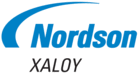
Catalog excerpts
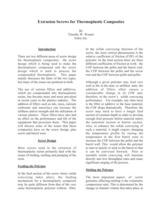
ByTimothy W. WomerXaloy Inc. Introduction There are two different areas of screw designfor thermoplastic composites: the screwdesign which is being used to make thethermoplastic compound and the screwdesign which is used to process thecompounded thermoplastic. This papermainly discusses the latter of the two types,but many of the issues are pertinent to both.The use of various fillers and additives,which are compounded into thermoplasticresins, has become more and more prevalentin recent years in the plastics industry. Theaddition of fillers such as talc, mica, calciumcarbonate and nanoclays can increase thestiffness and/or strength and the utilization ofvarious plastics. These fillers have also hadan effect on the performance and life of theequipment that processes them. This paperwill discuss some of the issues that thesecomposites have on the screw design, plusscrew and barrel wear. Screw Design Most screws used in the extrusion ofthermoplastic resins primarily deal with theissues of feeding, melting and pumping of theresin. Feeding the Polymer Melting the Polymer In the feed section of the screw where solidsconveying takes place, the feedingmechanism for a thermoplastic compositemay be quite different from that of the verysame thermoplastic polymer without filler. In the solids conveying function of thescrew, the most critical phenomenon is therelative coefficient of friction (COF) of thepolymer. In the feed section there are threedifferent coefficients of friction at work: theCOF between the pellet and the barrel wall,the COF between the pellet and the screwroot and the COF between pellet and pellet.Although a given polymer may feed verywell in the in the neat, or unfilled, state, theaddition of fillers often causes aconsiderable change in its COF and,therefore, in the screws solids conveyingperformance. For example, any time micais the filler or additive in the base material,the COF drops dramatically. Therefore, thescrew may need to have a longer feedsection of constant depth in order to developenough feed pressure before material entersthe transition section or barrier section.Also, to enhance the solids conveying ofsuch a material, it might require changingthe temperature profile by raising thetemperature in the first barrel zone toincrease the COF between the pellet and thebarrel wall. This would allow the polymerto start to tackify or stick to the barrel so thatit can be conveyed forward. Poor orunstable solids conveying will translatedirectly into low throughput rates and causesignificant surging of the process. The most important aspect of screwgeometry affecting melting is the volumetriccompression ratio. This is determined by thechange in channel volume that takes place in >
Open the catalog to page 1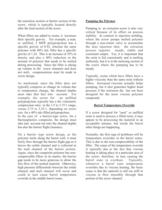
the transition section or barrier section of thescrew, which is typically located directlyafter the feed section of the screw.When fillers are added to resins, it increasestheir specific gravity. For example, a neat,or unfilled, 2 MFR polypropylene has aspecific gravity of 0.92, whereas the samepolymer with 40% talc filler has a specificgravity of 1.24. This is an increase of 35% indensity and also a 40% reduction in theamount of polymer that needs to be meltedduring processing. Since the filler is takingup volume in the screw channels and doesnot melt, compensations must be made inscrew...
Open the catalog to page 2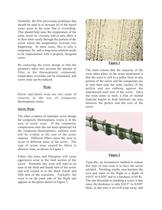
Normally, the first processing technique thatshould be used is to increase all of the barrelzones prior to the zone that is overriding.This should help raise the temperature of theresin, lower its viscosity and in turn allow itto flow more easily through the portion of thescrew where the temperature override washappening. In most cases, this is only atemporary fix, and a long-term solution needsto be implemented with a properly designedscrew.By correcting the screw design so that thegeometry takes into account the amount offiller in the thermoplastic compound,temperature overrides can be...
Open the catalog to page 3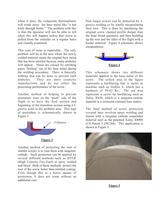
when it does, the composite thermoplasticwill erode away the base metal like a hotknife through butter.Ӕ The problem with thisis that the operator will not be able to tellwhen this will happen unless that screw ispulled from the extruder on a regular basisand visually examined.This type of wear is repairable. The onlyproblem will be at the area where the newlywelded material meets the original base metalthat has been nitrided because many pinholeswill appear. These are caused by nitridinggases boilingӔ out of the base metal duringthe welding procedure. There is basicallynothing that can be...
Open the catalog to page 4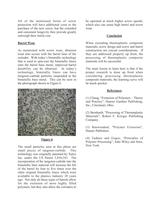
All of the mentioned forms of screwprotection will have additional costs to thepurchase of the new screw, but the extendedand consistent longevity they provide greatlyoutweigh their initial cost. Conclusion Barrel Wear When extruding thermoplastic compositematerials, screw design and screw and barrelconstruction are crucial considerations. Ifthey are addressed properly up front, theprocessing of thermoplastic compositematerials will be successful.The main lesson to learn here is that if theproper research is done up front whenconsidering processing thermoplasticcomposite materials, the...
Open the catalog to page 5All Nordson Xaloy catalogs and technical brochures
-
Custom Injection Units
1 Pages
-
FTR Valves
2 Pages
-
Auto-Shut Valves
2 Pages
-
Injection Molding Screws
2 Pages
-
Pulsar® Mixing Screw
1 Pages
-
Z-Mixer? Screw
1 Pages
-
Fusion™ II screw
2 Pages
-
SmartHeat? Coating
4 Pages
-
Injection Barrels
1 Pages
-
Mini Jet Cleaner
2 Pages
-
JCP 1724 Jet Cleaner
2 Pages
-
WRP-35s/36s Pelletizer
2 Pages
-
WRP-12i In-Line Pelletizer
2 Pages
-
Static Mixers
2 Pages
-
EquaTherm® Rolls
2 Pages
-
Durashell
2 Pages
-
Standard extrusion pumps
2 Pages
-
Extrusion Barrels
1 Pages
-
X8000
1 Pages
-
Extrusions screws
2 Pages
-
Elastomer Nozzle
7 Pages
-
BHP Shutoff Nozzle
11 Pages
-
Hydraulic changers
2 Pages
-
Front-end components.
3 Pages
-
Stratablend® II
1 Pages
-
Efficient™ Extrusion Screw
1 Pages
-
Fusion™ Screw
2 Pages
-
Xaloy Extrusion equipment
1 Pages
Archived catalogs
-
Gross® Equatherm® Rolls
1 Pages
-
Nano™ Mixer
1 Pages