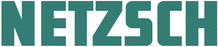
Group: NETZSCH
Catalog excerpts
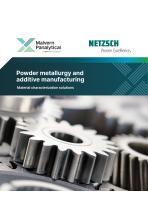
Powder metallurgy and additive manufacturing Material characterization solutions
Open the catalog to page 1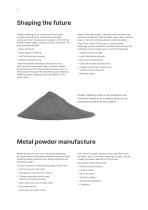
Shaping the future Powder metallurgy is an umbrella term that covers a range of processes for manufacturing metallic components from metal powders usually by first forming a dimensionally stable compact and then sintering it. The main processes include; Additive Manufacturing is a relatively new technique that permits local fusing of metal powders using a laser, electron beam, or by post-sintering adhesive bonded powders. There are a number of reasons for using a powder metallurgy process instead of a traditional process such as machining. These include one or more of the following: • Metal...
Open the catalog to page 2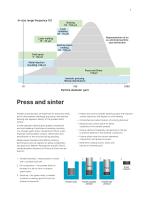
In-size range frequency (%) Brazing 53 - 150 µm Laser cladding 45 - 75 µm Representation of an as-atomized particle size distribution Laser melting 15 - 45 µm Electron beam melting 45 - 106 µm Cold spray 5 - 45 µm Metal injection moulding <38 µm Press and Sinter >45µm Isostatic pressing (Whole distribution) 10 Press and sinter Powder characteristics are important for press and sinter, as for other powder metallurgy processes, with particle packing and apparent density of the powder blend critical. A lower apparent density gives greater compaction and cold-welding of particles on pressing,...
Open the catalog to page 3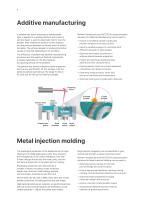
Additive manufacturing In powder bed fusion processes a metal powder layer is applied to a building platform and a laser or electron beam is used to selectively melt or fuse the powder. After melting the platform is then lowered and the process repeated continually until the build is complete. The unfused powder is removed and either reused or recycled depending on its condition. Malvern Panalytical’s and NETZSCH’s characterization solutions for Additive Manufacturing can be used to: • Ensure a consistent powder supply and prevent variations in product quality • Identify suitable powders...
Open the catalog to page 4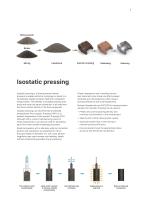
Metal powder Injection molding Isostatic pressing Isostatic pressing is a forming process where pressure is applied uniformly (using gas or liquid) to a hermetically sealed container filled with compacted metal powder. The benefits of isostatic pressing over press and sinter are equal compaction in all directions and more uniform density in the final component. Phase composition and crystallite size are also important since these can affect powder hardness and melt properties which impact pressing efficiency and sintering behavior. Isostatic pressing can be performed at elevated...
Open the catalog to page 5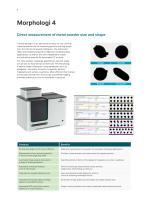
Morphologi 4 Direct measurement of metal powder size and shape The Morphologi 4 is an advanced yet easy-to-use, particle characterization tool for measuring particle size and shape from 0.5 microns to several millimeters. The instrument offers the flexibility required for R&D and troubleshooting applications, as well as the user-independent results and validation required for automated QC analysis. For many powder metallurgy applications, particle shape can be just as important as particle size. The Morphologi 4 reports shape information using parameters such as elongation, circularity,...
Open the catalog to page 6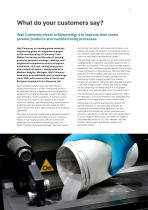
What do your customers say? Wall Colmonoy invest in Morphologi 4 to improve their metal powder products and manufacturing processes Wall Colmonoy is a leading global materials engineering group of companies engaged in the manufacturing of Colmonoy® and Wallex® surfacing and Nicrobraz® brazing products, precision castings, coatings, and engineered components across aerospace, automotive, oil & gas, mining, energy and other industrial sectors. Headquartered in Madison Heights, Michigan, Wall Colmonoy have been an established name in metallurgy since 1938, with several sites in the US and...
