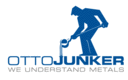
Catalog excerpts
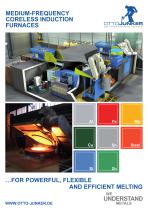
MEDIUM-FREQUENCY CORELESS INDUCTION FURNACES ...FOR POWERFUL, FLEXIBLE AND EFFICIENT MELTING WE UNDERSTAND www.otto-junker.de
Open the catalog to page 1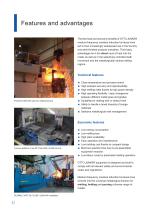
Features and advantages The technical and economic benefits of OTTO JUNKER medium-frequency coreless induction furnaces have led to their increasingly widespread use in the foundry and semi-finished products industries. Their basic advantages lie in the direct input of heat into the metal, as well as in the selectively controlled bath movement and the metallurgically neutral melting regime. Technical features < Close temperature and process control < High analysis accuracy and reproducibility < High melting rates thanks to high power density < High operating flexibility / easy changeover...
Open the catalog to page 2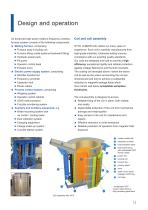
An advanced high-power medium-frequency coreless furnace system consists of the following components: ■ Melting furnace, comprising ► Furnace body including coil ► Furnace tilting cradle (optional backward tilting) ► Hydraulic power pack ► Pit guard ► Operator control desk ► Exhaust hood ■ Electric power supply system, comprising ► Rectifier transformer ► Frequency converter ► Capacitor rack ► Power cables ■ Process control system, comprising ► Weighing system ► Operator control cabinet ► JOKS melt processor ► Crucible monitoring system ■ Auxiliary and ancillary equipment, e.g. ► Water...
Open the catalog to page 3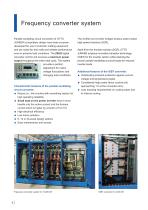
Frequency converter system Parallel oscillating circuit converters of OTTO JUNKER‘s proprietary design have been purposedeveloped for use in induction melting equipment and are noted for their safe and reliable performance even in extreme load conditions. The ZEUS digital converter control unit ensures a maximum power output throughout the entire heat cycle. The system provides a perfect adjustment for mains voltage fluctuations and changing load conditions. Characteristic features of the parallel oscillating circuit converter: < Robust d.c. link circuitry with smoothing reactor for high...
Open the catalog to page 4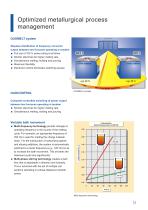
Optimized metallurgical process management DUOMELT system Stepless distribution of frequency converter output between two furnaces operating in tandem < Full use of 100 % power rating at all times < Shorter idle times for higher melting rate < Simultaneous melting, holding and pouring < Maximum flexibility < Electronic control eliminates switching pauses DUOMELT principle Computer-controlled switching of power output between two furnaces operating in tandem < Shorter idle times for higher melting rate < Simultaneous melting, holding and pouring Variable bath movement < Multi-frequency...
Open the catalog to page 5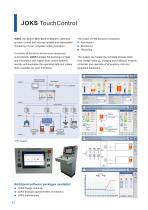
JOKS, the Junker Ofen KontroN System, optimizes process control and ensures reliable and dependable monitoring of your complete melting operation. It controls all functions and process sequences automatically. JOKS handles the exchange of data and information with higher-level control systems, records and evaluates the operating data and makes them available via open interfaces. The scope of HMI functions comprises X Automation X Monitoring X Recording The system can handle the complete process chain from charge make-up, charging and melting to analysis correction and operation of all...
Open the catalog to page 6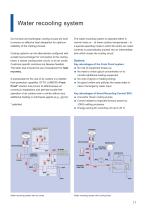
Water recooling system Our furnace and switchgear cooling circuits are built to ensure an effective heat dissipation for optimum reliability of the melting process. Cooling systems can be alternatively configured with a plate heat exchanger for connection to the cooling tower, a closed cooling tower circuit, or an air cooler. Customer-specific solutions are likewise feasible. The latter also include the use of equipment for heat recovery. A prerequisite for the use of air coolers is a reliable frost protection capability. OTTO JUNKER‘s Frost Proof* solution has proven its effectiveness on...
Open the catalog to page 7
Exhaust hood Weighing system Hydraulic power pack Control stand with operator desk Frequency converter (DUOMELT) Capacitor rack Transformer Air cooler Charging machine Water recooling system Dust collection system
Open the catalog to page 9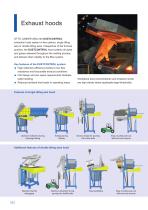
Exhaust hoods OTTO JUNKER offers the DUSTCONTROL extraction hood system in two options: single tilting axis or double tilting axes. Irrespective of the furnace position, the DUSTCONTROL hood collects all dusts and gases released throughout the melting process and delivers them reliably to the filter system. Key features of the DUSTCONTROL system: < High collection efficiency thanks to low flow resistance and favourable exhaust conditions < Flat design and low space requirements facilitate ladle handling < Reduced ambient heat loads in operating areas Workplace dust concentrations and...
Open the catalog to page 10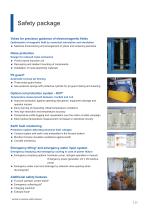
Yokes for precision guidance of electromagnetic fields Optimization of magnetic field by numerical calculation and simulation ■ Selective dimensioning and arrangement of yokes and screening elements Noise protection Design for reduced noise emissions ■ Firmly braced induction coil ■ Decoupling and resilient mounting of components ■ Installation of noise-absorbing materials Pit guard* Automatic furnace pit fencing ■ Three-sided guard frame ■ Gas pressure springs with protective cylinder for pit guard raising and lowering Optical coil protection system - OCP* Temperature measurement between...
Open the catalog to page 11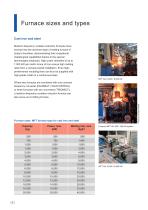
I Furnace sizes and types Cast iron and steel Medium-frequency coreless induction furnaces have evolved into the dominant type of melting furnace in today‘s foundries, demonstrating their exceptional metallurgical capabilities thanks to the special technologies employed. High power densities of up to 1,000 kW per metric tonne of iron ensure high melting rates from a compact-sized installation. Even high-performance moulding lines can thus be supplied with high-grade metal on a continuous basis. Where two furnaces are combined with one common frequency converter (DUOMELT / DUOCONTROL) or...
Open the catalog to page 12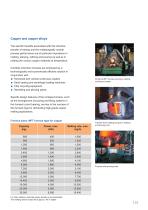
The specific benefits associated with the inductive transfer of energy and the metallurgical^ neutral process performance are of particular importance in melting, alloying, refining and pouring as well as in holding the various copper materials at temperature. Coreless induction furnaces are employed as a technologically and economically efficient solution in conjunction with ■ Horizontal and vertical continuous casters ■ Sand casting and centrifugal casting machines ■ Chip recycling equipment ■ Remelting and alloying plants Specific design features of the coreless furnace, such as the...
Open the catalog to page 13All OTTO JUNKER GMBH catalogs and technical brochures
-
Image-Broschüre
24 Pages
-
Pouring devices for cast iron
12 Pages