
Catalog excerpts
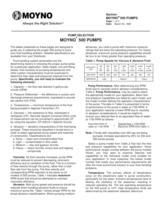
Table 1. Pump Speeds for Viscous & Abrasive Fluid > Page: 1 of 4 Date: March 30, 1996 The tables presented on these pages are designed to guide you in selecting the proper 500 pump to solve your fluid handling problem. Detailed specifications are available from your Distributor. Fluid handling system parameters are the determining factors in choosing the proper pump series for a particular application. Static heads, line and fitting losses, fluid viscosity at pumping temperatures and other system characteristics must be examined to determine flow rates and pressures required from the pump. Specifically, you will need to evaluate the following elements: 1. Capacity the flow rate desired in gallons per minute (GPM). 2. > VISCOSITY (CP) 100 to300300 to500500 to1,000 1,000 to2,000 2,000 to5,000 5,000 to10,000 10,000 to20,000 Pressure Differential ח the difference in suction and discharge pressure requirements, expressed in pounds per square inch (PSI). 3. > MAX RPM 1400 1200 950 700 350 180 100 ABRASION Light Medium Heavy Temperature maximum temperature of the fluid being pumped in degrees Fahrenheit (װF). 4. Pump Performance. After determining any RPM limits due to viscosity and/or abrasion considerations, Table 2, Pump Performance , may be used to select the appropriate model for your application. Basic flow and pressure Capabilities are listed for each model, and the model number defines the operation characteristics of the pump. The data in Table 2 is presented in terms of performance of the pump in water at 1750 RPM. If your application requires a lower RPM due to viscosity or abrasion considerations, it would be helpful to convert your desired flow to an equivalent flow of water at 1750 RPM as follows: Viscosity the resistance to flow, expressed in centipoise (CP). Seconds Saybolt Universal (SSU) units of measurement can be converted to approximate CP by using this equation: CP=SSU/5 x Specific Gravity. 5. Abrasion ח abrasive characteristics of the fluid being pumped. These should be classified in broad terms in order to select appropriate pump speed and materials of construction. Classifications are: a. None clean and uncontaminated fluid b. Light ח contaminated or dirty water c. Medium clay and gypsum slurries d. Heavy ח heavy slurries, emery dust and lapping compounds > Equivalent flow of water at 1750 RPM =Desired flow x 1750 RPM Maximum RPM (from table 1) Viscosity . As fluid viscosity increases, pump RPM must be reduced to prevent decreasing volumetric efficiency due to cavitation of the fluid. This is a function of flow velocity through the pump, rather than a total flow rate from the pump. The flow velocity and corresponding RPM reduction is the same on all models of 500 pumps. Table 1 indicates Note: If fluids with viscosities over 200 cps are being pumped, increase equivalent by 20% for 200 and 300 series pumps. Select a pump model from Table 2 that has the flow and pressure capabilities for your application. Since performance ranges overlap between the pump models shown, you may want to examine features and capabilities of the individual model most suitable for your application. In most instances, the lowest model number that meets your performance requirements will offer the most economical solution to your fluid handling problems. maximum RPM levels that should be attempted to maintain volumetric efficiency. Abrasion . Both pump speed and pressure should be reduced when handling abrasive fluids to ensure maximum pump life. Table 1 shows proper RPM for the broad abrasion classifications. When pumping medium abrasives, you need a pump with maximum pressure ratings that are twice the operating pressure. For heavy abrasives, maximum pump pressure capabilities should be four to six times greater than operating pressure. Temperature . The primary effects of temperature occur on the elastomers used in pump construction, particularly for the stator. Extreme temperatures tend to destroy the resiliency of the elastomer, resulting in reduced operating life. The low operating temperature for the 500 pump is 10F. High temperature limits are determined by the elastomer selected. Maximum >
Open the catalog to page 1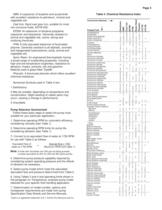
Page 3 Table 4. Chemical Resistance Index NBR. A copolymer of butadine and acrylonitrile with excellent resistance to petroleum, mineral and vegetable oils. Cast Iron . Sand cast grey iron, suitable for most non-corrosive fluids, ASTM A25. EPDM . An elastomer of ethylene propylene copolymer and terpolymer. Generally resistant to animal and vegetable oils, ozone, strong and oxidizing chemicals. FPM. A fully saturated elastomer of fluorinated polymer. Generally resistant to all aliphatic, aromatic and halogenated hydrocarbons, acids, animal and vegetable oils. Nylon Resin. An engineered...
Open the catalog to page 3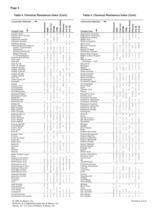
Page 4 Table 4. Chemical Resistance Index ( Cont ) Table 4. Chemical Resistance Index ( Cont ) > 1996 by Moyno, Inc. Printed in U.S.A.ɮ Moyno is a registered trademark of Moyno, Inc. Moyno,Inc.isaUnitofRobbins&Myers,Inc. size="-1">
Open the catalog to page 4All Moyno catalogs and technical brochures
-
EZstrip Cake Pump
2 Pages
-
SERIES A
2 Pages
-
EZstrip™ Hose Pump
16 Pages
-
Dosing pump
2 Pages
-
Hygienic Pump
2 Pages
-
Mine Dewatering
2 Pages
-
InviziQ™
2 Pages
-
EZstrip™ TR Muncher
2 Pages
-
L-Frame
2 Pages
-
EZstrip? Transfer Pump
2 Pages
-
Epsilon/Vertical
2 Pages
-
2000 Pumps
2 Pages
-
Compact C
2 Pages
-
Small Pumps
2 Pages
-
Moyno 1000 Pumps Bulletin
2 Pages
-
Moyno 500 Pumps Bulletin
2 Pages
-
Water/Wastewater Brochure
8 Pages
-
Moyno 1000 Brochure
6 Pages
Archived catalogs
-
EZstrip™ Cake Pump
2 Pages
-
Moyno 500 Pumps Brochure
6 Pages
-
Moyno Metering Pumps Specs
4 Pages
-
Moyno Grinders Specs
2 Pages
-
Moyno Grinders Brochure
8 Pages
-
Moyno 2000 CC Service Manual
16 Pages
-
Moyno 2000 CC Brochure
8 Pages
-
Moyno 1000 Service Manual
34 Pages