Catalog excerpts
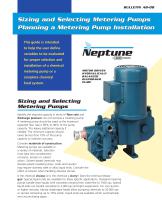
Sizing and Selecting Metering Pumps Planning a Metering Pump Installation This guide is intended to help the user define variables to be evaluated for proper selection and installation of a chemical metering pump or a complete chemical feed system. MOTOR DRIVEN HYDRAULICALLY BALANCED DIAPHRAGM PUMP Sizing and Selecting Metering Pumps Identify the required capacity in terms of flow rate and discharge pressure. Do not oversize a metering pump. A metering pump should be sized so the maximum expected flow rate is 85% to 90% of the pump capacity. This leaves additional capacity if needed. The minimum capacity should never be less than 10% of the pump capacity to maintain accuracy. Consider materials of construction. Metering pumps are available in a variety of materials. Selection must take into consideration corrosion, erosion or solvent action. Solvent-based chemicals may dissolve plastic headed pumps. Acids and caustics may require stainless steel or alloy liquid ends. Consider the effect of erosion when handling abrasive slurries. Is the chemical viscous or is the chemical a slurry? Does the chemical release gas? Special liquid ends are available for these specific applications. Standard metering pumps handle clear liquids with viscosities ranging from water-like to 1500 cps. Special liquid ends can handle viscosities to 5,000 cps and light suspensions. For true slurries or higher viscosity, tubular diaphragm heads allow pumping chemicals to 20,000 cps or slurries containing up to 10% solids. Liquid ends are available which automatically vent accumulating gases.
Open the catalog to page 1
Sizing and Selecting Metering Pumps continued ELECTRONIC DIAPHRAGM PUMP Double diaphragm heads with leak detection and alarm are available for applications where any diaphragm failure must be sensed immediately. Examples are: applications where contact between the process fluid and the pump hydraulic fluid cannot be tolerated or where, due to the toxic or hazardous nature of the fluid being pumped, leakage cannot be tolerated. Select a driver matching the available utilities which may include electric, air, gas or other means of driving the pump. Identify hazardous area requirements when...
Open the catalog to page 2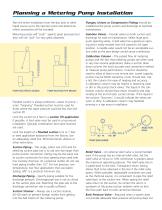
Planning a Metering Pump Installation Plan the entire installation from the day tank or other liquid source up to the injection point and determine which accessories will be included. Flanges, Unions or Compression Fittings should be installed at the pump suction and discharge to facilitate maintenance. Metering pumps will “push” against great pressures but they will not “pull” for very great distances. Isolation Valves – Provide valves on both suction and discharge for ease of maintenance. Select large port, quick opening valves. A ball valve has a generous opening and is easily stroked...
Open the catalog to page 3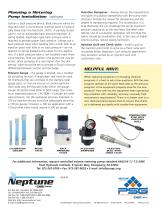
Planning a Metering Pump Installation continued contain a back pressure device. Back pressure valves are required when a low pressure injection point is hydraulically lower than the feed tank. NOTE: A partially closed valve is not an acceptable back pressure regulator. A spring loaded, diaphragm type back pressure valve is required to provide proper back pressure. Always use a back pressure valve when feeding from a bulk tank to an injection point with little or no back pressure—do not depend on spring loaded pump valves for this application. If a back pressure valve is not installed under...
Open the catalog to page 4All Neptune Chemical Pump catalogs and technical brochures
-
Sample Coolers
2 Pages
-
Calibration Columns
2 Pages
-
Pulsation Dampeners
2 Pages
-
Mixer Catalog
12 Pages
-
Neptune Solar D? Pump Series
2 Pages
-
Series PZ Pumps
10 Pages
-
Polymaster
8 Pages
-
By-Pass & Filter Feeder
2 Pages
-
Glycol Feeder
15 Pages
-
Neptune Brochure
20 Pages