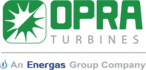
Catalog excerpts
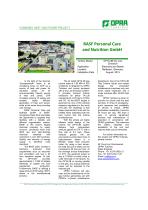
COMBINED HEAT AND POWER PROJECT BASF Personal Care and Nutrition GmbH Turbine Model Application Location Installation Date In the light of the German “Energiewende” there is an increasing focus on CHP as a source of heat and power for industrial plants. As an environmentally friendly source of heat and power, CHP increases security of supply and enables highly efficient generation of heat and power, while at the same time providing cost savings. BASF Personal Care and Nutrition GmbH, or BASF, recognizes these facts and takes the opportunity to upgrade their facilities with a reliable and efficient cogeneration system. BASF is the world’s largest chemical company by yearly turnover, producing more than 9000 raw and semi-finished chemical materials with customers in over 200 countries. Quality and security of energy supply is therefore most important. The BASF plant, located in Germany, produces food supplements such as enzymes and emulsifiers and has a 24 hour operation regime. At site, the OP16-3B provides approximately 1.7 MW of reliable electricity to sustain the food supplement production. Furthermore, BASF is utilizing a large amount of 60 bar(g), 450°C steam in the manufacturing process. The all radial OP16-3B gas turbine rated at 1.85 MW in ISO conditions is designed by OPRA Turbines and comes equipped with a Dry Low Emission system. It provides full-load turbine emissions far below TA-Luft requirements at 25 ppmv of NOx and CO. As the BASF project is governed by one of the strictest emission regulations in the world (TA-Luft), the challenge is that these requirements must also be fulfilled when operating both the duct burner and the turbine simultaneously. With the simple yet highly efficient radial design of the turbine, the OP16-3B system delivers high temperature exhaust gasses at 575 ⁰C with a flow rate of 8.4 kg/s. These exhaust gasses will be recovered by producing 6 tons of high-pressure steam in a Bertsch waste heat recovery boiler. By using a duct burner, the total amount of steam can be increased to 20 tons per hour. At the average annual temperature of 10°C, the electrical output at site is 1700kW of which most is used internally in the factory. As the OP16-3B is running parallel to the grid, any surplus electrical power will be exported to the national grid. OPRA Turbines will also carry out the maintenance on the gas turbine generating set with OPRA’s in-house maintenance OP16-3B Dry Low Emission Electricity and Steam Illertissen, Germany. August, 2015 department. Due to the OP16-3B Gas Turbine robust and simple design the scheduled maintenance comprises only one minor yearly inspection and a major overhaul after 44.000 fired hours. OPRA Turbines is driven to provide our clients with the best services. In times of emergency, quick response and availability of service is critical. OPRA guarantees availability of service 24 hours per day, 365 days a year. A service agreement ensures that maintenance is executed in accordance with OPRA guidelines. This improves the safety, reliability and availability of the unit and reduces total cost of ownership. For further information on this project and OPRA Turbines, please contact: Mr. Ruud van Groenewoud OPRA Turbines Sales Engineer Phone: +31 (0)74-2452121 Fax: +31 (0)74 245 21 20 Email: rvg@opra.nl www.opraturbines.com OPRA Turbines BV, Opaalstraat 60, 7554 TS, Hengelo OV, The Netherlands, Phone +31 (0)74 245 2121, Fax +31 (0)74 245 2120. www.opratur
Open the catalog to page 1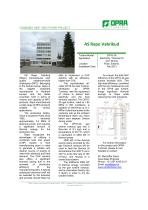
COMBINED HEAT AND POWER PROJECT AS Repo Vabrikud Turbine Model Application Location Installation Date AS Repo Vabrikud (Repo) manufactures high quality melamine-faced chipboards (MFC). Belonging to the Sorbes Group, Repo is the biggest chipboard manufacturer in Northern Europe and the Baltic Countries, both in terms of volume and capacity of MFC products. Repo manufactures a wide range of MFC products suitable for various applications. The production facility, which is located in Püssi since 1992, demands approximately 3.5 MWe of electrical power and requires a significant amount of thermal...
Open the catalog to page 2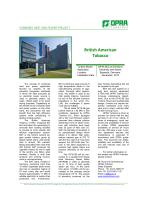
COMBINED HEAT AND POWER PROJECT British American Tobacco Turbine Model Application Location Installation Date The concept of combined heat and power application favored by majority of the industrial companies worldwide in which the heat produced by an electrical power source is used to generate steam, hot water, chilled water or for direct drying purposes. Capitalizing on the benefit of the combined heat and power system, on the other hand, the consumers will also benefit from the high efficiency system while contributing to greener energy system. The British American Tobacco, or BAT,...
Open the catalog to page 3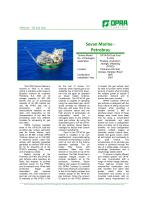
Sevan Marine Petrobras Turbine Model No. of Packages Application Location Certification Installation Year The FPSO Sevan Marine is moored in 1000 m of water, where it operates under lease to Brazilian national oil company Petrobras S.A. With an oil storage capacity of 300 000 barrels and an oil processing capacity of 30 000 barrels per day, the FPSO also has a processing plant for hydrocarbons installed on the deck, and depending on the characteristics of the field the processing plant has different modules for processing oil, gas and water. OPRA Turbines supplied three of the OP16-3A...
Open the catalog to page 4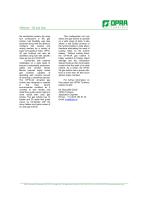
Offshore – Oil and Gas the combustion system. By using four combustors in the gas turbine, fuel flexibility was also achieved along with the ability to configure fuel nozzles and mixing swirlers for a variety of liquid and gaseous fuels. OP163A gas turbines can also be operated using fuel with calorific 3 value as low as 215 BTU/ft . Confronted with extreme challenges on a daily basis to ensure a sustainable production, safety and comfort, Sevan Marine requires highly robust gas turbines capable of operating with minimal amount of servicing or downtime periods. The OP16-3A all-radial gas...
Open the catalog to page 5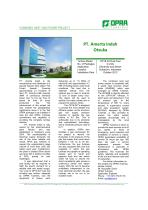
COMBINED HEAT AND POWER PROJECT PT. Amerta Indah Otsuka Turbine Model No. of Packages Application Location Installation Date PT. Amerta Indah is the manufacturer and distributor of a popular isotonic drink called ‘The Pocari Sweats’. Covering approximately 21 hectares of land, PT. Amerta Indah requires 3MW of continuous electrical power and 12 ton per hour of steam for their 24 hours production line. The achievement of this project not only marked the geographical significance since it is the first OPRA package to be installed in Asia but also OPRA Turbines commitment and capability in...
Open the catalog to page 6All OPRA Turbines catalogs and technical brochures
-
OP16 Datasheet (Imperial)
1 Pages
-
OP16 Datasheet (Metric)
1 Pages
-
OPRA Brochure (English)
8 Pages