifin Corporation. All rights reserved.
Open the catalog to page 1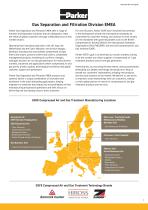
Gas Separation and Filtration Division EMEA Parker Gas Separation and Filtration EMEA offer a range of filtration and separation solutions that are designed to meet the needs of global customers through a dedicated focus on key market sectors. Operating from manufacturing sites in the UK, Italy, the Netherlands and the Czech Republic, the division designs, develops, manufactures and markets compressed air/gas filters and dryers, process chillers and coolers, condensate management products, breathing air purifiers, nitrogen, hydrogen and zero air on-site gas generators for many diverse...
Open the catalog to page 3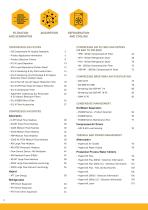
- ISO Compressed Air Quality Standards 4 - Product Application Information 6 - Product Selection Criteria 8 - OIL-X Liquid Separator 10 - SFH Liquid Separators (Carbon Steel) 12 - OIL-X Coalescing & Dry Particulate Filters 14 - OIL-X Coalescing, Dry Particulate & Oil Vapour 16 Reduction Filters (Carbon Steel) - OIL-X Point Of Use Oil Vapour Reduction Filter 18 - OIL-X OVR Plant Scale Oil Vapour Reduction 20 - OIL-X Combination Filter 22 - Hyperfilter Coalescing, Dry Particulate 24 & Oil Vapour Reduction Filters - OIL-X 0003G Micro Filter 26 - OIL-X Filter Accessories 27 COMPRESSED AIR...
Open the catalog to page 4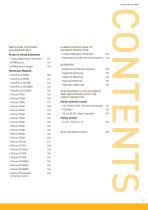
INDUSTRIAL NITROGEN GAS GENERATORS Pressure Swing Adsorption - Product Application Information 112 Membrane Modules Correction Factors CARBON DIOXIDE QUALITY INCIDENT PROTECTION - Product Application Information 146 - PCO2 Quality Incident Protection Systems 148 - Biogas Dehumidification Systems 150 REPLACEMENT FILTER ELEMENTS AND MAINTENANCE KITS FOR LEGACY PRODUCTS Parker domnick hunter - OIL-X EVOLUTION / OIL-Xplus Advantage 154 Parker Zander Parker Worldwide Contacts 158
Open the catalog to page 5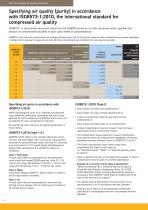
ISO Compressed Air Quality Standards Specifying air quality (purity) in accordance with lSo8573-1:2010, the international standard for compressed air quality ISO8573-1 is the primary document used from the ISO8573 series as it is this document which specifies the amount of contamination allowed in each cubic metre of compressed air. ISO8573-1 lists the main contaminants as solid particulate, water and oil. The purity levels for each contaminant are shown separately in tabular form, however for ease of use, here all three contaminants are combined into one easy to use table. Specifying air...
Open the catalog to page 6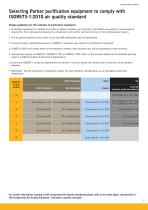
1. Purification equipment is installed to provide air quality, therefore you must first of all identify the quality of compressed air required for the compressed air leaving the compressor room and for each point of use on the compressed air system. 2. The air quality required at each point of use may differ dependent upon the application. 3. Using the quality classifications shown in ISO8573-1 will allow easy selection of purification equipment. 4. ISO8573-1:2010 is the latest edition of the standard, however some facilities may still be operating on older revisions. 5. Specifying air...
Open the catalog to page 7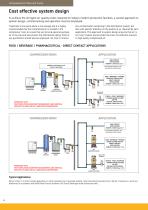
Compressed Air Filters and Dryers Cost effective system design To achieve the stringent air quality levels required for today’s modern production facilities, a careful approach to system design, commissioning and operation must be employed. any contamination remaining in the distribution system, but also with specific attention on the quality of air required by each application. This approach to system design ensures that air is not ‘over treated’ and provides the most cost effective solution to high quality compressed air. Treatment at one point alone is not enough and it is highly...
