Catalog excerpts
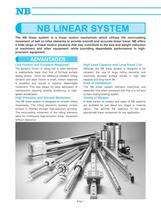
The dynamic friction of rolling ball or roller elements is substantially lower than that of full-face surface sliding friction. Since the difference between rolling dynamic and static friction is small, motion response is excellent and results in superior dependable movement. This also allows for easy fabrication of mechanisms requiring precise positioning or high- speed acceleration. Although the NB linear system is designed to be compact, the use of large rolling elements and machined raceway surface results in high load capacity and long travel life. > The NB linear system shortens machining and assembly time when compared with that of a full face surface sliding bearing system. > The NB linear system is designed for smooth rolling movements. The rolling element's raceway contact surface is finished through high-precision grinding. The recirculating movement of the rolling elements allow for continuous high-precision linear movement without clearance. A wide variety of models and types of NB systems are available for just about any shape or material option. This permits the selection of the best appropriate linear component for any application. Eng-1 >
Open the catalog to page 1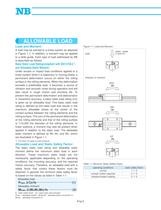
Figure 1-1 Load and Moment > rated loads C and Coload direction of momentpitch yaw roll Table 1-1 Minimum Static Safety Factor > *1: This does not apply to some products. operating conditions static safety factor normal 1 2 smooth motion required 2 4 vibration/impact loading 3 5 > fs : static safety factor Co : basic static load rating(N)Pmax. : allowable load(N) M P ,M R ,M Y : allowable static moment(N m)Mmax. : allowable moment(N m)
Open the catalog to page 3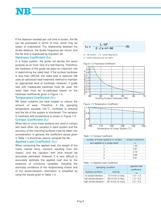
L > h : life time(hr) s : stroke distance(m) n1 : stroke frequency per min.(cpm) Figure 1-2 Hardness Coefficient > H Hardness Coefficient, f Tracking Surface Hardness, HRC > Figure 1-3 Temperature Coefficient > T Temperature Coefficient, f Temperature of Linear System ( )Table 1-2 Contact Coefficient > number of linear systems in contactand applied to a single shaft contact coefficientf > W 1 1.00 2 0.81 3 0.72 4 0.66 5 0.61 Table 1-3 Applied Load Coefficient operating condition applied load coefficient,f loading condition velocity > W no shock/vibration 15 m/min or less 1.0 1.5 low...
Open the catalog to page 5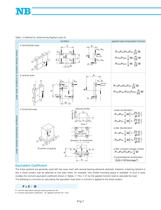
Table 1-5 Method for Determining Applied Load (2) condition applied load computation formula > thrustforcethrust force under static conditions or constant velocity motionunder constant acceleration conditions under accelerationunder decelerationunder constant velocity motion > velocity V time Tthrust force G:center of gravitydirection of movement velocity profile thrust force g:gravitational acceleration 2 vertical/side axes 2 vertical axes 2 horizontal axes > The linear systems are generally used with two axes, each with several bearing elements attached. However, a bearing element ortwo...
Open the catalog to page 7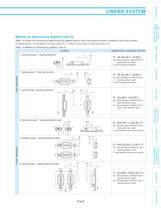
SLIDEGUIDEBALLSPLINE ROTARYBALLSPL W: applied load (N) P: load applied to the linear system (N) : distance to the center of a bearing element (mm) > 2 Ep > 1 : Mp equivalent coefficient with 1 bearing element usedEr: Mr equivalent coefficient > 2 SLIDEBUSHSLIDEUNITSTROKEBUSH 2 Ey1: My equivalent coefficient with 1 bearing element usedEr: Mr equivalent coefficient > 1 W W > 2 1 axis application2 axes application 2 Ep > 1 : Mp equivalent coefficient with 1 bearing element usedEy1: My equivalent coefficient with 1 block (outer cylinder) used > SLIDEROTARYBUSH Ep > 1 : Mp equivalent coefficient...
