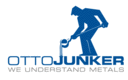
Catalog excerpts
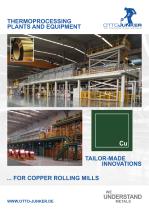
THERMOPROCESSING PLANTS AND EQUIPMENT □TTOJUIMKER WE UNDERSTAND METALS ... FOR COPPER ROLLING MILLS
Open the catalog to page 1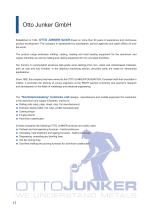
I Otto Junker GmbH Established in 1924, OTTO JUNKER GmbH draws on more than 90 years of experience and continuous product development. The company is represented by subsidiaries, service agencies and sales offices all over the world. The product range embraces melting, casting, heating and heat treating equipment for the aluminium and copper industries as well as melting and casting equipment for iron and steel foundries. Our foundry in Lammersdorf produces high-grade sand castings from iron, nickel and cobalt-based materials, both as cast and fully finished. In the attached machining...
Open the catalog to page 2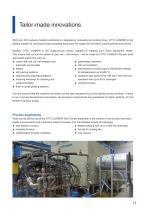
I Tailor-made innovations With over 400 systems installed worldwide on degreasing, annealing and pickling lines, OTTO JUNKER is the leading supplier of continuous strip processing equipment for copper and its alloys, including brass and bronze. Notably, OTTO JUNKER is the single-source This means that not just the system‘s core unit -associated equipment such as: ■ coilers with coil car, belt wrapper and automatic spool loader ■ shears ■ strip joining systems ■ cleaning and degreasing stations ■ brushing machines for cleaning and surface finishing ■ flush or spray pickling systems vendor...
Open the catalog to page 3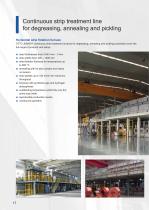
I Continuous strip treatment line for degreasing, annealing and pickling Horizontal strip flotation furnace OTTO JUNKER continuous strip treatment furnaces for degreasing, annealing and pickling processes cover the full range of products and alloys: ■ strip thicknesses from 0.043 mm - 3 mm ■ strip widths from 300 - 1300 mm ■ strip flotation furnaces for temperatures up to 900 °C ■ annealing with no strip contact and nearly no tension ■ strip speeds up to 100 m/min for maximum throughput ■ furnaces with protective gas and hydrogen atmospheres ■ outstanding temperature uniformity over the...
Open the catalog to page 4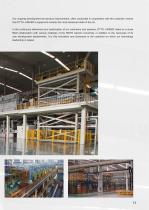
Our ongoing development and product improvement, often conducted in cooperation with the customer, ensure that OTTO JUNKER‘s equipment remains the most advanced state of the art. In the continuous refinement and optimization of our machinery and systems, OTTO JUNKER relies on a close R&D collaboration with various institutes of the RWTH Aachen University, in addition to the resources of its own development departments. It is this innovation and closeness to the customer on which our technology leadership is based.
Open the catalog to page 5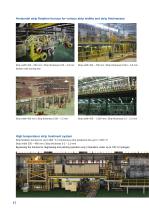
Horizontal strip flotation furnace for various strip widths and strip thicknesses Strip width 300 – 650 mm | Strip thickness 0.05 – 0.9 mm Strip width 300 – 700 mm | Strip thickness 0.043 – 0.8 mm System with turning reel Strip width 400 mm | Strip thickness 0.08 – 1.2 mm Strip width 450 – 1,300 mm | Strip thickness 0.2 – 2.2 mm High temperature strip treatment system Strip flotation furnace for up to 900 °C | Continuous strip treatment line up to 1,000 °C Strip width 250 – 460 mm | Strip thickness 0.2 – 2.0 mm Bypassing the furnace for degreasing and pickling operation only | Operation...
Open the catalog to page 6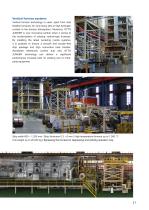
Vertical furnace systems Vertical furnace technology is used, apart from strip flotation furnaces, for very heavy strip or high hydrogen content in the furnace atmosphere. Moreover, OTTO JUNKER is your innovative partner when it comes to the modernization of existing vertical-type furnaces. By installing the latest centering nozzle systems, it is possible to ensure a smooth and scratch-free strip passage and high convective heat transfer. Worldwide references confirm that new OTTO JUNKER technology can deliver a significant performance increase both on existing and on thirdparty equipment....
Open the catalog to page 7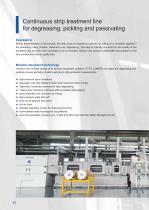
I Continuous strip treatment line for degreasing, pickling and passivating Degreasing Before heat-treatment in the furnace, the strip must be cleaned to remove the rolling oil or emulsion applied in the preceding rolling process. Referred to as “degreasing“, this step is critically important for the quality of the annealed strip as even minor quantities of oil or emulsion residue may produce undesirable discoloration of the strip surface and hence, quality loss. Modular equipment technology Owing to the modular design of its diverse equipment systems, OTTO JUNKER can adapt the degreasing...
Open the catalog to page 8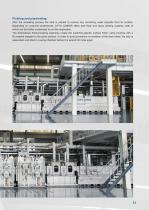
Pickling and passivating After the annealing process the strip is pickled to remove any remaining oxide deposits from its surface. Depending on customer preferences, OTTO JUNKER offers both flush and spray pickling systems, both of which can be further customized to suit the application. The downstream finish-brushing machines create the customer-specific surface finish, using brushes with a fill material adapted to the given product. In order to avoid premature re-oxidation of the bare metal, the strip is passivated and dried in a spray chamber before it is wound into coils again.
Open the catalog to page 9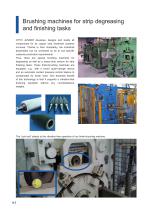
Brushing machines for strip degreasing and finishing tasks OTTO JUNKER develops, designs and builds all components for its copper strip treatment systems in-house. Thanks to their modularity, the individual assemblies can be combined so as to suit specific customer production requirements. Thus, there are special brushing machines for degreasing as well as a heavy-duty version for strip finishing tasks. These finish-brushing machines are equipped, e.g., with a brush quick-change device and an automatic contact pressure control feature to compensate for brush wear. One essential benefit of...
Open the catalog to page 10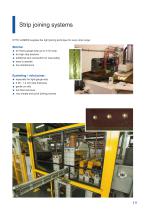
OTTO JUNKER supplies the right joining technique for every strip range: Stitcher ■ for heavy-gauge strip up to 4 mm strip ■ for high strip tensions ■ additional wire connection for dual safety ■ easy to operate ■ low maintenance Eyeletting / rivlet joiner: ■ especially for light-gauge strip ■ 0.05 -1.2 mm strip thickness ■ gentle on rolls ■ low fluid carryover ■ very simple and quick joining process
Open the catalog to page 11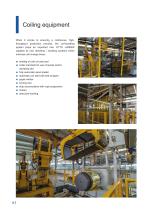
I Coiling equipment When it comes to ensuring a continuous, high-throughput production process, the coil-handling system plays an important role. OTTO JUNKER supplies its own decoiling / recoiling systems which minimize coil change times: ■ loading of coils on jack pad ■ coiler mandrels for use of spools and/or clamping slot ■ fully automatic spool loader ■ automatic coil start with belt wrapper ■ paper winder ■ turning reel ■ strip accumulators with rope suspension ■ shears ■ strip joint tracking
Open the catalog to page 12All OTTO JUNKER GMBH catalogs and technical brochures
-
Image-Broschüre
24 Pages
-
Pouring devices for cast iron
12 Pages