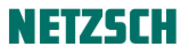
Group: NETZSCH

Catalog excerpts
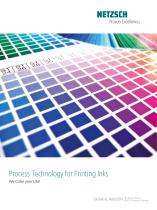
Proven Excellence. Process Technology for Printing Inks We Color your Life! CHEMICAL INDUSTRY a Business Field of NETZSCH Grinding & Dispersing
Open the catalog to page 1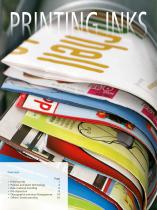
PRINTING INKS Page Printing inks 2 Process and plant technology 4 Raw material handling 6 Pre-dispersion 8 Flexographic printing / Rotogravure 14 Offset / Sc
Open the catalog to page 2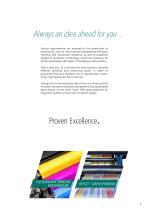
Always an idea ahead for you ... Various requirements are imposed in the production of printing inks, such as color intensity, transparency and gloss, chemical and mechanical resistance, as well as properties related to production technology, which are necessary for further processing with respect to bending or deformation. That is why you, as a printing ink manufacturer, demand efficient grinding and dispersing plants in order to guarantee that your products are of reproducible, consistently high quality for the consumer. Savings on the raw materials side on the one hand, and the increase...
Open the catalog to page 3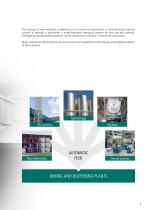
The dosing of raw materials is selected as a function of continuous or discontinuous process control. In general, a distinction is made between transport systems for wet and dry material. Intelligently-designed feed systems can be tailored to a number of machines and plants. Many references demonstrate our know-how and capability for the design and implementation of feed systems. Tank Storage Silo Systems Mini/Medi Bulks AUTOMATIC FEED Dosing Systems MIXING AND DISPERSING PLANTS
Open the catalog to page 5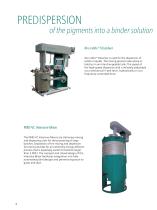
of the pigments into a binder solution MasterMix® Dissolver MasterMix® Dissolver is used for the dispersion of solids in liquids. The mixing process takes place in batches in an interchangeable tank. The speed of the high-speed dispersion disk is infinitely adjustable via a mechanical V-belt drive, hydraulically or via a frequency-controlled drive. PMD-VC Intensive Mixer The PMD-VC Intensive Mixers are stationary mixing and dispersing units for the processing of large batches. Separation of the mixing and dispersion functions provides for an extremely energy-efficient process that is...
Open the catalog to page 6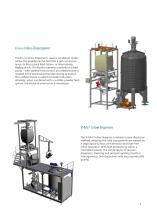
Epsilon Inline-Dispergierer The Epsilon Inline Disperser is used in circulation mode, where the powder can be fed from a sack via suction lance, or from a sack feed station, or alternatively, BigBag or silo. The Epsilon operates similarly to a feed pump – with optimal flow control, an underpressure is created in the processing chamber during operation. This underpressure is used for powder induction, whereby, when combined with a suitable powder feed system, the intake of external air is minimized. Ψ-Mix® Inline Disperser The Ψ-Mix® Inline Disperser combines a new dispersion method, whereby...
Open the catalog to page 7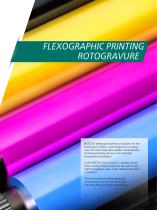
NETZSCH develops machines and plants for the production of flexo- and rotogravure printing inks. The most important quality characteristics for these printing inks are color intensity, transparency and gloss. In the NETZSCH Neos and Discus agitator bead mills, small grinding beads can be used at very high throughput rates under stable production conditions. This means that the defined quality characteristics can be achieved with reproducibility and high productivity.
Open the catalog to page 8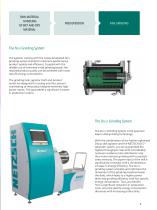
FINE GRINDING RAW MATERIAL HANDLING OF WET AND DRY MATERIAL The agitator cooling with the newly-developed Neos grinding system stands for maximum performance, product quality and efficiency. Coupled with the reliable use of extremely small grinding beads, the required product quality can be achieved with lower specific energy consumption. The grinding tank, agitator shaft and product outlet are designed for cooling and thus prevent overheating of the product despite extremely high power inputs. This guarantees a significant increase in production output. The Discus Grinding System The...
Open the catalog to page 9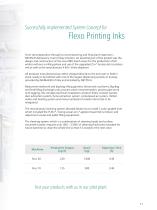
Successfully implemented System Concept for Flexo Printing Inks From site preparation through to commissioning and final plant inspection – NETZSCH delivered a true turnkey solution. An essential part of the project was the design and construction of the new PMD batch mixer for the production of NC whites without a milling phase and use of the upgraded Zeta® horizontal circulation mill as well as the revolutionary Ψ-Mix® inline disperser. All products manufactured are either shipped directly to the end user or held in stock, ready to be bottled with one of the largest dispensing systems in...