Open the catalog to page 8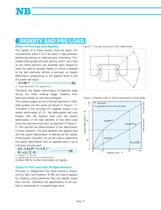
Effect of Pre-load and Rigidity: > Figure 1-7 Contact Structure of SGL Slide Guide The rigidity of a linear system must be taken into consideration when it is to be used in high-precision positioning devices or high-precision machinery. Pre- loaded slide guides and ball splines, which use a ball as the rolling element, are available upon request to meet the need for greater rigidity. If a force is applied to the ball elements without a pre-load, an elastic deformation proportional to the applied force to the 2/3 power will result. W > 2/3 (8) > : elastic deformation W : applied force...
Open the catalog to page 17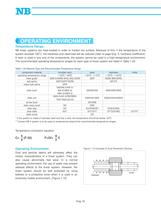
Table 1-23 Material Type and Recommended Temperature Range * If the system is made of stainless steel and has a seal, the temperature should be below 120 component material includes resin steel stainless other operating temperature range 20 80 20 110 20 140 slide guide SEB-A/SEBS-B/GL/SGL/SGW SER SEBS-BM/SERS ball spline SSP/SSPF/SSPB SPLFS rotary ball spline SPR GM/SM G/KB G/SW G/SMS G/KBS G/SWS G slide bush SM/KB/SW SMS/KBS/SWS SMA G/AK G/RB/RBW/TKA/TWA/CE/CD slide unit SMA/AK/SWA SMSA/AKS/SWSA stroke bush SR/SRB slide rotary bush RK SRE slide way NV SV/SVW/RV SVS/SVWS slide table NVT...
Open the catalog to page 19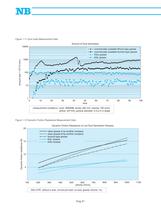
Figure 1-11 Dust Level Measurement Data Amount of Dust Generatedcommercially available lithium-type greasecommercially available fluorine-type grease KGU grease KGL grease timemeasurement conditions / work: SEBS9B; stroke: 200 mm; velocity: 700 mm/s airflow: 3m 1000010001001001009080706050403020101 > amount (per 1 CF/10 min.) 3 /min; particle diameter: 0.3 m or larger Figure 1-12 Dynamic Friction Resistance Measurement Data clean grease A by another company clean grease B by another companyfluorine-type greaseKGL GreaseKGU Grease201510510020030040050060070080090010001100 > Dynamic friction...
Open the catalog to page 21
Follow the instructions below to maintain the accuracy of NB linear system as a precision part and to use it safely.(1) Notes on Handling Any shock load caused by rough handling (such as dropping or hitting with hammer) may cause a scar on the raceway which will hinder smooth movement and shorten expected travel life. Also be aware that such impact may damage the resin parts. Never try to disassemble the product. Doing so may cause an entry of contamination or deterioration of assembly accuracy. The blocks or the outer cylinders may move just by tilting the rail or the shaft. Be careful not...
Open the catalog to page 23All NB catalogs and technical brochures
-
SLIDE SHAFT SPINDLE SHAFT
24 Pages
-
STROKE BUSH SLIDE ROTARY BUSH
14 Pages
-
TOPBALLR
13 Pages
-
SLIDE BUSH
74 Pages
-
SLIDE GUIDE
40 Pages
-
FIT Series
2 Pages
-
Actuator BG15
2 Pages
-
Linear System General Catalog
293 Pages
-
Slide Guide SEBS-BS
4 Pages
-
ROTARY BALL SPLINE SPB type
4 Pages
-
TOPBALL Slide Products
28 Pages
-
Compact Slide Way NYT/NYTS
2 Pages
-
BALL SPLINE SSP-AM type
2 Pages
-
SLIDE SCREW
4 Pages
-
ACTUATOR
39 Pages
-
LINEAR SYSTEM
21 Pages
Archived catalogs
-
General Catalog
289 Pages
-
NB - Slide Way
14 Pages
-
NB - Rotary Ball Spline
2 Pages
-
NB - Actuator
55 Pages
-
NB - Slide Bush
4 Pages
-
NB - Slide Rotary Series
14 Pages
-
NB - Miniature Slide Table
6 Pages
-
NB - Gonio way
8 Pages
-
NB - Slide guide
18 Pages