Open the catalog to page 7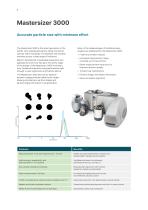
Mastersizer 3000 Accurate particle size with minimum effort The Mastersizer 3000 is the latest generation of the world’s most widespread particle sizing instrument, used by many thousands of companies and research institutes across a wide range of industries. Malvern Panalytical’s considerable experience and applications know-how has gone into every stage of the design of the Mastersizer 3000 instrument, from fundamental particle sizing performance right through to user ergonomics and method advice. The Mastersizer 3000 also has an optional dynamic imaging module called Hydro Insight...
Open the catalog to page 8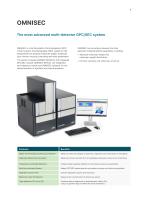
OMNISEC The most advanced multi-detector GPC/SEC system OMNISEC is a Gel Permeation Chromatography (GPC) / Size Exclusion Chromatography (SEC) system for the measurement of absolute molecular weight, molecular size, intrinsic viscosity, branching and other parameters. OMNISEC can accurately measure the most important characterization parameters, including: The system includes OMNISEC RESOLVE, the integrated GPC/SEC module, OMNISEC REVEAL, the integrated multi-detector module and OMNISEC software, for the characterization of synthetic and natural polymers. • ntrinsic viscosity and molecular...
Open the catalog to page 9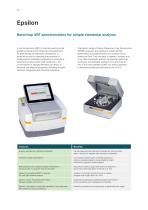
Epsilon Benchtop XRF spectrometers for simple elemental analysis X-ray fluorescence (XRF) is routinely used by metal powder producers and component manufacturers for determining the elemental composition of metal alloys and for detecting the presence of contaminants. Elemental composition is particularly important for alloys since small variations in the concentration of alloying elements can affect its chemical and physical properties, including strength, hardness, fatigue life and chemical resistance. The Epsilon range of Energy Dispersive X-ray fluorescence (EDXRF) analyzers are capable...
Open the catalog to page 10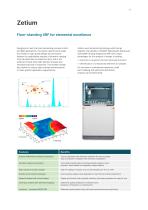
Zetium Floor-standing XRF for elemental excellence Designed to meet the most demanding process control and R&D applications, the Zetium spectrometer leads the market in high-quality design and innovative features for quantitative analysis of elements ranging from beryllium (Be) to americum (Am), and is the preferred choice when light element analysis and analytical precision is important. The modular design also allows for various task-oriented enhancements to meet specific application requirements. Zetium uses SumXcore technology which brings together the benefits of WDXRF (Wavelength...
Open the catalog to page 11All NETZSCH Analyzing & Testing catalogs and technical brochures
-
DMA 303 Eplexor
24 Pages
-
LFA 717 HyperFlash® Series
28 Pages
-
DSC 300 Caliris Series
28 Pages
-
STA 509 Jupiter Series
28 Pages
-
TG 309 Libra Series
24 Pages
-
DEA 288 Ionic
20 Pages
-
STA 2500 Regulus
12 Pages
-
NTA Guarded Hot Plate Series
16 Pages
-
TMA 402 F1/F3 Hyperion®
16 Pages
-
Rosand Series
20 Pages
-
Accelerating Rate Calorimetry
20 Pages
-
NTA HotBoxes
16 Pages
-
DIL 402 Expedis Select/Supreme
28 Pages
-
DIL 402 Expedis Classic
16 Pages
-
Product Overview
12 Pages
-
NETZSCH Energy Solutions
40 Pages
-
Advanced Materials Testing
32 Pages
-
NTA Fire Testing Systems
20 Pages
-
Kinetics NEO
20 Pages
-
TG-FTIR - product brochure
24 Pages
-
TA-QMS Coupling
28 Pages
-
Kinexus Prime DSR Series
20 Pages
-
Kinexus Prime Series
20 Pages
-
HMOR 422
1 Pages
-
RUL/CIC 421
1 Pages
-
Cone Calorimeter TCC 918
12 Pages
-
Thermal Insulation Materials
24 Pages
-
SBA 458 Nemesis®
24 Pages
-
NETZSCH NEVIO Instrument Series
24 Pages
-
LFA 427 - product brochure
24 Pages
-
DMA GABO EPLEXOR up to 1500°C
12 Pages
-
GABOMETER®
8 Pages