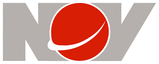
Group: Mono, Moyno, Chemineer, Kenics, Prochem, Greerco

Catalog excerpts
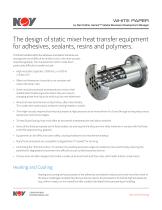
WHITE PAPER by Neil Cathie, Kenics™ Global Business Development Manager The design of static mixer heat transfer equipment for adhesives, sealants, resins and polymers. The fluids handled within the adhesives and sealant industries are amongst the most difficult to handle of any in the main process industries globally. The characteristics which make them particularly difficult to handle include: • High viscosities (typically 1-2000 Pa.s, or 1000 to 2 million cP). • Often non-Newtonian (viscosity is not constant and varies with shear rate). • Some must be processed at temperatures close to their solidification/hardening points where they are close to changing phase from liquid to solid (e.g. hot melt adhesives). • Almost all have low thermal conductivities, often intentionally. This makes them particularly resistant to being heated or cooled. • Their high viscosity requires that they be pumped at high pressures to be moved from A to B and through all required process equipment and process stages. • To keep fluids flowing, they must often be processed at temperatures well above ambient. • Some of the fluids processed are for food related use and require the alloy and non-alloy materials in contact with the fluids to be FDA approved (e.g. gaskets). • Equipment can be difficult to clean safely, causing shutdowns and maintenance delays. • Many fluids processed are susceptible to degradation if “cooked” for too long. • Controlling the “thermal history” of a product by avoiding excessive ranges of residence times (and thereby reducing the potential for degradation) becomes more difficult as soon as flow becomes laminar. • Process lines are often designed to handle a variety of process fluids and flow rates, which adds further complication. Heating and Cooling Heating and cooling are key processes in the adhesives and sealants industry and ones into which most of the above challenges inevitably fall. Many products need to be processed or formed at high temperatures (e.g., within a reactor or mix vessel) but later cooled to facilitate further processing or handling.
Open the catalog to page 1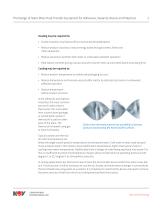
The Design of Static Mixer Heat Transfer Equipment for Adhesives, Sealants, Resins and Polymers Heating may be required to: • Enable solvents to be flashed off and recovered (devolatilization) • Reduce product viscosity to reduce energy losses through screens, filters and other equipment • Reduce viscosity to optimize belt cooler or underwater pelletizer operation • Heat reactor contents during a pump around to shorten heat up and overall batch processing time Cooling may be required to: • Reduce product temperature to enable safe packaging to occur • Reduce temperature and increase...
Open the catalog to page 2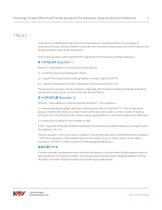
The Design of Static Mixer Heat Transfer Equipment for Adhesives, Sealants, Resins and Polymers Theory To be able to make decisions about how to solve heating or cooling problems, it is necessary to understand the basic theory of indirect conductive and convective heat transfer and how it relates to the design of indirect heat transfer equipment. The first key equation, which identifies the magnitude of the heating or cooling challenge is: Q = m*Cp*ΔT (Equation 1) Where Q = heat addition or removal required (W, Btu/hr) m = mass flow of process fluid (kg/sec, lbs/hr) Cp = specific heat of...
Open the catalog to page 3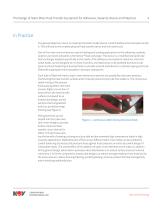
The Design of Static Mixer Heat Transfer Equipment for Adhesives, Sealants, Resins and Polymers In Practice The general objective now is to maximize the heat transfer device U and therefore minimize heat transfer A. This will lead to the smallest physical heat transfer device and the lowest cost. One of the most common devices used in heating and cooling applications in the adhesives, sealants, polymer and resins industries is the Kenics™ heat exchanger. This device is a modified shell and tube heat exchanger adapted specifically to the needs of the adhesives and sealants industries. Inlet...
