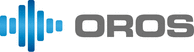
Catalog excerpts
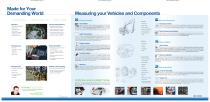
Verso (Intérieur) page 2 Verso (Intérieur) page 4 Made for Your Demanding World 1- Improve Efciency Measuring your Vehicles and Components 2- Minimize Testing Costs Improve testing efciency > Integrated & automated test process and report generation > Project management and data sharing: ASAM ODS compliant > Sound power > Continuously Variable Transmission (CVT) > Universal and multiple sensor’s types: microphones, acceleration, temperature, strain, pressure… Rotating Analysis Gear Analysis Signatures coming from gear box vibrations have high frequency content. A rst step is to analyze them using the standard FFT analysis. One can get further with tools such as cepstrum, kurtosis and harmonic markers provided by the OROS FFT-Diagnostics tool. The Constant Band Tracking function is also especially useful for looking at order proles during run-ups and run-downs of the transmission train. Hybrid Transmission Classical or hybrid transmissions are some of the major source of vibration in the drive train. Nowadays, Continuously Variable Transmissions (CVT) integrate a exible transmission belt that allows an innite number of transmission ratios. In order to carry order tracking, phase reference and rotating speed determination, the transmission ratio is based on a mathematical formula based on 2 tachometer’s inputs. Engines Analysis In-Vehicule Test > Portable and rugged systems for in-vehicle tests > Component in-vehicle integration > PC free operation: full signal recording for ofce processing archiving > Cabin noise > Interior NVH Verso (Intérieur) page 5 > Real-time results for direct live monitoring > Get all data through conditioners and CAN Bus The objective is the engine performance optimization and faults detections. For example, injection delay, valves faults, can be identied with EngineDiag. This software module integrates the machine mechanical properties: number of cylinders, ring order and timing diagram to provide pertinent results. Time signal, overall levels, cylinders phase alignment as well as angle-frequency representation on the machine cycle are efcient results for R&D and prototype validation. Vehicles > Automotive > Motorcycles > Trucks & Buses Structural Dynamics Damping & Isolation Absorbing and damping mounts are the components through which the vibration energy is transmitted between the engine and the rest of the vehicle: their properties, dimensions and positions should be determined with care. The techniques used are cross spectrum, transfer functions, damping, as well as ODS (Operating Deection Shape). > Earth Moving Vehicles > Industrial Vehicles > Leisure Vehicles > Trains Engines > Downsizing > Hybrid > Timing > Crankshaft > Diesel Modal & Experimental Analysis Modal Analysis is one of the key steps when testing vehicles and parts: it determines their structural characteristics and so, denes how they reacts to operating excitations. Shaker or impact hammer excitations can be used to capture the experimental datasets: the nal stage is the actual OROS Modal analysis. Noise Analysis Sound Power Sound power is a key acoustical value to be determined for vehicles and various automotive components such as alternators and motors. For qualication and production testing, the most common procedure uses microphones and is based on sound pressure level acquisition (ISO 374x) in a free or diffuse sound eld. For portable applications, sound intensity is preferably used to determine sound power. It is based upon measurements at discrete points (ISO 9614-1) or via a surface scanning (ISO 9614-2). In this case, a sound intensity probe is used. Torsional Analysis The OROS torsional module corresponds to a frequency to voltage converter that transforms a pulse train signal into a varying rotating speed value. This is a common cause for vibration in engines. A typical display is the varying angular velocity prole versus time. The rotating speed value signal can be analyzed: torsional modes can be deduced. Provided signals can also be processed with the Synchronous Order Analysis (SOA) module to give order tracking proles. Source Localization Components > Hybrid Drivetrains > Turbochargers During the NVH process, the acoustical specialist is often driven by improving the understanding and control of his product noise emission. Standard 1/3 octave analysis can be used as a rst step. The sound intensity acquisition at discrete points allows going one step further, drawing a colored noise map and acoustic iso lines. Hot spots and their corresponding frequencies will help the analyst to draw conclusions on how to reduce or control better the noise emission. Balancing Production Test Optimize costs and quality > Test bench maintenance > Automate production test process > Versatile tool box for all noise and vibration troubleshooting and diagnostics applications Balancing is a common application in particular for crankshaft that is often carried out during production. The OROS Balancing module enables to balance quickly and accurately. The synchronous order analysis can be controlled by NVDrive for integration into automatic balancing machines. > Steerings > Brakes > Alternators > Compressors > Electric Motors > Exhausts > Test bench integration with NVDrive On-Site Measurements & Applied Trainings Experts from OROS come on-site for applied trainings. They will help you using your OROS system. They can provide assistance in your measurement. They are also able to recommend optimization in your measurement process depending on your application and eld requirements. They trust OROS > “For in-vehicle tests, I really appreciate flexibility and portability of the OROS analyzers.” Noise and Vibration technician, Road test validation division. > Gear boxes > Continuous Variable Transmissions (CVT) Data Acquisition In-Vehicle Recording The different components installed in a vehicle are tested on the road to validate their integration in the vehicle (brakes, tires, turbocharger etc …). It requires a portable, rugged and easy recording system with a CAN Bus interface. PC free recording is especially useful for the toughest conditions (D-rec). Fatigue Test Drive train and transmission components are submitted to high static and dynamic stress that creates fatigue in the long term. During the prototype development and validation process, strain gauges are used to determine these parameters. They are also determined in combination with other parameters such as acceleration or rotating speed: having a way such as XPods, plug and play signal conditioning, to do that is essential.
Open the catalog to page 1All OROS catalogs and technical brochures
-
TPA TRANSFER PATH ANALYSIS
2 Pages
-
product catalog
17 Pages