Catalog excerpts
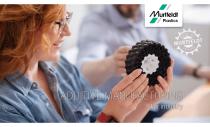
ADDITIVE MANUFACTURING
Open the catalog to page 1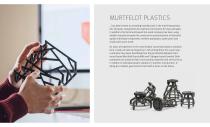
MURTFELDT PLASTICS … has been known as a leading manufacturer in the machining production of plastic components for machine construction for many decades. In addition, the Dortmund-based mid-sized company has been using additive manufacturing for the construction and production of industrialquality individual components, resilient prototypes, spare parts and small series since 2016. 65 years of experience in the machining of customised plastic solutions here, 5 years of start-up dynamics in 3D printing there: for a year now, customers have been benefiting from the partnership between...
Open the catalog to page 2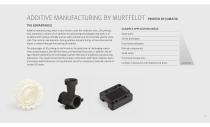
ADDITIVE MANUFACTURING BY MURTFELDT THE ADVANTAGES Additive manufacturing, which is also known under the collective term „3D printing“, now represents a whole set of additive manufacturing technologies that work in accordance with various principle and are each suitable only for extremely specific materials. The common denominator: During additive manufacturing, a three-dimensional object is created through the layering of material. The advantages of 3D printing do not lie only in the production of challenging components and prototypes, fast delivery times, and lower planning costs; in...
Open the catalog to page 3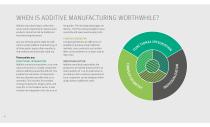
WHEN IS ADDITIVE MANUFACTURING WORTHWHILE? INDIVIDUALIZATION Additive manufacturing enables the production of tailored products from an order quantity of 1 up to small series in accordance with customer requirements. Each component can be designed individually without additional costs. These points are: FUNCTIONAL INTEGRATION Additive manufacturing allows us to unite various functions in a single component – without additional assembly efforts! This enables the realization of components that are otherwise possible only as an assembly. This includes, for example, moving components, hinges,...
Open the catalog to page 4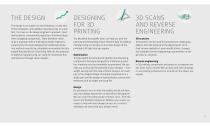
THE DESIGN The design is not subject to any limitations, or only very minor limitations, with additive manufacturing. In actual fact, it is more so the design engineer’s approach, tried and tested for conventional production, that limits ideas when designing components. There therefore needs to be a quantum shift in thinking by design engineers: components that were designed for traditional production methods need to be completely reconsidered to fully exploit the potential of 3D printing. After all, the potential of additive manufacturing can really be maximised first and foremost through...
Open the catalog to page 5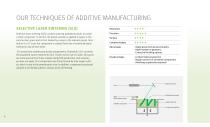
OUR TECHNIQUES OF ADDITIVE MANUFACTURING SELECTIVE LASER SINTERING (SLS) Selective laser sintering (SLS) involves sintering powdered plastic to create a solid component. To do this, the plastic powder is applied in layers in the construction space and is then heated by a laser in the relevant places. Similarly to in a CT scan, the component is created from lots of individual layers sintered on top of each other. SLS production enables practically any geometry. Polyamide 12 is currently the powdered source material for SLS. Thanks to the use of a laser, SLS parts are more precise than those...
Open the catalog to page 6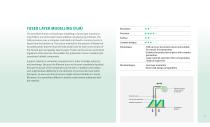
FUSED LAYER MODELLING (FLM) The procedure known as fused layer modelling or fused layer manufacturing (FLM) is one of the best known additive manufacturing methods. The FLM procedure uses a computer-controlled print head to construct parts in layers from the bottom up. The source material for the process is filament of extruded plastic that the machine selectively fuses for each cross section of the desired part and applies layer by layer. Thanks to the precise control and regulation of the process, this enables the production of even complex (and sometimes hollow) components. Support...
Open the catalog to page 7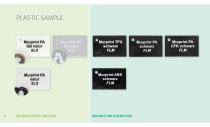
PLASTIC SAMPLE
Open the catalog to page 8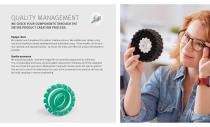
QUALITY MANAGEMENT WE CHECK YOUR COMPONENTS THROUGH THE ENTIRE PRODUCT CREATION PROCESS. Design check We support you throughout the product creation process. We validate your design using functional models in repeat development and production loops. These models can be printed, checked, and adjusted quickly - to ensure the most cost-effective product development possible. Quality assurance We ensure top quality - and we‘re happy for our specialist department to verify that. The corresponding processes and associated measurement methods are firmly integrated into our production processes....
Open the catalog to page 9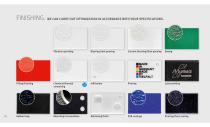
FINISHING. WE CAN CARRY OUT OPTIMIZATION IN ACCORDANCE WITH YOUR SPECIFICATIONS. Vibratory grinding Ceramic blasting/Shot peening Blasting/shot peening Chemical/thermal smoothing Laser printing Machining finish Printing/flock coating
Open the catalog to page 10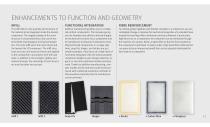
ENHANCEMENTS TO FUNCTION AND GEOMETRY INFILL FUNCTIONAL INTEGRATION FIBRE REINFORCEMENT The infill refers to the quantity and structure of the material to be integrated inside the desired component. The targeted design of this inner structure is characterized by a low use of material while retaining good mechanical properties. The more infill used, the more robust and the heavier the 3D component. The infill structures can vary, and must be chosen and applied to the component in accordance with the load state. In addition to the strength, rigidity, and material savings, the anisotropy of...
Open the catalog to page 11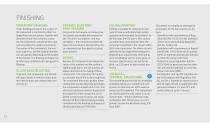
FINISHING VIBRATORY GRINDING In this finishing procedure, the surface of the component is machined so that it no longer feels raw and porous. Together with abrasives (made from ceramics or plastic), the components are placed into a tub and are polished by relative movements. The surface of the components, the residual roughness, and the material abrasion can vary greatly depending on the duration of the process. This finishing technique can be effectively combined with dyeing and infiltrating. GLASS BEAD BLASTING In general, SLS components are blasted with glass beads to remove excess...
Open the catalog to page 12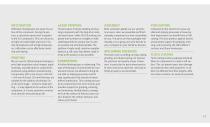
Infiltration impregnates and seals the surface of the component. During the process, a colourless epoxy resin is applied to the SLS component. This can ensure an air-tight and water-tight seal even in humid atmospheres and at high temperatures. Infiltration can be effectively combined with dyeing. We can use UV LED printing technology to print high-resolution colour images, apply markings, and add labels to components produced using additive manufacturing. Components with a size of up to 300 mm × 420 mm (A3) and 150 mm thickness are suitable for the addition of printing. Since the print...
Open the catalog to page 13All Murtfeldt catalogs and technical brochures
-
M s urytal® H / Murytal® E
1 Pages
-
All chapters
169 Pages
-
Fabrication competence
6 Pages
-
The Material "S" plus+ ® Family
14 Pages
-
SOLUTIONS IN PLASTICS
168 Pages
-
Tensioning systems
35 Pages
-
Chain, belt and sliding guides
56 Pages
-
Oil and lubrication systems
29 Pages
Archived catalogs
-
Chain and belt guides
41 Pages