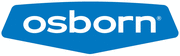

Catalog excerpts
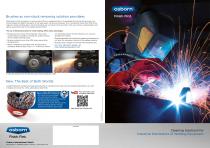
Brushes as non-stock removing solution providers Machining is often necessary to remove debris from a welded surface. It is accepted that during this process noncontaminated and debris-free parts of the weld seam will also be removed. This is sometimes more than 30% of the material. Unlike grinding discs, technical brushes are non-stock removing tools. They can remove contamination and debris, leaving the rest of the welded surface intact. The use of technical brushes for weld cleaning offers many advantages: • Brushes are non-stock removing tools. They clean contanimation and debris, leaving the original surface of the welded material intact. • Brushes produce more than 95% fewer sparks than grinding discs. • When compared to grinding tools, brushes are on average 6-8 dB (A) less noisy. A +/- 3 dB (A) increase (or decrease) means that the intensity of a sound is doubled (or halved). • Brushes generate less heat during usage and therefore do not alter the molecular surface of the welded material. • Brushes have a longer service-life than grinding tools. • For more information please visit: http://weldcleaning.osborn.com A brush (left) produces more than 95% fewer sparks than a grinding disc (right). New: The Best of Both Worlds Longlife filaments combine the high performance of a knotted cup brush with the material friendliness of a soft, crimped wire brush for a fine, satinised surface finish. • Min 5-times less wire breakage and wear through less flaring • Material friendly and non-stock removing • For cleaning and descaling jobs • Available in D 60, 75, 80, 100 and 125 mm • Safety-Certified by German TÜV-Süd (production monitored, type tested) Art.No. 6255332031 Printed 09/14. All items subject to change without notice. More information and a product video here: Your dealer: Cleaning Solutions for Industrial Distributors of Welding Equipment Osborn International GmbH Ringstrasse 10 • 35099 Burgwald • Germany • www.osborn.com
Open the catalog to page 1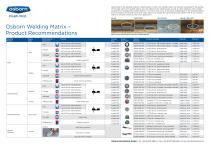
Depending on the welding method, contamination or other non-metallic debris can become embedded in the surface of the weld seam. Non-metallic debris may not adhere to the welding seam as well as other materials. If the welded component is subsequently coated, defects or corrosion may occur at this point. Independent of the welding method and the position of the layer (root, fill or cap), Osborn can supply the right cleaning tool. Please refer to our welding matrix to find the correct tool for every application. Osborn Welding Matrix – Product Recommendations Welding Method Debris Type Weld...
Open the catalog to page 2All Osborn GmbH catalogs and technical brochures
-
AS 46 T INOX Freecut
1 Pages
-
CS 24 R
1 Pages
-
AS 36 S IN
1 Pages
-
AS 36 T
1 Pages
-
AS 24 R Bahn
1 Pages
-
IDLER ROLLER & RAIL SOLUTIONS
47 Pages
-
Osborn Roller Technologies
36 Pages
-
Osborn Topseller
15 Pages
-
Osborn Catalog 2020/21
320 Pages
-
TOOLS FOR X-LOCK
24 Pages
-
Cordless Power Tool Accessories
16 Pages
-
Oil- and Gas Industry
48 Pages
-
Osborn Polishing Catalogue
10 Pages
-
Osborn Load Runners
92 Pages
-
Osborn TurbFly (SnowProtec)
7 Pages
-
Osborn Broomate
2 Pages
-
Osborn Woodworking Technology
24 Pages
Archived catalogs
-
Osborn ECO
24 Pages
-
Osborn (USA) Welder's Choice
15 Pages
-
OSBORN EZ-Flex catalogue
2 Pages
-
OSBORN Novofil catalogue
18 Pages
-
OSBORN MultiStrip catalogue
14 Pages
-
OSBORN TOP catalogue
44 Pages