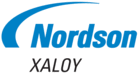
Catalog excerpts
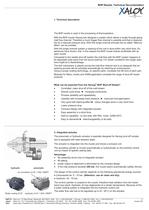
1. Technical description The BHP nozzle is used in the processing of thermoplastics > With the BHP nozzle Herzog has designed a system which allows a single through-going melt flow channel. Therefore a much bigger flow channel is possible and that is responsi-ble for a reduced pressure drop. With this single channel principle the so called Memory effectӔ can be avoided. With the single channel system a cleaning of the unit is done within very short time. Ex-periences have shown, that in this respect the BHP nozzle shares similarities with an open nozzle. Compared to the needle shut-off...
Open the catalog to page 2
BHP-Nozzle, Technical Documentation > 3. Risk of collision by driving into the mold Pay attention to the red marked points at the nozzle. The actuator needs enough space in the stationary plate. Please check the fixed measurements P, Q and S before driving into the mold: A longer tip may avoid any collision. In such cases a tip heater band with a separate con-trol unit may be needed. BHP 1 (mm) P 80 Q 68 S 96 K Tip lenght variably adjusted to immersion depth > 360 4. Adjust the component The actuator position is selectable within an angle of 360а. 5. Tip types There are two versions of tip...
Open the catalog to page 3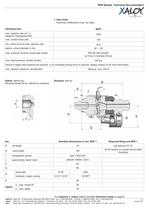
7. Data sheet Technical modifications may be made. Operating data BHP1 max. injection rate cm > 3 / s based on Polystyrene (PS) 1600 max. contact force (kN) 120 min. orifice (mm) at max. injection rate 5 approx. screw diameter in mm 50 ؖ 120 max. pressure at which nozzle gets closed 200 bar with actuator air 6 bar or hydraulic 40 bar max. back-pressure (closed nozzle) 250 bar Should a higher back pressure be required, or an increased closing force is required, please contact us for more information. max. injection pressure / temperature 3000 bar and 400C Option, without tip : Standard, with...
Open the catalog to page 5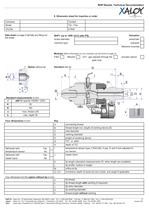
8. Dimension sheet for inquiries or order Company Contact Street Tel. / Fax City/Zip E-Mail Data sheet on page 5 will help you filling out this sheet. BHP1 (up to 1600 cm/s with PS) Actuation screw diameter: pneumatic machine type: hydraulic Machine mounted Modules > (More information on our modules can be found on page 4). actuator sensor Filter Mischer GITӖ gas injected through the gate core Option without tip Standard with tip Standard measurements in mm J 80 *90 special 1000W / 230V K 30 N 180 a max. thread > 35 b max. depth 30 Your dimensions in mm Key A connecting thread B thread...
Open the catalog to page 6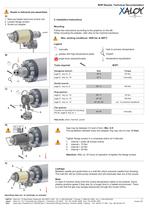
Nozzle is delivered pre-assembled. 9. Installation Instructions Mounting Follow the instructions according to the graphics on the left. When mounting the adapter, refer also to the machine handbook. Gap can be between 0.5 und 2.5mm manually grease with high temperature paste angle lever perpendicularly Max. working conditions: 3000 bar at 400C Leakage: Legend heat to process temperature Inspect temperature equalisation 1. Remove heater band and control unit. 2. Loosen flange screws. 3. Screw out adapter. B) D) E) C) Tools required: BHP1 > Hexagonal wrench: Size Torque page 8, key no. 8 AF 6...
Open the catalog to page 7
10. Nozzle design / Service Assemble nozzle according to numerical order. Disassemble the opposite way around. > Key Quantity Description Key Quantity Description 1 1 body 11 1 bolt 8 2 1 lever 12 1 splint or clip for spindle 8 3 1 lever bolt 踸10 13 1 adapter 4 1 bolt BHP 14 1 tip 5 1 bolt guide 15 1 heater band 80*90 1000W 6 1 cap nut 16 2 heater band screw 7 1 adapter ring- bracket 17 1 temperature sensor 8 8 screws 9 1 actuator 2.1 1 bolt plate 10 2 bolt 12, M14*1 2.2 1 clip 踸8 The following cleaning methods may be used: propane gas oil bath fluidized bath micro-blasting Check each...