Open the catalog to page 11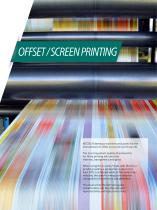
OFFSET / SCREEN PRINTING NETZSCH develops machines and plants for the manufacture of offset and screen-printing inks. The most important quality characteristics for these printing inks are color intensity, transparency and gloss. When using the TetraNex® disks with the Discus grinding system, a production output of at least 30% is achieved while, at the same time, reducing the specific energy consumption compared to the previous disk geometry. This means that the defined quality characteristics can be achieved with reproducibility and high productivity.
Open the catalog to page 12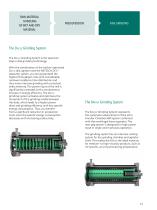
FINE GRINDING RAW MATERIAL HANDLING OF WET AND DRY MATERIAL The Discus Grinding System is the quantum leap in disk grinding technology. With the combination of the further-optimized Discus disk agitator and the NETZSCH DCC® separator system, you are guaranteed the highest throughput rates with considerably narrower residence time distribution and thus more intensive grinding with consistent stress intensity. The power input of the mill is significantly increased, with a simultaneous increase in energy efficiency. The Discus grinding system activates and optimizes the movement of the...
Open the catalog to page 13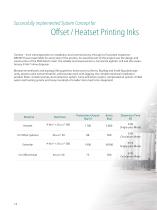
Successfully implemented System Concept for Offset / Heatset Printing Inks Turnkey – from site preparation to installation and commissioning, through to final plant inspection – NETZSCH was responsible for every step of the process. An essential part of the project was the design and construction of the PMD batch mixer, the reliable and improved Discus horizontal agitator mill and the revolutionary Ψ-Mix® inline disperser. Mezzanine steelwork and big-bag lifting gantries; hoists and cruciforms, Big-Bag and Small-Bag discharge units, process valve instrumentation, process pipe work with...
Open the catalog to page 14All NETZSCH Grinding & Dispersing catalogs and technical brochures
-
NETZSCH MiniVac
2 Pages
-
NETZSCH ConduxVita
4 Pages
-
NETZSCH Pre-Grinding Mill ProPhi
12 Pages
-
NETZSCH Zumba
4 Pages
-
NETZSCH Image G&D
28 Pages
-
NETZSCH Connect
4 Pages
-
Pamir
4 Pages
-
Laboratory Mill MiniZeta
2 Pages
-
NETZSCH MasterCream
8 Pages
-
Salsa® System
12 Pages
-
NETZSCH-Beads®
20 Pages
-
NETZSCH Steam Jet Mill s-Jet®
20 Pages
-
NETZSCH Classifier Mills CSM
12 Pages
-
Milling of Spices
4 Pages
-
NETZSCH Fine Impact Mill CONDUX®
12 Pages
-
NETZSCH SPHERHO®
4 Pages
-
NETZSCH Fine Classifier CFS
8 Pages
-
EpsilonVita Inline Disperser
2 Pages
-
Vacuum De-Aerator DA/DA-VS
8 Pages
-
Inline Disperser MaxShear
4 Pages
-
PMD-VC Intensive Mixers
8 Pages
-
MasterMix® Dissolver
8 Pages
-
Ψ-Mix® Inline-Disperser
12 Pages
-
NETZSCH Mill Control Systems
12 Pages
-
Atlas Vertical Roller Mill
4 Pages
-
URAL | Air classifier mill
4 Pages
-
Bora Air Classifier
4 Pages
-
Agitator Bead Mill Alpha®
24 Pages
-
MONSOON | Whizzer Classifier
4 Pages
-
Discus Grinding System
12 Pages
-
Nanomill Zeta RS
20 Pages
-
Zeta® Grinding System
8 Pages
-
Epsilon Inline Disperser
8 Pages
-
AfterSales Support
16 Pages
-
NETZSCH CaseStudy Tango
8 Pages
-
Discus Intensive Rotor
12 Pages
-
Grinding System Neos®
12 Pages
-
Netzsch filter and cyclones
12 Pages
-
NETZSCH SmartRemoval
4 Pages
-
NETZSCH Toll Grinding
8 Pages
-
Agitator Bead Mill DeltaVita®
12 Pages
-
NETZSCH_DeltaVitaMini
4 Pages
-
ALPHA®LAB
2 Pages
-
Fine Cutting Mill SecoMy
8 Pages
-
Laboratory Plants
20 Pages
-
NETZSCH Case Study Sakata
8 Pages
-
NETZSCH Case Study S&S
8 Pages