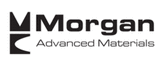

Catalog excerpts
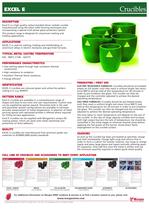
CRUCIBLESTANDS MUFFLERINGS CRUCIBLECOVERS EXCEL and HIMELT are high quality carbon-bonded silicon carbide crucibles manufactured using the latest roller-forming techniques and are designed to cater for a range of non-ferrous melting applications. INDUX is a high quality ceramic bonded clay graphite crucible range manufactured to provide controlled graphite alignment and optimised electrical properties to suit specific frequency ranges for induction melting applications. ISO-ALUSTAR is a premium quality crucible manufactured by high pressure iso-static pressing and incorporating high levels of oxidation resistance and mechanical durability.This product range is designed to provide superior resistance toattack by melt treatment agents typically used in aluminium alloy applications. SALAMANDER SUPER is a high quality ceramic bonded clay graphite crucible range manufactured by plastic forming techniques. ULTRAMELT is a premium quality carbon bonded silicon carbide crucible manufactured by high pressure iso-static pressing.ULTRAMELT incorporates MorganiteҒs advanced bondingtechnology and is the culmination of an intensive development program aimed to provide a superior grade product for the most arduous service conditions. INDUCTION FURNACES: Small Salamander Super crucibles aresometimes used in medium to high frequency induction furnaces. The heat-up procedure is dependent on furnace frequency, coil dimensions, and the resistivity of the metal being melted. It is recommended where possible to preheat the crucible empty. The furnace should initially be run at 20% of maximum power until the crucible shows signs of red heat. After 30 minutes the power can be increased to 50% of the maximum. Loosely charge the crucible with metal and maintain the power level at 50% until approximately half the crucible contains molten metal. The power should then be increased to maximum. > EXCEL is intended for aluminium melting in oil-fired furnaces, melting copper-based alloys in gas and oil-fired furnaces, melting precious metals and non-ferrous allys in low to medium frequency induction furnaces. HIMELT provides enhanced performance in those applicationswhere more arduous service conditions exist. SALAMANDER SUPER crucibles are used to provide consistent performance in fuel-fired furnaces and medium / high frequency induction furnaces. The smaller sizes are typically used to melt precious metals, while larger sizes can be used for some ferrous alloys such as grey iron as well as to melt non-ferrous alloys. INDUX crucibles are used to provide consistent performance in medium frequency induction furnaces. INDUX L crucibles are designed for furnaces operating at 1 2 kHz. INDUX H crucibles are suited to furnaces operating at frequencies from 3kHz and upwards. INDUX crucibles are typically used to melt copper alloys and precious metals. > ISO-ALUSTAR offers superior performance for aluminium holding and melting in electric resistance and gas furnaces, as well as melting and holding of zinc and zinc alloys. ULTRAMELT offers superior performance for aggressive erosive conditions with heavy flux usage in both copper based alloys and precious metal reclamation. The product is designed for use in gas, oil, and low to medium frequency induction furnaces. > SPOUTEXTENSIONS LAUNDERS HOTROD֙ PYROMETERSHEATHS INDUCTION FURNACES: The heat-up procedure is dependant onfurnace frequency, coil dimensions, and the resistivity of the metal being melted. It is recommended where possible to preheat the crucible empty. The power input rate should initially belimited until the crucible becomes bright red over its entire surface. The time taken to pre-heat will depend on the size of the crucible, but is usually in the range 20 40 minutes. Once one third of the crucible is full of molten metal the power can beincreased to a higher level. Silicon carbide crucibles absorb proportionally high levels of power from the induction field. Care should be taken not to overheat the crucible. The actual maximum power setting should be assessed from experience and will be dependant on the capacity of the crucible. The appearance of the inside wall of the crucible should be monitored for signs of over-heating and the power reduced once the full charge is molten. > ֕Clean meltingGood thermal conductivityՕGood resistance to chemical corrosionHigh refractoriness ՕFast melting speed through high consistent thermal conductivityExcellent thermal shock resistance ՕHigh resistance to oxidationGood erosion resistanceՕGood resistance to corrosive attack by chemical treatmentagents Controlled electrical resistivityՕGood thermal conductivityGood resistance to chemical corrosionՕHigh refractoriness > INDUCTION: The heat-up procedure is dependant on furnacefrequency, coil dimensions, and the resistivity of the metal being melted. It is recommended where possible to preheat the crucible empty. The power input rate should initially be limited until the crucible becomes bright red over its entire surface. The time taken to pre-heat will depend on the size of the crucible, but is usually in the range 20 40 minutes. Once one third of the crucible is full of molten metal the power can be increased to a higher level. Silicon carbide crucibles absorb proportionally