Open the catalog to page 8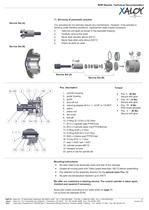
11. Servicing of pneumatic actuator Our actuators do not normally require any maintenance. However, if the actuator is working under extreme conditions, replacement seals maybe necessary. Take the unit apart as shown in the exploded drawing Carefully remove the seals Never heat actuator above 200C! Never heat steel parts above 520аC! Check all parts for wear Service Set (A) Service Set (B) Service Set (A) Service Set (B) Pos. description Torque: 1. cylinder housing 2. guide housing 3. guide 4. shut-off nut 5. reducing adapter M14 x 1 - G1/8 or 1/8 NPT 6. piston 7. piston rod 8. dirt cover...
Open the catalog to page 9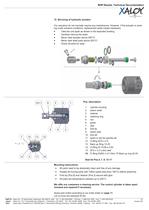
12. Servicing of hydraulic actuator Our actuators do not normally require any maintenance. However, if the actuator is work-ing under extreme conditions, replacement seals maybe necessary. Take the unit apart as shown in the exploded drawing Carefully remove the seals Never heat actuator above 200C! Never heat steel parts above 520аC! Check all parts for wear Pos. description 1. cylinder housing 2. piston shaft 3. retainer 4. retaining ring 5. nut 6. guide 7. disk 8. fork tip 9. piston seal 10. bolt 8 11. splint or clip for spindle 8 12. O-Ring ID12 x 2.5 13. Back up Ring 12-25 14. O-Ring...
Open the catalog to page 10
13. Parts subject to wear / ordering spare parts Worn parts The following parts may become worn: bolt Pos. 4 lever - bolt Pos. 3 bolt guide Pos. 5 lever Pos. 2 bolt P1.5 8 Pos. 11 actuator Pos. 9 Heater bands and T/C can fail with immediate effect. These parts we recommend to keep on stock Spare parts order: ID- No. Please enter the nozzles ID here: It's on the nozzle engraved (sample 205 9999). Quantity Part description (see page 8,9,10) > Xaloy Inc., 72 Stard Road, Seabrook NH 03874 Phone +603 929 82 46 / Fax +603 929 82 47 www.xaloy.com > NAFTA Xaloy Inc. 72 Stard Road, Seabrook, NH...
Open the catalog to page 11All Nordson Xaloy catalogs and technical brochures
-
Custom Injection Units
1 Pages
-
FTR Valves
2 Pages
-
Auto-Shut Valves
2 Pages
-
Injection Molding Screws
2 Pages
-
Pulsar® Mixing Screw
1 Pages
-
Z-Mixer? Screw
1 Pages
-
Fusion™ II screw
2 Pages
-
SmartHeat? Coating
4 Pages
-
Injection Barrels
1 Pages
-
Mini Jet Cleaner
2 Pages
-
JCP 1724 Jet Cleaner
2 Pages
-
WRP-35s/36s Pelletizer
2 Pages
-
WRP-12i In-Line Pelletizer
2 Pages
-
Static Mixers
2 Pages
-
EquaTherm® Rolls
2 Pages
-
Durashell
2 Pages
-
Standard extrusion pumps
2 Pages
-
Extrusion Barrels
1 Pages
-
X8000
1 Pages
-
Extrusions screws
2 Pages
-
Elastomer Nozzle
7 Pages
-
Hydraulic changers
2 Pages
-
Front-end components.
3 Pages
-
Stratablend® II
1 Pages
-
Efficient™ Extrusion Screw
1 Pages
-
Fusion™ Screw
2 Pages
-
Xaloy Extrusion equipment
1 Pages
Archived catalogs
-
Gross® Equatherm® Rolls
1 Pages
-
Nano™ Mixer
1 Pages