Open the catalog to page 4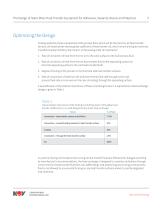
The Design of Static Mixer Heat Transfer Equipment for Adhesives, Sealants, Resins and Polymers Optimizing the Design Putting aside the physical properties of the process fluid, which will be the same for all heat transfer devices, the heat transfer device global coefficient of heat transfer (U), which we are aiming to maximize, is predominantly limited by four factors, in decreasing order of importance: 1. Rate of convection of heat from the hot (or to the cold) surface to the bulk process fluid. 2. Rate of convection of heat from the hot heat transfer fluid to the separating surface (or...
Open the catalog to page 5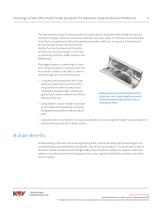
The Design of Static Mixer Heat Transfer Equipment for Adhesives, Sealants, Resins and Polymers The heat transfer surface thickness would normally be as thin as possible after taking into account mechanical design needs such as pressure retention and cyclic loads. This process ensures that this factor does not significantly affect the global heat transfer coefficient. Convection of heat from/to the heat transfer surface to/from the heat transfer fluid can be maximized; therefore its influence on overall design is minimized by optimizing fluid flow, baffle positions and baffle design. The...
Open the catalog to page 6All NOV Inc. catalogs and technical brochures
-
Chemineer™ Small Mixer
6 Pages
-
CD-6
2 Pages
-
BT-6
2 Pages
-
HE-3
2 Pages
-
20 HT/GT
12 Pages
-
Swing Check Valve Data Sheet
4 Pages
-
EZstrip Hose Pump Brochure
9 Pages
-
Kenics HEV Bulletin
2 Pages
-
KMX-V Static Mixer Bulletin
1 Pages
-
UltraTab Bulletin
2 Pages
-
Kenics WVM Bulletin
2 Pages
-
EZstrip™ Transfer Pump
2 Pages
-
Merlin range
1 Pages
-
Dosing/Metering
2 Pages
-
Mixing Technologies Overview
12 Pages
-
Heat Exchangers
4 Pages
-
Greerco Homogenizer Bulletin
8 Pages
-
KM Mixers
2 Pages
-
KMX-V Mixers
1 Pages
-
ChemSeal
2 Pages
-
Impellers Bulletin
6 Pages
-
Biopharm Mixers
8 Pages
-
Portable Mixers
2 Pages
-
MR Mixers
12 Pages
-
20 HT Agitator range
12 Pages
-
Maxflo WSE
1 Pages
-
RL-3
2 Pages
-
Kenics UltraTab Static Mixer
2 Pages
-
Chemineer Line Card
2 Pages
-
Pipeline Mixers
8 Pages
-
Kenics Sanitary Mixer
2 Pages
-
Static Mixing Technology
12 Pages
-
HT Turbine Agitators Bulletin
10 Pages
-
Model 20 HT / GT
12 Pages
-
XE-3
1 Pages
-
Side-Entering Agitators Bulletin
10 Pages
-
HS Agitators
10 Pages
-
Prochem MD Series Mixers
10 Pages
-
QED Agitators
2 Pages
-
Mining Applications
6 Pages
-
HT & HTM
4 Pages
-
WVM Mixers
2 Pages
-
HEV Static Mixer Bulletin
2 Pages
-
SC-3
2 Pages
-
IBC Mixers Bulletin
4 Pages
-
IBC Mixers
4 Pages
Archived catalogs
-
Impellers Bulletin
2 Pages
-
HT
4 Pages
-
Clean Sweep Bulletin
2 Pages
-
RBTNS Biotech Mixer Bulletin
2 Pages
-
BTNS Biotech Mixer Bulletin
2 Pages
-
Biotechnology / Pharmaceutical
8 Pages
-
Model 10 MR Agitators
6 Pages
-
Capabilities Brochure - English
12 Pages
-
portable mixer
2 Pages
-
Waste Water brochure
6 Pages
-
In-line high shear mixer
4 Pages
-
Kenics Static Mixer
12 Pages
-
DT agitator range
2 Pages