high levels of power from the induction field. Care should be taken not to overheat the crucible. The actual maximum power setting should be assessed from experience and will be dependant on the capacity of the crucible. The appearance of the inside wall of the crucible should be monitored for signs of over-heating and the power reduced once the full charge is molten. > ֕Excellent resistance to attack by chemical treatment agentsHigh mechanical strengthՕExcellent resistance to oxidation High consistent densityՕFast melting speed through high thermal conductivity Superior erosion resistanceՕHigh resistance to chemical corrosion Excellent thermal shock resistanceՕHigh mechanical strengthHigh consistent densityՕFaster melting speed > FUEL-FIRED FURNACES: Crucibles should be pre-heated emptyuntil they reach a uniform bright red colour (circa 900C) in order topre-condition the glaze. The pre-heating time will depend on the size of the crucible. In the case of large capacity crucibles and furnaces with high output burners the rate of temperature rise should be controlled in the initial stages to minimise thermal stress. The typical time taken from ambient to red heat is up to 1hour. Avoid direct flame impingement on the crucible surface. > FUEL-FIRED: Crucibles should be pre-heated empty until theyreach a uniform bright red colour (circa 900аC) in order to pre- condition the glaze. The pre-heating time will depend on the size of the crucible. In the case of large capacity crucibles and furnaces with high output burners the rate of temperature rise should be controlled in the initial stages to minimise thermal stress. Avoid direct flame impingement on the crucible surface. > ELECTRIC RESISTANCEAND GAS FIRED FURNACES: Cruciblesshould be pre-heated empty. A new crucible should initially be heated slowly to 200C over a period of two hours to eliminate any moisture that may be present. Subsequently the crucible should be heated to 600аC on low power before the full heating rate is used to reach 950C, or the desired working temperature ifhigher. Iso-Alustar crucibles used for holding applications should be held at 950аC for one hour in order to fully develop the anti-oxidant glaze system. The time taken to reach temperature will depend on the size of the crucible but will typically be in the range two and a half to three hours. Avoid direct flame impingement on the crucible surface.The same heat up procedure should be repeated prior to re-useafter a cool-down period. The two hour drying period can be omitted except where the crucible has not been used for a long period in which case moisture that has been absorbed by slag will need to be slowly removed. PUSH-UP/DROP COIL FURNACES: The heat-up procedure isdependant on furnace frequency, coil dimensions, and the resistivity of the metal being melted. 3kHz furnaces: It is recommended where possible to preheat thecrucible empty. The furnace should initially be run at 20% of maximum power until the crucible shows signs of red heat. After 30 minutes the power can be increased to 50% of the maximum. Loosely charge the crucible with metal and maintain the power level at 50% until approximately half the crucible contains molten metal. The power should then be increased to maximum.1kHz furnaces: The power absorption of the empty crucible maybe too poor therefore it may be necessary to pre-heat with a charge loosely in place in order to provide supplementary heating by conduction from the metal charge. Run the furnace at 20% of maximum power until the crucible shows signs of red heat. If after ? hour the crucible shows no evidence of red heat, increase the power to 50% of maximum. Hold at 50% until half the crucible contains molten metal, then increase to maximum power.Tilting furnaces: INDUX crucibles will be prone to thermal shockif the rate of temperature rise of the metal charge is too rapid. It is therefore recommended that where possible the crucible is pre-heated empty from cold using a maximum of 100Kw, or 50% of maximum power, whichever is smaller. Heat the crucible until itbecomes bright red. This should take between 20 and 40 minutes. Once the metal charge is added the crucible itself will absorb very little power and will remain at red heat until the metal melts. On subsequent cycles the preheat procedure is unnecessary when the crucible is still red hot. > SALAMANDER SUPER crucibles are coloured black except forcertain smaller sizes that are supplied unpainted. > INDUX crucibles are coloured black and utilize the suffix INDL orINDH to denote the specific type. > EXCEL crucibles are coloured dark red and utilise the code X.e.g. AX800.HIMELT crucibles are coloured bright red and utilize the code HM e.g. AHM800 ISO-ALUSTAR crucibles are finished green and utilise patterncoding with the suffix ALUS e.g. BN500ALUS > SALAMANDER SUPER crucibles are available in a range of sizes as A-shapes, F-shapes (bilge), and E-shape cylinders to suit a wide spectrum of end user requirements. Ladle liners are also available in standard or bottom pour configuration. ULTRAMELT crucibles are coloured black and utilise patterncoding with the suffix ULTR. > INDUX crucibles are available in a range of sizes as A-shapes, F-shapes (bilge), and E-shape cylinders.Contact Morganite for a specific recommendation based on yourfurnace specification > ISO-ALUSTAR crucibles