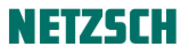
Group: NETZSCH

Catalog excerpts
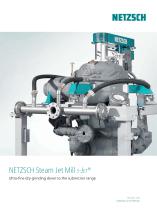
NETZSCH Steam Jet Mill S-JET® Ultra-fine dry-grinding down to the submicron range Business Unit GRINDING & DISPERSING
Open the catalog to page 1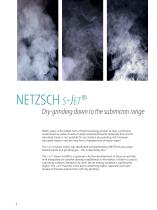
NETZSCH S-JET® Dry-grinding down to the submicron range Water vapor is the oldest form of thermal energy known to man, commonly understood as visible clouds of steam (saturated steam). Naturally this kind of saturated steam is not suitable for use inside a dry-grinding mill. However, saturated steam is not the only form of appearance of water vapor! The S-JET® process which was developed and patented by NETZSCH uses superheated steam as a grinding gas – this is absolutely dry! The S-JET® Steam Jet Mill is a systematic further development of those air jet mills with integrated air classifier...
Open the catalog to page 2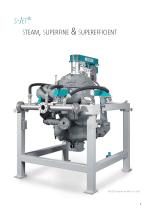
STEAM, SUPERFINE & SUPEREFFICIENT NETZSCH Steam Jet Mill S-JET® 500
Open the catalog to page 3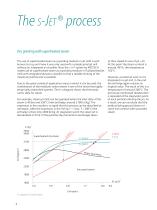
The S-JET® process Dry grinding with superheated steam The use of superheated steam as a grinding medium in jet mills is wellknown, but up until now it was only used with a simple spiral jet mill without an integrated air classifier. Now the S-JET® system by NETZSCH makes use of superheated steam as a grinding medium in fluidized bed jet mills with integrated dynamic classifier so that a reliable limiting of the maximum particle size is possible. Due to the great variety of application areas in which it can be used, the combination of the mediums water/steam is one of the most thoroughly...
Open the catalog to page 4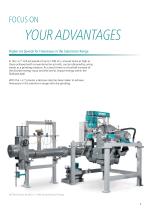
YOUR ADVANTAGES Higher Jet Speeds for Finenesses in the Submicron Range In the S-JET® mill jet speeds of up to 1200 m/s, around twice as high as those achieved with conventional air jet mills, can be obtained by using steam as a grinding medium. As a result there is a fourfold increase of the discrete energy input and the kinetic impact energy within the fluidized bed! With the S-JET® process a decisive step has been taken to achieve finenesses in the submicron range with dry-grinding. NETZSCH Steam Jet Mill S-JET® 500 with grinding air fitting
Open the catalog to page 5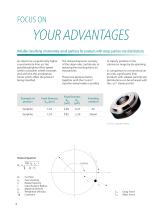
YOUR ADVANTAGES Reliable classifying of extremely small particles for products with steep particle size distributions As steam has a significantly higher sound velocity than air, the possible peripheral flow speed within a classifier wheel increases and with this the acceleration forces which affect the product being classified. The reduced dynamic viscosity of the steam also contributes to reducing the resisting force on the particles. These two decisive factors together with the CONVOR® classifier wheel make it possible In comparison to conventional air jet mills, significantly finer products...
Open the catalog to page 6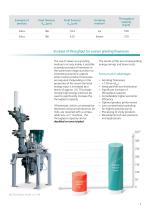
Grinding medium Increase of throughput for coarser grinding finenesses The use of steam as a grinding medium not only makes it possible to produce product finenesses in the submicron range, but also has interesting economic aspects when coarser product finenesses are required. Depending on the properties of the steam the total energy input is increased by a factor of approx. 2.6. This exceptionally high energy yield can be used to significantly increase the throughput capacity. If finenesses, which can already be obtained using conventional air jet mills, are required with a comparable size...
Open the catalog to page 7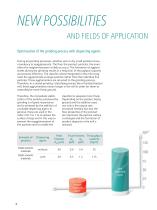
NEW POSSIBILITIES AND FIELDS OF APPLICATION Optimization of the grinding process with dispersing agents During all grinding processes, whether wet or dry, small particles show a tendency to reagglomerate. The finer the product particles, the more often this reaglommeration is likely to occur. This formation of agglomerates during dry-grinding results in a reduction of throughput capacity and process efficiency. The classifier wheel integrated in the mill recognizes the agglomerate as large particles rather than the individual fine particles. These agglomerates are returned to the grinding...
Open the catalog to page 8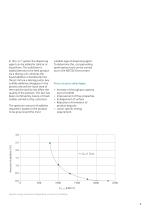
In the S-JET® system the dispersing agent can be added in solid or in liquid form. The solid form is added directly to the feed product via a dosing unit, whereas the liquid additive is fed directly into the jet mill via a dosing pump. Any volatile additives disappear in the process around the input area of the machine and do not affect the quality of the product. This fact has been confirmed by means of check studies carried out by customers. The optimum amount of additive required is based on the product to be ground and the most suitable type of dispersing agent. To determine this,...
