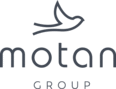
Catalog excerpts
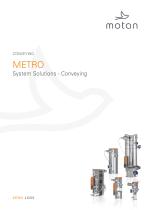
System Solutions - Conveying ZERO LOSS
Open the catalog to page 1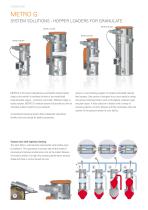
METRO G SYSTEM SOLUTIONS - HOPPER LOADERS FOR GRANULATE METRO G 30I-HSS METRO G is the most comprehensive and flexible material loader range on the market. It combines the best of two established material loader ranges – colortronic and motan. Whether simple or highly complex, METRO G’s modular system will provide you with an individual solution tailored to your demands. A centralised conveying system offers substantial operational benefits and cost savings for plastics processors. Vacuum valve with implosion cleaning The mesh filter is automatically cleaned after each loading cycle by...
Open the catalog to page 2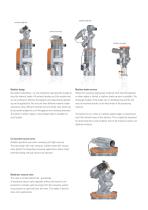
Modular design No product redundancy - as your production requirements change so does the material loader. All material loaders are fully modular and can be matched to different throughputs and requirements depending on the application. Not only are there different material loader volumes but also different material inlet and outlet sizes which can be accurately adapted to suit throughputs and conveying distances. The option of either a glass or steel hopper body is available for most loaders. Lid mounted vacuum valve Reliable operation even when conveying with high vacuums. The cast design...
Open the catalog to page 3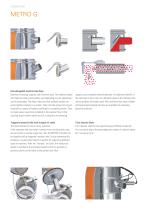
Interchangeable material inlet flaps Optimum conveying capacity and minimum wear. The material loader inlet flaps are easily removeable, and depending on your application, can be exchanged. The flaps make sure that multiple loaders can work together properly in a system. They limit the amount of vacuum required for a group of loaders connected to a coupling station. Thus, no check valves need to be installed in the material flow at the coupling station which would result in a reduction in conveying Tangential material inlet with trumpet air outlet The ideal solution for fine or dusty...
Open the catalog to page 4
Stainless steel discharge flap Because the large material outlet has a discharge flap which is made of stainless steel it is abrasion resistant and meets all requirements for medical or food packaging applications. The angled design increases the outlet area and helps with materials which may bridge. Dampened discharge flap Prevents material jamming and vacuum loss. A spring loaded damper on the discharge flap prevents the flap from completely closing when not under vacuum. During pneumatic conveying any granules left lying on the discharge flap which might get trapped are first sucked...
Open the catalog to page 5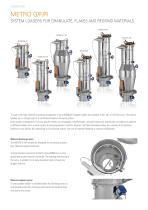
METRO G/F/R SYSTEM LOADERS FOR GRANULATE, FLAKES AND REGRIND MATERIALS METRO R 100 METRO G/F 150 METRO R 150 METRO G/F 60 To cope with large material conveying throughputs of up to 6000kg/h. Hopper loaders are available in 60, 100, or 150 litre sizes. The system loaders are an integral part of a centralised material conveying system. Each system is designed to suit your specific needs; e.g. throughput, material types, and plant layout are individually considered. In addition to different loader sizes, a wide variety of conveying options, controls, blowers, and filter techniques allow the...
Open the catalog to page 6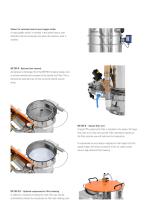
Sensor for maximum level in every hopper loader A rotary paddle switch is installed in the loader body to automatically stop the conveying cycle when the maximum level is reached. METRO R - Optional dust removal As material is discharged from the METRO R material loader, dust is actively removed and conveyed to the central dust filter. This is achieved by generating an air flow using the central vacuum pump. METRO R – Special filter unit A large PTFE-coated cloth filter is installed in the loader. The large filter area to air flow ratio and the Teflon membrane coating on the filter provides...
Open the catalog to page 7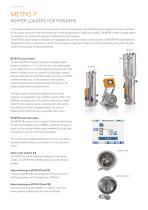
METRO P HOPPER LOADERS FOR POWDERS In the plastics compounding and manufacturing process, there are many powders (all with different flow properties) that require handling. F or the vacuum conveying of both free-flowing and non-free-flowing powders, motan has a solution. The METRO P series of hopper loaders are available in two versions and guarantee reliable and dust-free conveying. The METRO PC system loaders are designed to be integrated into centralised motan conveying systems. The METRO PB single loaders are designed to be used as a “stand-alone” solution. From the material source...
Open the catalog to page 8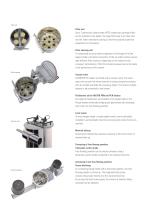
Filter unit Filter unit Up to 7 generously dimensioned ePTFE-coated star cartridge filters can be installed in the loader. The large filter area to air-flow ratio and the Teflon membrane coating on the filters provides optimum separation for all powders. Filter cleaning unit A compressed air accumulator integrated in the hinged lid of the hopper loader with direct connection of the air outlet nozzles secures high-efficient filter cleaning. Depending on the material to be conveyed, optimisation of the filter cleaning sequences can be made in the setup menu of the control. Filter cleaning...
Open the catalog to page 9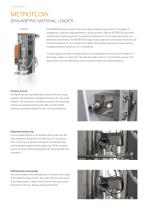
METROFLOW GRAVIMETRIC MATERIAL LOADER METROFLOW The METROFLOW series is part of the motan range of products and systems for all stages of management, conditioning and preparation of plastic granules. With the METROFLOW gravimetric material loader, plastic processors can automate important areas of the production process costeffectively and efficiently. The METROFLOW weighs every single load and evaluates the results with a maximum deviation of 1%. Gravimetric throughput control greatly improves the entire material management process and allows for full traceability. A known quantity of...
Open the catalog to page 10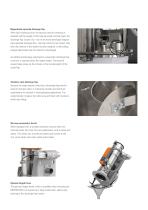
Magnetically operated discharge flap After each conveying cycle, the vacuum used for conveying is released and the weight of the material would normally cause the discharge flap to open. But - due to the newly developed magnetically operated discharge flap - the flap remains firmly closed. Only after the material in the loader has been weighed, is the holding magnet deactivated and the material is discharged. An additional advantage compared to a pneumatic discharge flap: no sensor is required below the hopper loader. The material request takes place via the initiator at the counterweight...
Open the catalog to page 11All Motan gmbh catalogs and technical brochures
-
ALARMcollector
1 Pages
-
LUXOR HD Hot air dryers
4 Pages
-
sCONVAC CONVEYING SOLUTIONS
4 Pages
-
LUXOR SG Dry air dryer
4 Pages
-
LUXOR Simple Solutions - Drying
12 Pages
-
MIXER MODULE MB/MC/Uni
2 Pages
-
BB 60 Blanketing bin
2 Pages