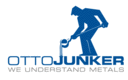
Catalog excerpts
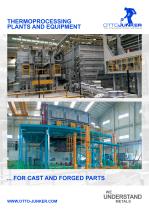
THERMOPROCESSING PLANTS AND EQUIPMENT □TTOJUNKER WE UNDERSTAND METALS FOR CAST AND FORGED PARTS
Open the catalog to page 1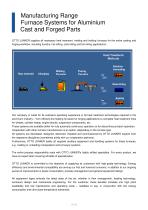
Manufacturing Range Furnace Systems for Aluminium Cast and Forged Parts OTTO JUNKER supplies all necessary heat treatment, melting and holding furnaces for the entire casting and forging workflow, including foundry, hot-rolling, cold-rolling and foil-rolling applications: Our company is noted for its extensive operating experience in all heat treatment technologies required in the aluminium industry – from efficient pre-heating furnaces for forging applications to complete heat treatment lines for wheels, cylinder heads, engine blocks, suspension components, etc. These systems are available...
Open the catalog to page 2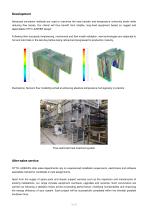
Development Advanced simulation methods are used to maximize the heat transfer and temperature uniformity levels while reducing flow losses. Our clients will thus benefit from reliable, long-lived equipment based on rugged and dependable OTTO JUNKER design. Following their successful engineering, mechanical and flow model validation, new technologies are subjected to hot and cold trials in the test-bay before being refined and progressed to production maturity. Illustrations: Numeric flow modelling aimed at achieving absolute temperature homogeneity in practice Flow-optimized heat treatment...
Open the catalog to page 3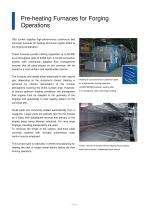
Pre-heating Furnaces for Forging Operations Otto Junker supplies high-performance continuous belt conveyor furnaces for heating aluminium ingots/ billets to the forging temperature. These furnaces provide holding capacities up to 60,000 kg at throughput rates of 8,000 kg/h. A forced convection system with individually adapted flow management ensures that all parts placed on the conveyor will be heated in a most uniform and reproducible manner. The furnaces are heated either electrically or with natural gas, depending on the customer's choice. Heating is Heating of cast automotive suspension...
Open the catalog to page 4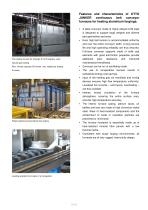
Features and characteristics of OTTO JUNKER continuous belt conveyor furnaces for heating aluminium forgings: A plate conveyor made of highly alloyed CrNi steel is designed to support large weights and diverse part geometries and sizes. Even high belt tension is accommodated uniformly and over the entire conveyor width. A long service life and high operating reliability are thus ensured. Full-area conveyor supports made of solid cast elements with good anti-friction properties provide Pre-heating furnace for forgings, 8 t/h throughput, open natural-gas heating Max. furnace capacity: 60...
Open the catalog to page 5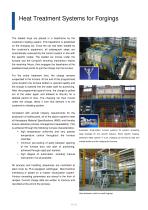
Heat Treatment Systems for Forgings The loaded trays are placed in a baseframe by the customer's loading system. This baseframe is positioned on the charging car. Once the car has been loaded by the customer's equipment, all subsequent steps are automatically executed by the control system in line with the specific recipe. The loaded car moves under the furnace and the furnace's winching mechanism lowers the receiving fixture, then engages the baseframe at the predetermined points to pull the charge into the furnace. For the entire treatment time, the charge remains suspended in the...
Open the catalog to page 6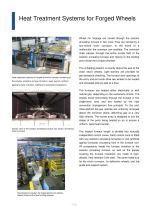
Heat Treatment Systems for Forged Wheels Wheel rim forgings are moved through the solution annealing furnace in two rows. They are carried by a four-strand chain conveyor. In the event of a malfunction the conveyor can oscillate. The conveyor chain passes through the entire nozzle field of the solution annealing furnace and returns to the loading point inside the furnace chamber. The unloading position is exactly above the axis of the chain return wheels. Light barriers are provided for part presence checking. The furnace door openings at Heat treatment systems for forged aluminium wheels,...
Open the catalog to page 7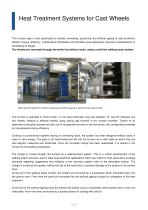
Heat Treatment Systems for Cast Wheels This furnace type is built specifically for solution annealing, quenching and artificial ageing of cast aluminium wheels. Energy efficiency, maintenance-friendliness and flexibility were particularly important considerations in developing its design. The wheels are conveyed through the entire line without racks, using a multi-tier walking beam system. Heat-treatment system for solution annealing and artificial ageing of cast aluminium alloy wheels The furnace is operated in mixed mode, i.e. the wheel diameter may vary between 14“ and 24“ between any...
Open the catalog to page 8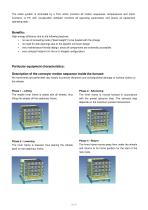
The entire system is controlled by a PLC which monitors all motion sequences, temperatures and motor functions. A PC with visualization software monitors all operating parameters and stores all equipment operating data. Benefits: High energy efficiency due to the following features: ■ no use of annealing racks ("dead weight") to be heated with the charge ■ no need for wall openings due to the specific conveyor design ■ very maintenance-friendly design, since all components are externally accessible ■ very compact footprint (in line or U-shaped configuration) Particular equipment...
Open the catalog to page 9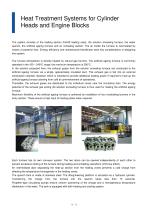
Heat Treatment Systems for Cylinder Heads and Engine Blocks The system consists of the loading section (forklift loading area), the solution annealing furnace, the water quench, the artificial ageing furnace and an unloading section. The air inside the furnace is recirculated by means of powerful fans. Energy efficiency and maintenance-friendliness were key considerations in designing this system. The furnace atmosphere is directly heated by natural gas burners. The artificial ageing furnace is commonly operated in the 160 – 240°C range; the maximum temperature is 300°C. In the solution...
Open the catalog to page 10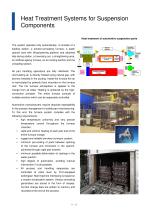
I Heat Treatment Systems for Suspension Components Heat treatment of automotive suspension parts The system operates fully automatically. It consists of a loading station, a solution-annealing furnace, a water quench tank with lifting/lowering platform and attached drip-drying station, a traversing car, a straightening area, an artificial ageing furnace, an air cooling section and the unloading section. All part handling operations are fully robotized. The recirculating air is directly heated using natural gas, with burners installed in the ducting. Inside the furnace the air is...
Open the catalog to page 11All OTTO JUNKER GMBH catalogs and technical brochures
-
Image-Broschüre
24 Pages
-
Pouring devices for cast iron
12 Pages