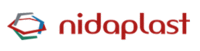
Catalog excerpts
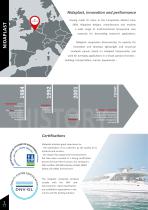
Nidaplast, innovation and performance Having made its name in the Composites Market since 1984, Nidaplast designs, manufactures and markets a wide range of multi-functional honeycomb core materials for demanding industrial applications. Nidaplast composites demonstrates its capacity for innovation and develops lightweight and structural sandwich panels, based on nidaplast honeycombs, and used for everyday applications in a broad spread of sectors : building, transportation, marine, equipments... Induplast integrates the Etex group The first extruded polypropylene honeycomb is launched by...
Open the catalog to page 2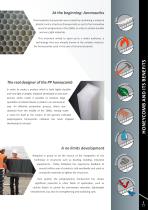
This invention aimed to open up to a wider audience, a technology that was already known in the aviation industry: the honeycombs used in the core of structural panels. Thermoplastic honeycomb was created by combining a material (plastic) and a structure (honeycomb) as part of an innovative research programme in the 1980s, in order to obtain durable and very light materials. The real designer of the PP honeycomb In order to create a product which is both highly durable and very light in weight, nidaplast developed an extrusion process which made it possible to produce large quantities of...
Open the catalog to page 3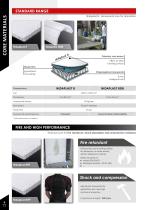
STANDARD RANGE Nidaplast 8 : Honeycomb core for lamination Plastic film guaranteed cell sealing Polyester non-woven offers an ideal bonding surface Polypropylene honeycomb 8 mm hexagonal cell Characteristics Technical core for fire resistance, shock absorption and compression resistance Fire retardant Honeycomb panel providing a better fire behaviour, no smoke toxicity, without halogenous material. Meets standards of : ► railway (EN 45545) ► building (Euroclasse : EN 13-501) ► ... High density honeycomb for applications wich need high mechanical properties. Compressive strength : 260 t/sqm
Open the catalog to page 4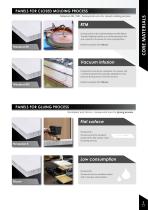
Nidaplast 8R / 8RI : honeycomb core for closed molding process RTM Honeycomb for the implementation by RTM (Resin Transfer Molding) thanks to a reinforced plastic film and a specific non-woven for resin impregnation. Reinforced plastic film 200 µm CORE MATERIALS PANELS FOR CLOSED MOLDING PROCESS Vacuum infusion Honeycomb covered by a polyester non-woven and a reinforced plastic film specially adapted for resin pressure during vacuum infusion process. Reinforced plastic film 300 µm PANELS FOR GLUING PROCESS Nestaplast and Fitcore : honeycomb core for gluing process Flat surface Honeycomb :...
Open the catalog to page 5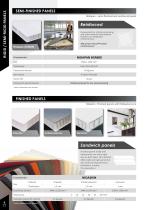
RIGID / SEMI-RIGID PANELS SEMI-FINISHED PANELS Nidapan : semi-finished and reinforced panel Nidapan 8GR600 Characteristics Size Thicknesses Honeycomb density Non-woven Plastic film Honeycomb special features *other dimensions on request Reinforced Honeycomb for a faster processing and a low material consumption thanks to an integrated reinforcement. 600 g/sqm Glass/PP biaxial reinforcement NIDAPAN 8GR600 2500 x 1220 mm* From 10 to 40 mm* 65 kg/sqm 45 g/m2 Polyester 50 pm Reinforced panel for one side processing FINISHED PANELS Nidaskin : finished panels with Nidaplast core Sandwich panels...
Open the catalog to page 6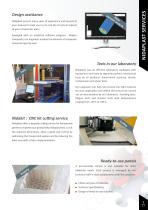
NIDAPLAST SERVICES Design assistance Nidaplast puts its many years of experience and success at your disposal to help you to pre-size the structural aspects of your composites parts. Equipped with an analytical software program, Magics Composite, our engineers analyse the behavior of composite materials layer by layer. Nidaplast has an efficient laboratory equipped with equipment and tools to regularly perform mechanical tests on its products: dimensional accuracy, tensile, compression and shear tests. Our engineers can help you choose the right material for your application and define the...
Open the catalog to page 7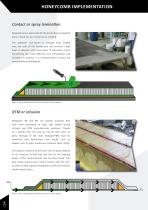
HONEYCOMB IMPLEMENTATION Contact or spray lamination Nidaplast core is well suited for the production of sandwich parts in hand lay-up or spray lay-up molding. The polyester non-woven is strongly heat welded onto the cells of the honeycomb and ensures a high level of adhesion with most types of thermoset resins. Considering the many different resin formulations and variations in process, it is recommended to check the compatibility with Nidaplast. Refer to the implementation requirements for further details RTM or infusion Nidaplast® 8R and 8RI are specific products that have been developed...
Open the catalog to page 8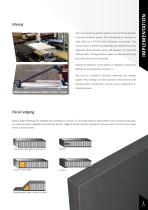
The honeycomb can also be used as a core for the production of glued sandwich panels. The honeycomb is covered on both sides by a PP film and a Polyester non-woven. This surface allows a perfect bonding with most kind of structural adhesives (Polyurethane, Epoxy, MS polymer...) or hot melt adhesive films. The application of glues can be carried out by glue roller (manual or industrial). Almost all materials can be glued on nidaplast honeycomb (Metals, wood, laminates, minerals...) The use of a sandwich structure optimises the weight/ rigidity ratio, making it an ideal solution in many...
Open the catalog to page 9
BUILDING Claddings Prefabricated toilet block Decorative structures Technical doors Bathroom Architectural elements Partitions Technical floors SHOWER CUBICLES ARCHITECTURAL ELEMENTS INTERIOR FURNISHINGS INDUSTRIAL FITTINGS Polyester processing Wind turbine nacelles Floating floors Swimming pools Waterjet cutting support Boxes Bus shelters Urban furniture SWIMMING POOLS URBAN FURNITURE WIND TURBINE POLYESTER PROCESSING
Open the catalog to page 10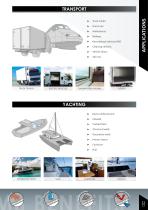
► Truck trailer ► Horse van ► Ambulances ► Railway ► Recreational vehicles (RV) ► Cleaning vehicles ► Vehicle floors ► Site hut YACHTING ► Deck reinforcement ► Catwalk ► Cockpit floor ► Structural walls ► Decorative walls ► Interor layout ► Furniture ► Hull
Open the catalog to page 11All Nidaplast catalogs and technical brochures
-
NIDAPLAST-COMPOSITE-INFUSION
2 Pages
-
NIDAPLAST-COMPOSITE-GLUING
2 Pages
-
LIGHTWEIGHT STONE
8 Pages