are available in a range of shapes andsizes to suit most end user requirements. Certain sizes can be made available with pyrometer pocket configuration to facilitate accurate measurement of metal temperature. A selection of fixed pouring spouts with optimised profiles is offered where required for tilting furnace applications. > ULTRAMELTcrucibles are available in a wide range of optimised shapes and sizes to suit a broad spectrum of end user requirements. Heavy wall (HW) versions can be supplied and a range of integral pouring spouts are offered where required. EXCEL and HIMELT crucibles are available in a comprehensive range of shapes and sizes to suit most end user requirements. Custom sizes can be supplied by special request. Heavy wall (HW) versions can be supplied for increased life in arduous applications and a selection of fixed pouring spouts with optimised profiles is offered where required for tilting furnaces. EXCEL and HIMELT crucibles can be supplied with MorganiteՒsunique PD coating system, which can assist with metal cleanliness and prevention of dross adhesion. > SALAMANDER SUPER crucibles are manufactured from premium grade raw materials to ISO9000:2000 quality standards. INDUX crucibles are manufactured from premium grade raw materials to ISO9000:2000 quality standards. > FUEL-FIRED FURNACES: Anew crucible should be pre-heatedempty in order to minimise the temperature gradient across the crucible wall. If the furnace refractories have been repaired or if there is a risk of the crucible having absorbed some moisture, then the furnace should initially be heated slowly up to circa 200C and held at this temperature until all moisture has been driven off. Anew crucible should initially be heated slowly and evenly to600ںC on low power, avoiding local impingement of flame. Subsequently the full heat input rate should be utilised to achieve a uniform bright red condition over the whole crucible (circa 900C / 1650ںF) at which point the crucible should be charged immediately taking care to avoid packing metal tightly orbridging ingots across the crucible. The furnace controls can then be set to achieve the desired metal operating temperature and heating should continue at the full rate until the metal has reached the desired temperature.In the case of crucibles to be fed with molten metal, it isimportant that the crucible body temperature is equivalent to or slightly above that of the molten metal in order to minimise thermal stress. ULTRAMELT crucibles are manufactured from premium grade raw materials to ISO9000:2000 quality standards. ISO-ALUSTAR crucibles are manufactured from premium grade raw materials to ISO9000:2000 quality standards. As soon as the crucible has been pre-heated as specified, charge and melt immediately. Charge light scrap and returns first in order to form a cushion for heavier material. Use tongs to charge ingots and place large pieces and ingots vertically allowing space for expansion. Only add flux once the metal is molten and use the minimum quantity required to obtain good metal quality. > Follow the specified preheat procedure. Charge light scrap and returns first in order to form a cushion for heavier material. Use tongs to charge ingots and place large pieces and ingots vertically allowing space for expansion. Only add flux once the metal is molten > As soon as the crucible has reached the specified pre-heat temperature, charge and melt immediately. Charge light scrap and returns first in order to form a cushion for heavier material. Use tongs to charge ingots and place large pieces and ingots vertically allowing space for expansion. Only add flux once the metal is molten. > Assoon as the crucible has reached the specified pre-heat temperature, charge and melt immediately. Charge light scrap and returns first in order to form a cushion for heavier material. Use tongs to charge ingots and place large pieces and ingots vertically allowing space for expansion. Only add flux once the metal is molten. > EXCEL and HIMELTcrucibles are manufactured from premium grade raw materials to ISO9000:2000 quality standards. As soon as the crucible has been pre-heated as specified, charge and melt immediately. Charge light scrap and returns first in order to form a cushion for heavier material. Use tongs to charge ingots and place large pieces and ingots vertically allowing space for expansion. Only add flux once the metal is molten and use the minimum quantity required to obtain good metal quality. > *Detailed information on these products is available by request
Open the catalog to page 1All Morgan Molten Metal Systems catalogs and technical brochures
-
Morganite® Crucibles
32 Pages
-
Noltina® Crucibles
32 Pages
-
Noltina® Crucibles
32 Pages
-
Alustar E50
2 Pages
-
ResCoat Coating
2 Pages
-
Z2e² PRO Coating
2 Pages
-
Degassing Rotors
2 Pages
-
Syncarb Z2 e2
1 Pages
-
Ladle Liners
2 Pages
-
Stabil
2 Pages
-
Grafit
2 Pages
-
Excel & Himelt
8 Pages
Archived catalogs
-
Morgan MMS Furnace Range
4 Pages
-
Crucible Lifter
2 Pages
-
Ingot Loader
1 Pages
-
Foundry Products
2 Pages
-
Ultramelt Crucible Brochure
6 Pages
-
Crucible Accessories
4 Pages
-
Excel HiMelt Brochure
6 Pages
-
IsoAlustar Crucible Brochure
6 Pages
-
Salamander Crucible Brochure
4 Pages
-
Ultramelt Crucible Brochure
4 Pages
-
Indux Crucible Brochure
4 Pages
-
Starrbide Crucible Brochure
6 Pages