Open the catalog to page 8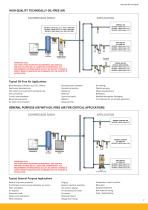
HIGH QUALITY TECHNICALLY OIL-FREE AIR COMPRESSOR ROOM GENERAL USE ISO 8573-1:2010 Class 1:1:2 ISO 8573-1:2010 Class 1:2:2 ISO 8573-1:2010 Class 1:3:2 HIGH QUALITY OIL-FREE AIR ISO 8573-1:2010 Class 1:1:0 ISO 8573-1:2010 Class 1:2:0 ISO 8573-1:2010 Class 1:3:0 PARKER ADSORPTION OR HYBRID DRYER IMPORTANT NOTE: THE PURIFICATION EQUIPMENT REQUIREMENTS ARE IDENTICAL FOR BOTH OIL-FREE AND OIL LUBRICATED COMPRESSORS. THE REQUIREMENTS FOR BREATHABLE QUALITY AIR ARE NOT COVERED IN ISO8573 REFER TO BREATHING AIR STANDARDS FOR THE COUNTRY OF INSTALLATION. HIGH FLOW TETPOR II STERILE AIR FOR CRITICAL...
Open the catalog to page 9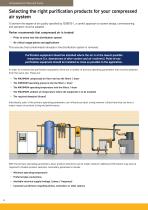
Compressed Air Filters and Dryers Selecting the right purification products for your compressed air system To achieve the degree of air quality specified by ISO8573-1, a careful approach to system design, commissioning and operation must be adopted. Parker recommends that compressed air is treated: • Prior to entry into the distribution system • At critical usage points and applications This ensures that contamination already in the distribution system is removed. Purification equipment should be installed where the air is at the lowest possible temperature (i.e. downstream of after-coolers...
Open the catalog to page 10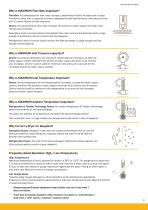
Why is MAXIMUM Flow Rate Important? Filtration: As compressed air flow rates increase, contamination levels increase and a larger filtration surface area is required to ensure adequate filtration performance, low pressure drop and 12 month lifetime of filter elements. Dryers: As compressed air flow rates increase, the amount of water vapour the dryer must remove also increases. Adsorption dryers must be sized on the highest flow rate to ensure the desiccant bed is large enough to provide the correct contact time and dewpoint. Refrigeration dryers must be sized to ensure the heat exchanger...
Open the catalog to page 11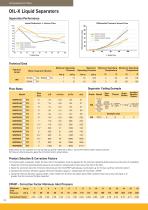
Technical Data Filtration Grade Stated flows are for operation at 7 bar (g) (102 psi g) with reference to 20°C, 1 bar (a), 0% relative water vapour pressure. For flows at other pressures, apply the correction factors shown below. Product Selection & Correction Factors To correctly select a separator model, the flow rate of the separator must be adjusted for the minimum operating (inlet) pressure at the point of installation. 1. Obtain the minimum operating (inlet) pressure and maximum compressed air flow rate at the inlet of the filter. 2. Select the correction factor for minimum inlet...
Open the catalog to page 12All Parker Gas Separation and Filtration Division EMEA catalogs and technical brochures
-
ES2000 Series
4 Pages
-
Compressed Air Filters
2 Pages
-
PNEUDRI
24 Pages
-
OIL-X EVOLUTION
24 Pages
-
Analytical Gas Systems
52 Pages
-
Waveguide Air Pressure Unit
2 Pages
-
Regenerative CBRN Protection
8 Pages
-
Regenerative breathing air
2 Pages
-
Breathing Air Purifiers
8 Pages
Archived catalogs
-
Compressed Air Heaters
2 Pages
-
OIL-X EVOLUTION
4 Pages
-
PNEUDRI DH
4 Pages
-
CARBOFLOW Filter Cartridges
2 Pages
-
PCO2
2 Pages
-
MAXIGAS generic brochure
8 Pages