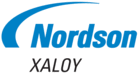
Catalog excerpts
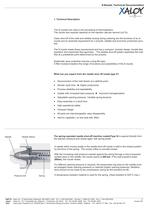
1. Technical Description The S-nozzles are used in the processing of thermoplastics. The nozzle size required depends on the injection rate per second (cm > 3 /s). Clean shut-off of the melt and reliable closing during metering are the functions of an A- nozzle and an essential requirement for a smooth, reliable and economic production proc-ess. The S-nozzle meets these requirements and has a compact, modular design, trouble-free operation and maximized flow geometry. The reliable shut-off system separates the melt flow at a predefined point determined by the process. Systematic wear...
Open the catalog to page 2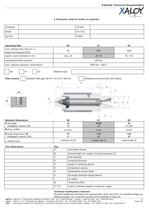
2. Dimension sheet for orders or enquiries Operating data Company Contact Street Tel / Fax Zip/City E-Mail S0 S1 S2 max. injection flow rate cm > 3 / s based on Polystyrol (PS) 45 500 1600 approx. worm diameter in mm max. 20 20 -50 50 -120 opening and back pressure 200 bar max. injection pressure / temperature 2000 bar / 350C A0 A1 A2 Machine type Filter module Standard filter gap A0=0.3 / A1=0.5 / A2=0.8 Abrasion protection (over 30% fillers) Standard dimensions S0 S1 S2 K tip lenght installation wrench 15 18/28 30 (AF) 19 24 41 (36) M max. orofice 2,5 mm 5 mm 8 mm N body lenght (excl. B )...
Open the catalog to page 3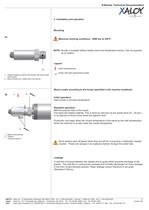
3. Installation and operation Mounting A) Maximum working conditions : 2000 bar at 350C NOTE: Nozzle is supplied without heater band and temperature sensor. Can be supplied as an Option. Legend > match temperatures smear with high temperature paste 1. Grease sealing surfaces and threads with high tempe-rature paste 2. Mount Nozzle incl. heater band and sensor 1. Match temperatures 2. Tighten (torques: page 5) Mount nozzle according to the torque specified in the machine handbook. Initial operation: B) Repeated operation: Heat nozzle to process temperature. Melt the polymer fully in the...
Open the catalog to page 4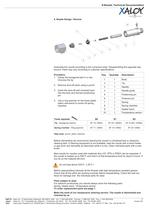
4. Nozzle Design / Service Assemble the nozzle according to the numerical order. Disassembling the opposite way around. Parts may vary according to customer specifications. Procedure 1. Clamp the hexagonal part in a vice. Unscrew the tip 2. Remove shut-off parts using a punch 3. Insert the shut-off part reversed back into the body and reinsert positioning pin 4. Use a ring spanner on the three stabili-sation extrusions to screw off spring chamber Before dismantling we recommend cleaning the nozzle in a fluidized-bed or ultrasonic cleaning tank. If cleaning equipment is not available, heat...
Open the catalog to page 5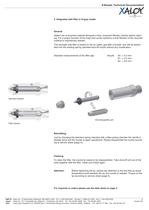
5. Integrated melt filter in S-type nozzle General Added use of recycled material demands a final, important filtration directly before inject-ing. For a proper function of the mold (hot runner systems) a final filtration of the recycled material is imperatively needed. The herzog melt filter is based on the so called ΄gap filter principle and will be assem-bled into the existing spring operated shut-off nozzle without any modification. Standard measurements of the filter gap: Nozzle S0 0.3 mm S1 0.5 mm S2 0.8 mm > Standard System Filter System Interchangeable part Retrofitting Just by...
Open the catalog to page 6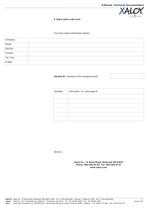
NAFTA Xaloy Inc. 72 Stard Road, Seabrook, NH 03874, USA Tel: +1 603 929 8246 Toll free: +1 866 533 1092 Fax: +1 603 929 8332 Japan 7 Version 00 Xaloy Inc. 74-1 Yamashita-cho, Naka-Ku - Yokohama, 231-0023 Tel: +81-45-661-3508 Fax: +81-45-661-3507 Asia Xaloy Asia (Thailand) Ltd. 700/446 Moo 7, Donhuaroh| Muang Chonburi, Chonburi 20000, Thailand Tel: +66 38 717 084 Fax: +66 38 454 377 >
Open the catalog to page 7All Nordson Xaloy catalogs and technical brochures
-
Custom Injection Units
1 Pages
-
FTR Valves
2 Pages
-
Auto-Shut Valves
2 Pages
-
Injection Molding Screws
2 Pages
-
Pulsar® Mixing Screw
1 Pages
-
Z-Mixer? Screw
1 Pages
-
Fusion™ II screw
2 Pages
-
SmartHeat? Coating
4 Pages
-
Injection Barrels
1 Pages
-
Mini Jet Cleaner
2 Pages
-
JCP 1724 Jet Cleaner
2 Pages
-
WRP-35s/36s Pelletizer
2 Pages
-
WRP-12i In-Line Pelletizer
2 Pages
-
Static Mixers
2 Pages
-
EquaTherm® Rolls
2 Pages
-
Durashell
2 Pages
-
Standard extrusion pumps
2 Pages
-
Extrusion Barrels
1 Pages
-
X8000
1 Pages
-
Extrusions screws
2 Pages
-
Elastomer Nozzle
7 Pages
-
BHP Shutoff Nozzle
11 Pages
-
Hydraulic changers
2 Pages
-
Front-end components.
3 Pages
-
Stratablend® II
1 Pages
-
Efficient™ Extrusion Screw
1 Pages
-
Fusion™ Screw
2 Pages
-
Xaloy Extrusion equipment
1 Pages
Archived catalogs
-
Gross® Equatherm® Rolls
1 Pages
-
Nano™ Mixer
1 Pages