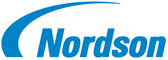
Catalog excerpts
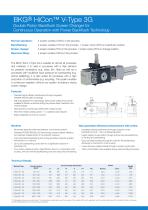
BKG® HiCon™ V-Type 3G Double Piston Backflush Screen Changer for Continuous Operation with Power Backflush Technology Normal operation: 4 screen cavities (100%) in the process 3 screen cavities (75%) in the process, 1 screen cavity (25%) in backflush position Screen change: 3 screen cavities (75%) in the process, 1 screen cavity (25%) in change position Reservoir filling: 4 screen cavities (100%) in the process The BKG HiCon V-Type 3G is suitable for almost all processes and materials. It is used in processes with a high demand for pressure consistency (e.g. strap, film, fiber) as well as in processes with insufficient back pressure for backflushing (e.g. strand pelletizing). It is also suited for processes with a high proportion of contaminates (e.g. recycling). The system enables a continuous operation without any system shutdowns during screen change. Features Patented highly efficient backflushing through integrated POWER BACKFLUSH technology H2 With the patented 4K-75-technology, three screen cavities (75%) remain available for filtration at all times during the process steps “backflush” and “screen change” Optimized flow channel geometries (free of dead zones) Wear-free metallic sealing system – no additional seal required Easily integrated into the line controls New generation efficiency enhancement: Old vs New All process steps are performed pressure- and volume-constant Increased cleaning performance through reduction of the backflushing cycle - only one displacing piston Patented POWER BACKFLUSH technology ensures highest efficiency and operates independently of the extrusion pressure Fully automated backflushing and venting procedure reduces operator intervention to a minimum Up to 200 backflushing cycles allow for a significant reduction in operating cost Higher degree of automation through autonomous parameterizing of venting and backflushing Easy and clean handling through an outlet for the backflushing discharge on the bottom of the housing Lower extrusion height possible through compact construction Four screen cavities provide a large filtration area in a comparably small housing, with only minimal backflushing amounts during the self-cleaning 100% of the filtration area available during reservoir filling procedure Technical Details Machine Type Screen Changer Dimensions L1 * The throughput values are only estimates. The actual rates are dependent upon the viscosity of the material, filter mesh, application and the contamination level of the material; therefore, the values may differ depe
Open the catalog to page 1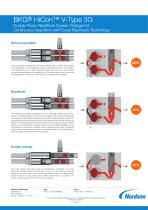
BKG® HiCon™ V-Type 3G Double Piston Backflush Screen Changer for Continuous Operation with Power Backflush Technology Normal operation The heated steel housing allows for two screen bearing pistons, positioned transversely to the melt stream, and containing two screen cavities each per piston. The melt flow is subdivided into four flow paths, directed through each of the four screen cavities, and reunited after filtration at the material outlet. The contamination of the melt and the resulting deposits on the screen packs result in an increase in flow resistance. 75 % The backflushing is...
Open the catalog to page 2All Nordson Polymer Processing Systems catalogs and technical brochures
-
Xaloy® Front End Components
2 Pages
-
BKG-DBCC
2 Pages
-
BKG® HiCon™ R-Type 250
2 Pages
-
Solutions for Electronic
1 Pages
-
Solutions for Sheet
4 Pages
-
Autoflex Technology
2 Pages
-
Rapid Servicing Systems
2 Pages
-
Coextrusion Technology
4 Pages