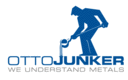
Catalog excerpts
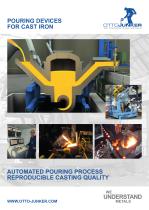
POURiNG DEVICES FOR CAST IRON AUTOMATED POURING PROCESS REPRODUCIBLE CASTING QUALITY
Open the catalog to page 1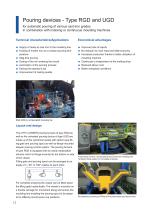
Pouring devices - Type RGD and UGD for automatic pouring of various cast-iron grades in combination with indexing or continuous moulding machines Technical characteristics/Applications Economical advantages Supply of ready-to-cast iron to the moulding line mproved rate of rejects I Holding of molten iron at a constant pouring tem- o residual iron and improved ladle economy N Slag-free pouring Dosing of the iron entering the mould Automation of the pouring process Improvement of casting quality ncreased production thanks to better utilization of I moulding machine asthouse is independent of...
Open the catalog to page 2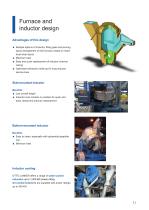
I Furnace and inductor design Advantages of this design ■ Multiple options of inductor, filling gate and pouring spout arrangement on the furnace vessel to match local shop layout ■ Minimum heel ■ Easy and quick replacement of inductor channel casing ■ Optimized refractory make-up for long inductor service lives Side-mounted inductor Benefits: ■ Low overall height ■ Inductor core remains in position for quick and easy vessel and inductor replacement Bottom-mounted inductor Benefits: ■ Easy to clean, especially with spheroidal graphite iron ■ Minimum heel inductor cooling OTTO JUNKER offers...
Open the catalog to page 3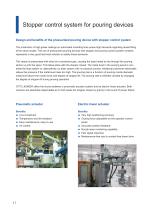
I Stopper control system for pouring devices Design and benefits of the pressurized pouring device with stopper control system The production of high-grade castings on automated moulding lines poses high demands regarding dosed filling of the sand moulds. The use of pressurized pouring devices with stopper and pouring control system certainly represents a very good technical solution to satisfy these demands. The vessel is pressurised with dried air or protective gas, causing the liquid metal to rise through the pouring siphon up into the spout. This takes place with the stopper closed. The...
Open the catalog to page 4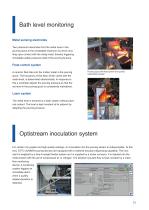
Bath level monitoring Metal sensing electrodes Two policeman electrodes limit the metal level in the pouring spout to the acceptable maximum by short-circuiting upon contact with the rising metal, thereby triggering immediate safety pressure relief of the pouring furnace. Float control system A ceramic float dips into the molten metal in the pouring spout. The buoyancy of this float, which varies with the metal level, is determined electronically. In response to this a controller adjusts the pouring pressure so that the set level in the pouring spout is consistently maintained. Pouring...
Open the catalog to page 5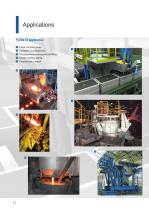
R Flask moulding lines R Flaskless moulding lines ^ Simultaneous pouring and re-filling 4I Anode rodding plants 5I Pouring with tundish
Open the catalog to page 6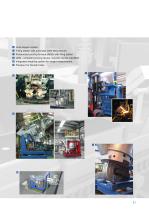
H Dual stopper system 7 Filling station with automatic ladle tilting feature 7 Pressurized pouring furnace (RGD) with filling station 8 UGD - unheated pouring device, inductor can be retrofitted ~9| Integrated weighing system for weight measurement 10 Flexipour for Double Index
Open the catalog to page 7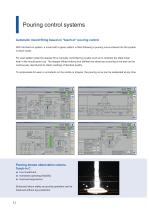
Pouring control systems Automatic mould filling based on "teach-in" pouring control With the teach-in system, a mould with a given pattern is filled following a pouring curve entered into the system in teach mode. For each pattern plate the stopper lift is manually controlled by joystick such as to maintain the ideal metal level in the mould sprue cup. The stopper lifting motions thus defined are stored as a pouring curve and can be continuously reproduced to obtain castings of identical quality. To compensate for wear or accretions on the nozzle or stopper, the pouring curve can be...
Open the catalog to page 8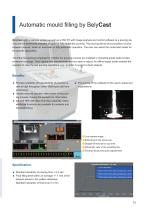
BelyCast adds a camera system as well as a HMI PC with image analysis and control software to a pouring device with an electrically actuated stopper for fully automatic pouring. The pouring device thus provides a choice between manual, 'teach-in' automatic or fully automatic operation. The user can select the mode best suited for his specific application. The Ethernet cameras employed to monitor the pouring process are installed in industrial-grade water-cooled protective housings. They require little maintenance and are easy to adjust. An offline replay mode enables the operator to view...
Open the catalog to page 9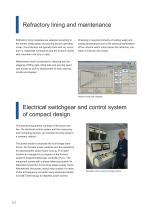
Refractory lining materials are selected according to the molten metal grade and pouring device operating mode. The inductors are typically lined with dry corundum or magnesite compounds and the furnace vessel with corundum mix (dry or cast). Maintenance work is restricted to cleaning and deslagging of filling gate, filling tube and pouring spout with nozzle as well as replacement of worn pouring nozzle and stopper. Checking is required primarily of cooling water and casing temperatures and of the electrical parameters of the inductor which inform about the refractory condition of inductor...
Open the catalog to page 10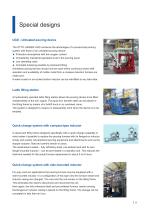
Special designs UGD - Unheated pouring device The OTTO JUNKER UGD combines the advantages of a pressurized pouring system with those of an unheated pouring device: Protective atmosphere with low oxygen content Consistently maintained geostatic level in the pouring spout Complete emptying possible by backward tilting Unheated pouring devices should only be used where continuous three-shift operation and availability of molten metal from a coreless induction furnace are made sure. A water-cooled or air-cooled bottom inductor can be retrofitted at any later date. Ladle filling station A...
Open the catalog to page 11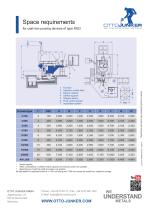
for cast-iron pouring devices of type RGD □TTOJUIMKER WE UNDERSTAND METALS Furnace type (c) otto JUNKER GmbH - o9/2oi6 Illustrations and texts may represent options or extras. 11 Useful capacity 2) Other combinations of useful furnace capacity and inductor power are possible. 3) depending on mould line width and sprue cup position All data relate to a standard travel of +/- 500 mm along and 1,000 mm across the mould line; subject to change. OTTO JUNKER GMBH Jagerhausstr. 22 52152 Simmerath Germany
Open the catalog to page 12All OTTO JUNKER GMBH catalogs and technical brochures
-
Image-Broschüre
24 Pages