Open the catalog to page 9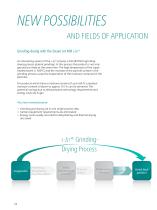
NEW POSSIBILITIES AND FIELDS OF APPLICATION Grinding-drying with the Steam Jet Mill S-JET® An interesting variant of the S-JET® process is the NETZSCH grindingdrying process (patent pending). In this process the product is not only ground but dried at the same time. The high temperature of the superheated steam (> 300°C) and the increase of the particle surface in the grinding process cause the evaporation of the moisture contained in the particles. For products which have a moisture content of up to 60 % a residual moisture content of down to approx. 0.5 % can be achieved. The potential...
Open the catalog to page 10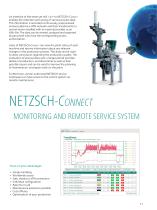
An interface of the steam jet mill S-JET® to NETZSCH-CONNECT enables the collection and saving of various process data. This information is recorded continuously, preprocessed and encoded via a VPN-network and then transferred to a central server installed with an external provider as an XML-file. The data can be viewed, analyzed and exported by personnel who have the corresponding access authorization. Users of NETZSCH-CONNECT can view the plant status of each machine and receive information about any relevant changes in the production process. This data can be used to draw conclusions...
Open the catalog to page 11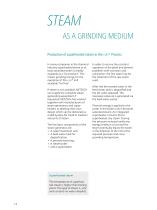
STEAM AS A GRINDING MEDIUM Production of superheated steam in the S-JET® Process In many companies in the chemical industry superheated steam or at least saturated steam is readily available as a “by-product”. This means grinding energy for the operation of the S-JET® mill available “for free”. If steam is not available, NETZSCH can supply the complete steam generating equipment if requested. NETZSCH has worked together with manufacturers of steam generators and superheaters to develop their own design which can be delivered as a Skid System for small to medium amounts of steam. The five...
Open the catalog to page 12All NETZSCH Grinding & Dispersing catalogs and technical brochures
-
NETZSCH MiniVac
2 Pages
-
NETZSCH ConduxVita
4 Pages
-
NETZSCH Pre-Grinding Mill ProPhi
12 Pages
-
NETZSCH Zumba
4 Pages
-
NETZSCH Image G&D
28 Pages
-
NETZSCH Connect
4 Pages
-
Pamir
4 Pages
-
Laboratory Mill MiniZeta
2 Pages
-
NETZSCH MasterCream
8 Pages
-
Salsa® System
12 Pages
-
NETZSCH-Beads®
20 Pages
-
NETZSCH Classifier Mills CSM
12 Pages
-
Milling of Spices
4 Pages
-
NETZSCH Fine Impact Mill CONDUX®
12 Pages
-
NETZSCH SPHERHO®
4 Pages
-
NETZSCH Fine Classifier CFS
8 Pages
-
EpsilonVita Inline Disperser
2 Pages
-
Vacuum De-Aerator DA/DA-VS
8 Pages
-
Inline Disperser MaxShear
4 Pages
-
PMD-VC Intensive Mixers
8 Pages
-
MasterMix® Dissolver
8 Pages
-
Ψ-Mix® Inline-Disperser
12 Pages
-
Discus Intensive Grinding System
12 Pages
-
NETZSCH Mill Control Systems
12 Pages
-
Atlas Vertical Roller Mill
4 Pages
-
URAL | Air classifier mill
4 Pages
-
Bora Air Classifier
4 Pages
-
Agitator Bead Mill Alpha®
24 Pages
-
MONSOON | Whizzer Classifier
4 Pages
-
Discus Grinding System
12 Pages
-
Nanomill Zeta RS
20 Pages
-
Zeta® Grinding System
8 Pages
-
Epsilon Inline Disperser
8 Pages
-
AfterSales Support
16 Pages
-
NETZSCH CaseStudy Tango
8 Pages
-
Discus Intensive Rotor
12 Pages
-
Grinding System Neos®
12 Pages
-
Netzsch filter and cyclones
12 Pages
-
NETZSCH SmartRemoval
4 Pages
-
NETZSCH Toll Grinding
8 Pages
-
Agitator Bead Mill DeltaVita®
12 Pages
-
NETZSCH_DeltaVitaMini
4 Pages
-
ALPHA®LAB
2 Pages
-
Fine Cutting Mill SecoMy
8 Pages
-
Laboratory Plants
20 Pages
-
NETZSCH Case Study Sakata
8 Pages
-
NETZSCH Case Study S&S
8 Pages