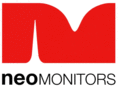
Combustion Control on Process heaters, Fired Heaters, Steel, Glass and High Temperature Processes
3Pages
Catalog excerpts
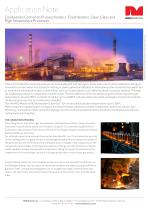
Application Note All Rights Reserved, Copyright © November 2016, NEO Monitors AS Combustion Control on Process heaters, Fired Heaters, Steel, Glass and High Temperature Processes Industrial Combustion Control processes can be broadly split into two types -those where most of the combustion energy is removed to convert water into steam for heating or power generation (boilers) or those where other materials than water (oil or minerals) are heated directly to convert them, such as in a steel plant or on refineries (fired or process heaters). The need for combustion control is a requirement in both areas. The main difference from an analytical point of view is process gas temperature –around 200°C in a boiler stack but up to a 1000°C and more where less heat exchange is involved in materials conversion processes (or in a combustion chamber). The new NEO Monitors Multicomponent LaserGas™ iQ2 can be used at process temperatures up to 1300°C. Multi component capability with a single unit enables the best solution to reliable combustion control, not only for fuel efficiency minimisation of environmental damage, but also with measurements that can reduce maintenance and improve safety and product quality. THE COMBUSTION PROCESS Controlling the air: fuel ratio to get the maximum useful heat from a fuel is always desirable from both a fuel efficiency and an environmental viewpoint. It is now well accepted that simultaneous measurement of both excess O2 and CO will enable complete combustion without heating needlessly excess air. For material conversion processes there can be other benefits too. If the combustion process for the melting tanks in a glass furnace is not managed properly this can impact the quality of the glass and shorten the lifetime of the melting furnaces. Changes in the composition of the fuel gas will cause changes in the physical properties of the gas and the minimum air requirements needed to achieve stoichiometric combustion. Failing to respond to variations in the composition of the natural gas can result in losing a production run due to poor gas quality. In steel making, impurities such as sulphur and excess carbon are removed from the raw iron, and alloying elements such as nickel, chromium and vanadium are added to produce different grades of steel. Limiting dissolved gases such as nitrogen and oxygen, and entrained impurities in the steel is also important to ensure the quality of the products cast from the liquid steel. NEO Monitors as • A subsidiary of Norsk Elektro Optikk • Prost Stabels vei 22 • N-2019 Skedsmokorset, Norway Phone +47 67 97 47 00 • www.ne
Open the catalog to page 1
Application Note A process heater is a direct-fired heat exchanger that uses the hot gases of combustion to raise the temperature of a feed flowing through coils of tubes aligned throughout the heater. Depending on the use, these are also called furnaces or fired heaters. Process heaters are used throughout the hydrocarbon and chemical processing industries in places such as refineries, gas plants, petrochemicals, chemicals and synthetics, olefins, ammonia and fertilizer plants. Some plants may have only two or three heaters while larger plants can have more than fifty. Not only fuel cost,...
Open the catalog to page 2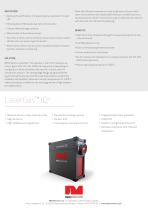
MOTIVATION • Optimum Fuel efficiency -CO levels may be read down to 1 ppm LDL • Minimisation of NOx levels due to O2 minimisation • Cleaner Heat exchange surfaces More than 30 years’ experience as the originators of cross stack laser measurement have enabled NEO Monitors to add features to the measurement which minimise the need to calibrate and concerns with line lock and collisional broadening. • Minimisation of Greenhouse Gases • Operational safety where methane measurement may be used to identify start up issues in gas fired plant • Water measurement may be used to establish wet/dry...
Open the catalog to page 3All NEO Monitors catalogs and technical brochures
-
LaserGas-III-SP-NH3-DeNOx
2 Pages
-
LaserGas-iQ2-Vulcan
2 Pages
-
LaserGas-iQ2
2 Pages
-
Application note DeNox
2 Pages