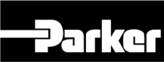
Catalog excerpts
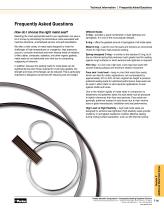
Technical Information Frequently Asked Questions Frequently Asked Questions How do I choose the right metal seal? Selecting the most appropriate seal for your application can save a lot of money by eliminating the tremendous costs associated with machine downtime, unscheduled service, and spill remediation. Different Needs C-ring – provides a good combination of leak tightness and springback. It is one of the most popular designs. E-ring – offers the greatest amount of springback of all metal seals. We offer a wide variety of metal seals designed to meet the challenges of high temperatures or cryogenics, high pressures, vacuum, corrosive chemicals and even intense levels of radiation. Unlike rubber, composite, asbestos, and other organic gaskets, metal seals do not deteriorate over time due to compacting, outgassing or blowouts. Metal O-ring – used for over 50 years and remains an economical choice for high-load, high pressure sealing. In addition, because the seating loads for metal seals can be significantly less than those required for crush-type gaskets, the strength and mass of the flanges can be reduced. This is particularly important to designers concerned with reducing size and weight. Wire ring – is a low cost, high load, crush type seal used with smooth mating surfaces and minimum relative movement. Spring energized C-ring – is similar to the standard C-ring, but it has an internal spring that produces much greater load for sealing against rough surfaces or when extreme leak tightness is required. Face seal / axial seal – keep in mind that metal face seals, which are ideal for static applications, are compressed by approximately 10% to 20% of their original free height to produce preferred sealing loads for optimized performance. Axial seals can be used in either static or semi-dynamic applications to seal against shafts and bores. Due to the relative rigidity of metal seals in comparison to elastomeric and polymeric seals, the axial seals must be produced to tighter tolerances than face seal grooves. Face seals are generally preferred instead of axial seals due to their relative ease of gland manufacture, installation and seal performance. Section F Additional Metal Seal Styles High Load vs High Elasticity – high load metal seals are designed for extreme leak tightness. High elasticity seals provide resiliency or springback needed to maintain effective sealing during mating surface separation, such as with thermal cycling. Parker Hannifin Corporation • Composite Sealing Systems Division Advanced Products Business Unit • 33 Defco Park Road, North Haven, CT 06473 Phone: 203 239 3341 • Fax: 203 239 4409 www
Open the catalog to page 1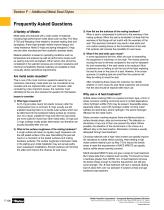
Section F – Additional Metal Seal Styles Frequently Asked Questions A Variety of Metals Metal seals are produced with a wide variety of materials including high performance nickel alloys such as Alloy 718, Alloy X-750 and Waspaloy. Heat treated to increase seating load and springback, these high-strength metals improve fatigue and creep resistance. Metal O-rings and spring energized C-rings are also often manufactured from austenitic stainless steels. Material selection is based on operating conditions such as temperature and pressure as well as performance issues such as seating load and...
Open the catalog to page 2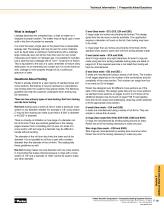
Technical Information What is leakage? Leakage describes the unwanted loss, or leak of matter as it escapes its proper location. The matter may be liquid, gas or even solid in the form of powder for example. It is a fact that every single seal on the planet has a measurable leakage rate. The leakage rate may be zero for some materials, such as liquid water or petroleum hydrocarbons with a relatively large molecular size, but will be more than zero for very small molecules such helium or hydrogen gas. It is possible to manufacture a seal that has a leakage rate of 1x10-11 cc/sec/mm of...
Open the catalog to page 3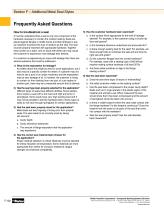
Section F – Additional Metal Seal Styles Frequently Asked Questions How to troubleshoot a seal It must be understood that a seal is only one component of the hardware necessary to contain the medium leaking. Seals are placed against flanges or shafts /bores and that hardware is just as important to prevent the loss of medium as the seal. The seal must be properly matched with appropriate hardware. Together they function as a team, and an issue with either part may cause the customer to experience more leakage than desired. If a customer is experiencing an issue with leakage then there are...
Open the catalog to page 4All Parker Composite Sealing Systems Division catalogs and technical brochures
-
Metal Seal Design Guide
106 Pages
-
Exhaust Manifold Seals
2 Pages
-
O-Seal Division
2 Pages
Archived catalogs
-
Metal Seals
16 Pages
-
Parker O-Rings
6 Pages
-
ParFab Design Guide
40 Pages